Titanium Meets the Challenges of Military Aerospace Manufacturing
“If stainless, nickel, and cobalt alloys don’t meet your performance requirements, chances are titanium will.” Ron Brucker, a senior metallurgist here at Ulbrich once said. The truth is that Titanium can withstand corrosive elements that are no match for the other alloys, and with the strength of steel at half its weight, it can also be used where strength-to-weight ratios are critical.
As a manufacturer, you have specific requirements for your project, so choosing the best alloy for your application is key to having an optimized final product. When it comes to designing parts for the aerospace industry, you need a material that is lighter, yet stronger, and holds up to hotter temperatures, all while allowing planes to fly faster and more efficiently than ever. This is where Titanium shines.
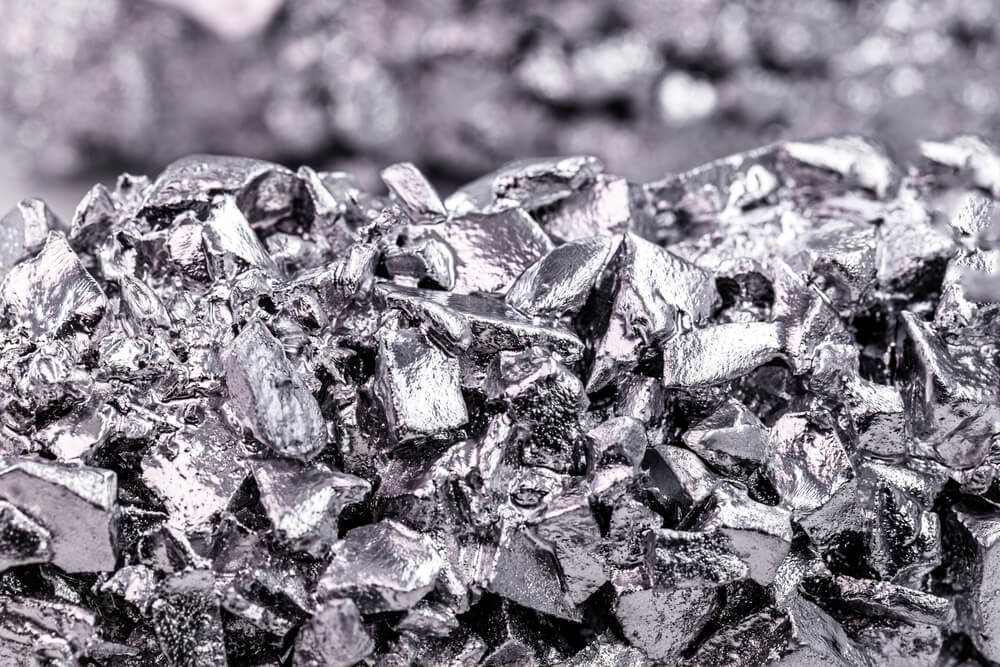
The inception of Titanium dates back to 1791, unknowingly first discovered by geologist Rev. William Gregor. Four years later, it was officially named ‘titanium’ by German scientist Martin Heinrich Klaproth. The name originates from the word 'Titan' which comes from the Greek Mythology beings known as 'Titans', which were extremely strong and resilient.
The material’s strength and weight make it preferred for many aerospace and aircraft parts. Still, like other high-performance alloys, processing titanium into metal is a lengthy process and costly, sometimes over 30 times more expensive than stainless and notably unstable.
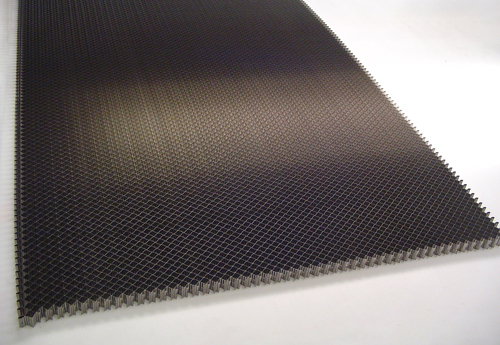
However, there is one technique that exploits the material’s strength and keeps costs down – honeycomb panels. Made from corrugated, precision width strips, matched up against each other, then brazed or welded where one flat area fits up against the other, the panels provide maximum openness, strength per pound, and lightness. The honeycomb panels provide noise abatement and insulation when used as shrouds around aircraft engines. A mounting case for a military missile is one example.
Titanium is an amazing material which has unique properties that make it highly sought after in the production of many modern and innovative applications such as this. It’s strong and light. The tensile strength of Ti is between 30,000 psi to 200,000 psi depending on the type of titanium. It is also low density; about 60% the density of iron, reducing load and strain of heavier metals while reducing the overall weight of the objects it is used to manufacture.
The military specifies titanium honeycomb panels to meet strength requirements for their missile mounting case. Titanium actually has the highest strength-to-density ratio of any metallic element, making it an excellent choice for this application. Ulbrich, a precision reroller who supplies Titanium for this application, uses technologically advanced rolling mills to roll the Ti material down in repeated passes to 0.004” (0.10-mm) gauge; we then use our slitting machines to slit the material to .75” (19-mm) widths. The part is further processed with a precision crimp being imparted into the strip, where it is then joined via resistance welding, layer after layer.
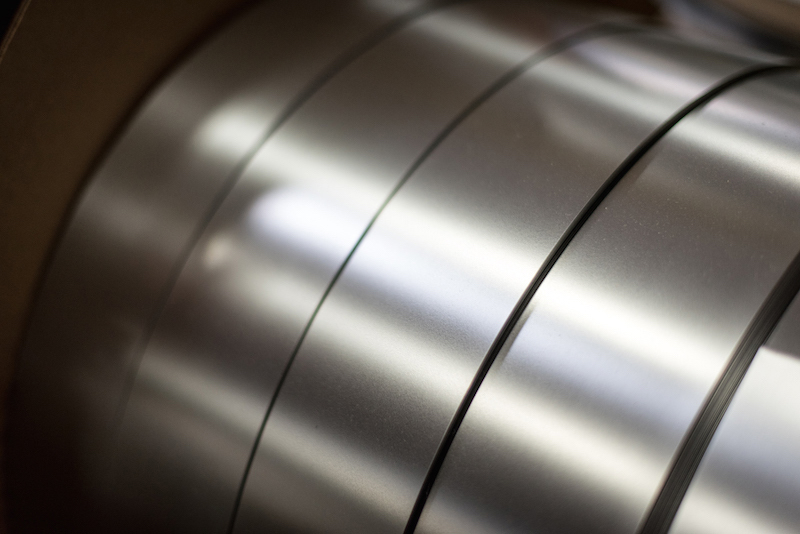
Titