Why Stainless? Its Benefits and Unique Characteristics
Construction hardware. Kitchen appliances. Consumer electronics. Medical and dental instruments. These are just a few of the many products manufactured with stainless steel that people rely upon every day.
There are many reasons why stainless steel is so common, including its temperature resistance, corrosion resistance, and sustainability. Additionally, it can be engineered with extremely precise tolerances and properties, so stainless has solidified itself as a crucial component of countless industries and applications.
All the Basics About Stainless Steel
Stainless steel alloy materials are high strength (tensile and yield) and have excellent pitting corrosion resistance. Each alloying element adds its own properties, and when tempered with heat treatment and forming processes like rolling and shaping, stainless steel products become ideal for a nearly limitless number of applications.
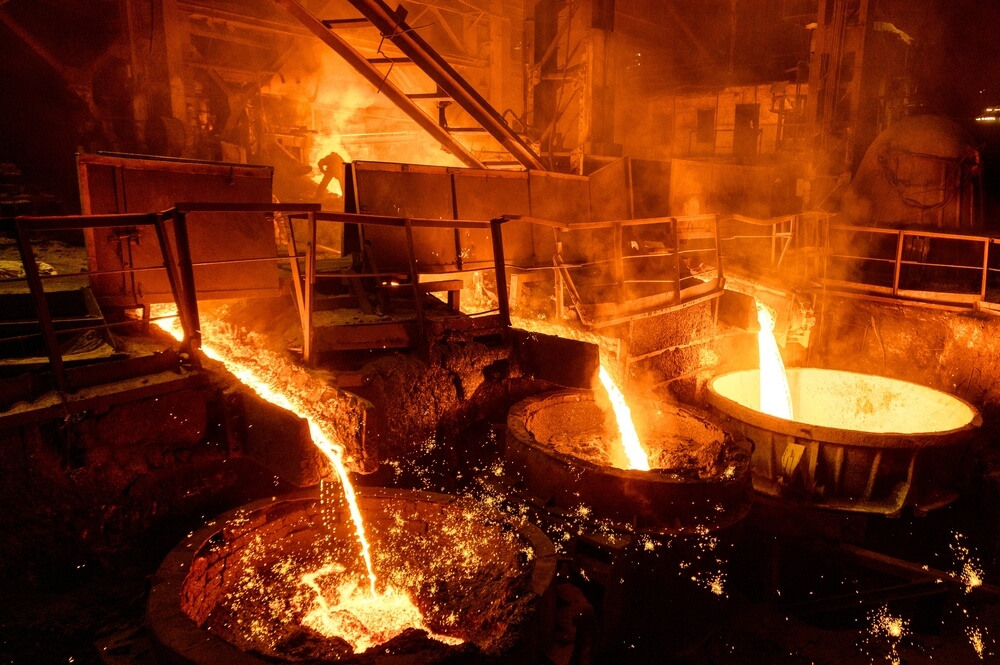
How to Fabricate Stainless Steel
The stainless-steel production process starts when a steel mill melts down scrap and raw materials like iron, carbon, chromium, and nickel in large crucibles.
Once melted, excess carbon is removed from the mixture. The compound is turned and stirred to evenly distribute the elements and ensure uniform quality. Then, it is cast into big slabs that can be made into billets for forging, sheet, or, for our purposes, rolled into coils.
Cold rolling mills like Ulbrich process stainless steel coil, adjusting its thickness and imparting other mechanical process suited to the customers specifications or application. Cold rolling refers to metal processing imparted under 300° while most hot rolling is done by the melt mills themselves. Once surface finishes are applied and any other value-added processing is completed, the material is ready to use.
History of Stainless Steel
Oddly enough, stainless steel was invented accidentally. In 1913, British metallurgist Harry Brearly was tasked with creating a new alloy with higher corrosion resistance for use in the English military’s guns and artillery. He added chromium to iron, noticed the alloy didn’t rust, and thus stainless steel was born.
The following year, European manufacturers started using stainless steel to produce knives and cutlery. As the decades passed and the metal industry evolved, stainless was used for military tanks, surgical implements, turbine blades, and even as a flood barrier on the river Thames. Fast forward to today, where stainless steel has countless applications across countless industries.
Thanks to technological advancements, stainless steel material is now widely used—and in many cases, it has even overtaken the usefulness of other steel.
The Difference Between Stainless Steel and Carbon Steel
There are several differences between stainless steel and ordinary steel, and perhaps the most important is the material’s ingredients. While all steel contains iron and is alloyed using carbon, stainless contains at least 10% chromium. In fact, stainless’s chromium content is what makes it so resistant to corrosion and extreme temperatures. That’s because when chromium is exposed to oxygen it creates an inert and protective layer of Cr2O3 on the metal. This passive layer is what keeps stainless steel from rusting.
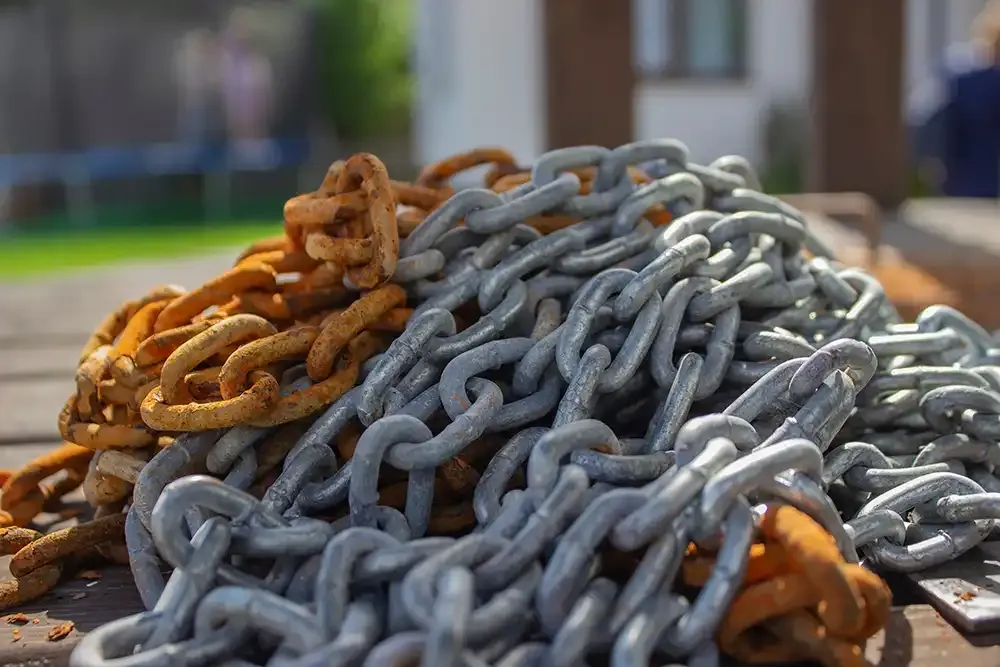
Although stainless is softer than carbon steel, different types provide plenty of applications. Materials like austenitic stainless steel or ferritic stainless steel and each different stainless steel grade has different properties, each of which are useful in countless applications.
Properties of Stainless Steel
Stainless steel is classified into different grades depending on their chemical makeup, particularly their percentages of carbon, chromium, and nickel. For example, austenitic stainless is the most common type and is graded as a 300 series stainless, containing up to 30% chromium and 6% nickel. Further, ferritic, and martensitic stainless steel are both 400-grade material and contain 11%-12% chromium. Each type has unique properties, including:
- Excellent corrosion resistance
- High tensile strength
- Durability
- Temperature resistance
- Easy formability and fabrication
- Longevity with little required maintenance
- Environmental friendliness
- Great aesthetic appearance
Despite these advantageous properties, there are some factors that make stainless steel difficult to work with. For example, its high tensile strength and plasticity can make it difficult to machine. Additionally, since it holds onto high temperatures, it takes time to cool down before it can be formed and finished. However, in most cases, the advantages of stainless steel greatly outweigh the disadvantages.
Evaluating the Properties of Stainless Steel
Tensile testing is one of the most common methods we use to determine whether the mechanical properties of a stainless-steel alloy product are optimal for our customers. This test helps assess how stainless steel will perform under tensile (stretching or pulling) forces, which is crucial for designing and ensuring the quality and safety of stainless steel components.
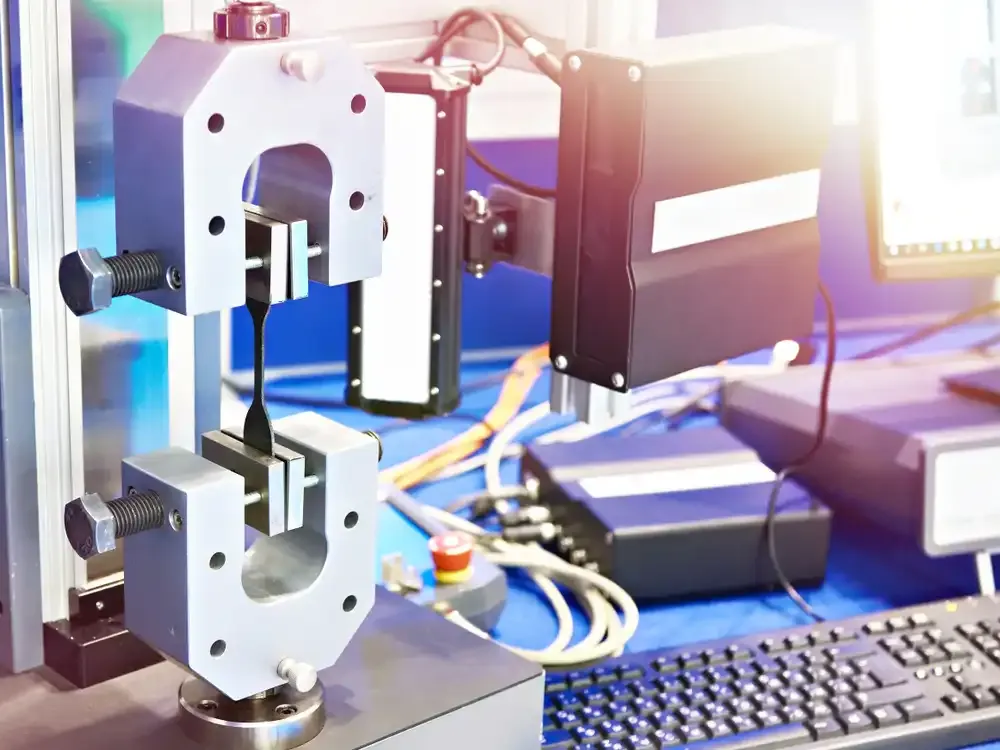
Overview of how tensile testing for stainless steel is conducted:
1. Sample Preparation: A small, standardized specimen of the stainless-steel material, often in the form of a cylindrical or flat test piece, is prepared. The specimen should have specific dimensions and be free from defects or irregularities that might affect the test results.
2. Mounting the Sample: The prepared specimen is securely mounted in the testing machine, which consists of two jaws – one fixed and one movable. The specimen is clamped between these jaws.
3. Application of Force: The testing machine applies a tensile force (tensile load) to the specimen by pulling it apart along its axis. The force is applied gradually and continuously until the specimen fractures. During this process, various parameters are measured and recorded:
- Stress: Stress is the force applied per unit of the original cross-sectional area of the specimen (expressed in Pascals or psi). It provides information about the material's ability to resist deformation under tension.
- Strain: Strain is the relative change in length of the specimen as it is stretched, divided by the original length. It is often expressed as a percentage. Strain helps determine the material's ductility and how it responds to deformation.
4. Recording Data: Throughout the test, data such as the applied force, elongation (change in length), and the corresponding stress and strain values are recorded. These data points are used to generate stress-strain curves.
5. Stress-Strain Curve: The stress-strain curve is a graphical representation of the material's behavior under tension. It provides valuable information about its mechanical properties, including the following key points:
- Yield Strength: The point on the curve where the material begins to deform plastically.
- Ultimate Tensile Strength (UTS): The maximum stress the material can withstand before fracturing.
- Elongation and Reduction in Area: These parameters indicate the material's ductility. Elongation is the percentage increase in length at the point of fracture, and reduction in area is the percentage reduction in the cross-sectional area of the specimen at that point.
6. Fracture: The test continues until the specimen fractures. The type of fracture (ductile or brittle) and the location of the fracture can also provide valuable insights into the material's behavior.
Tensile testing is a fundamental method for characterizing stainless steel and other materials in various industries, including manufacturing, construction, and engineering. It helps engineers and materials scientists understand how a material responds to tensile forces and is essential for quality control, material selection, and design considerations.
The Different Microstructures of Stainless Steel
The microstructure of stainless steel can vary depending on its composition and heat treatment. However, the three aforementioned groupings of stainless-steel grades (austenitic, ferritic, and martensitic) each have distinct microstructures.
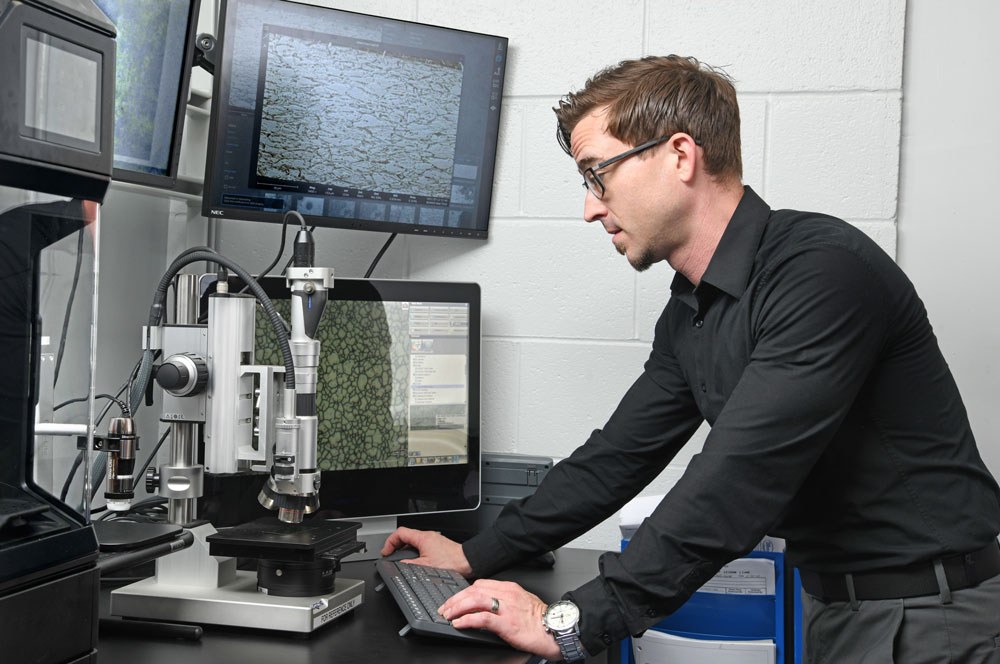
1. Austenitic Microstructure
- Austenitic stainless steel has a face-centered cubic (FCC) crystal structure at room temperature. In the microstructure, this results in a densely packed arrangement of atoms.
- Key Characteristics:
- Non-magnetic.
- Excellent corrosion resistance.
- Good toughness and ductility.
- This microstructure is stable at both high and low temperatures, making austenitic stainless steel suitable for a wide range of applications.
2. Ferritic Microstructure
- Ferritic stainless steel has a body-centered cubic (BCC) crystal structure at room temperature, with iron atoms arranged in a less tightly packed manner than in austenitic steel.
- Key Characteristics:
- Magnetic.
- Good corrosion resistance, especially in oxidizing environments.
- Lower toughness and ductility compared to austenitic stainless steel.
- Ferritic stainless steel is often used in applications where magnetic properties are desirable or in environments where corrosion resistance is needed.
3. Martensitic Microstructure
- Martensitic stainless steel exhibits a body-centered tetragonal (BCT) crystal structure, resulting from a phase transformation that occurs during rapid cooling or mechanical deformation.
- Key Characteristics:
- Magnetic.
- High hardness and strength.
- Lower corrosion resistance compared to austenitic and ferritic stainless steels.
- This microstructure is commonly found in cutlery and knives, where hardness and sharpness are essential properties.
These are the three primary microstructures found in stainless steel. However, some stainless steels may have mixed microstructures or be intentionally heat-treated to achieve specific properties, such as precipitation-hardening stainless steels, which undergo a controlled process to form fine precipitates in the microstructure, enhancing their strength and hardness. Additionally, duplex stainless steels have a combination of both austenitic and ferritic microstructures, offering a balance of properties.
The choice of microstructure depends on the intended application and the desired combination of properties, including corrosion resistance, strength, and magnetic characteristics.
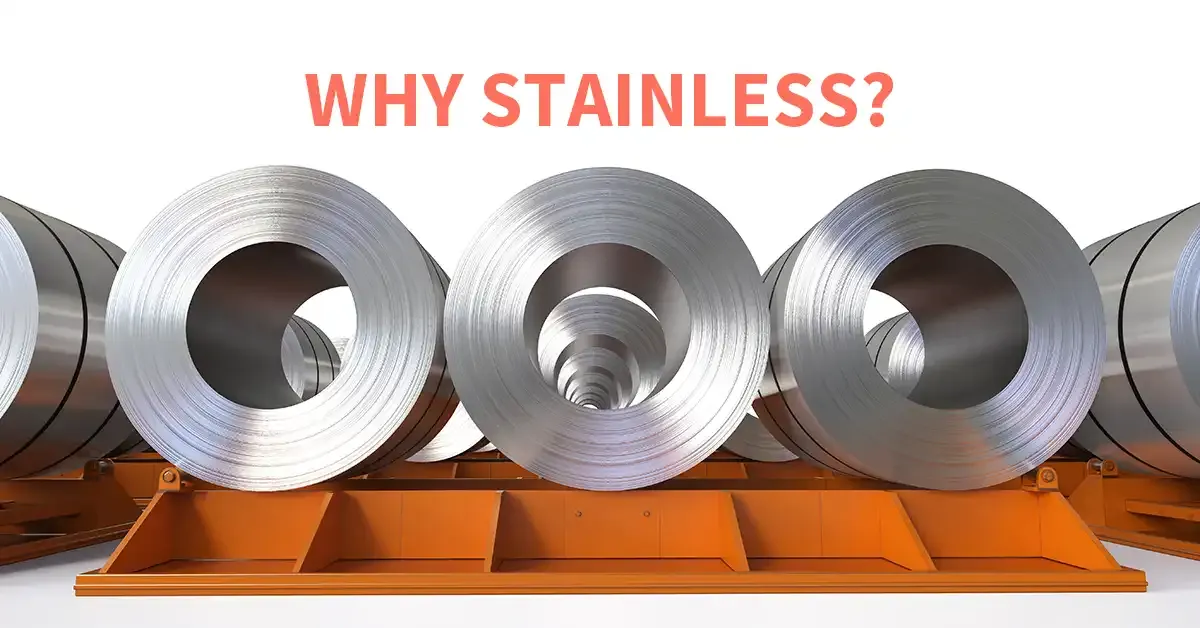
Advantages and Disadvantages of Stainless Steel
In addition to the manufacturing challenges of stainless steel, it is an expensive material to produce. However, there are many more advantages than disadvantages, which is perhaps why stainless is such a popular component with such a wide breadth of uses.
In addition to being resistant to corrosion and high heat, stainless steel is hygienic. Some types of precipitation hardening stainless steel, such as 17-7ph stainless steel, are particularly easy to clean and sanitize. This is crucial in applications like medical and dental implements, food production equipment, and inside consumers’ homes.
This is because stainless steel has a smooth, non-porous surface, which means there are no microscopic openings or irregularities in the material where contaminants can hide. It’s resistant to a wide range of chemicals and cleaning agents, plus its non-reactive surface does not impart any flavors, odors, or contaminants to the materials it meets.
What’s more, stainless steel is sustainable. While traditional steels create a large carbon footprint, stainless is 100% recyclable. It can be melted down and reproduced over and over again, creating an unending ecofriendly product.
Most Common Uses of Stainless Steel
Although carbon steel has its place in many applications, stainless is more popular thanks to its many advantages. The cold rolling process can yield all sorts of products that are used by many industries, including:
- Architecture and construction industries: Roofing, storage tank cladding, handrails, and countertops.
- Automotive and transportation industries: Exhaust systems, fuel tanks, and catalytic converters.
- Medical and dental industries: Surgical steel tools, implants, and equipment that must be sanitized.
- Energy and heavy industries: Heat exchangers, turbines, and valves.
- Food and catering industry: Kitchen utensils and appliances, as well as food packaging.
In other words, there is no challenge too large for stainless steel.
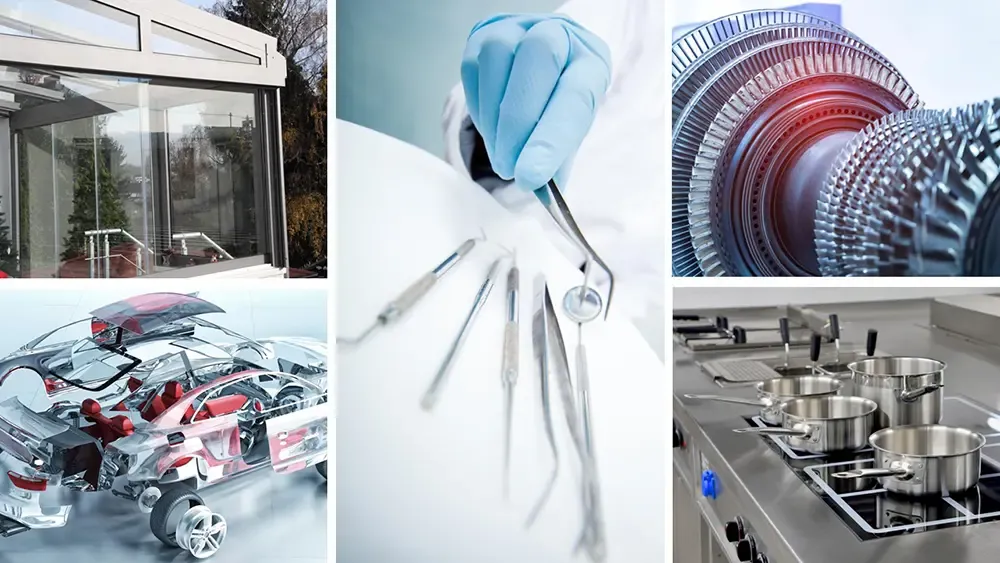
Answers to Your Stainless Steel Questions
Stainless steel has become an extremely valuable and common material. Although some metals have advantages over stainless in certain applications, few are used as widely as stainless. And if you have questions about stainless steel, look to Ulbrich for the answers!
For more information about stainless steel, contact an Ulbrich specialist today.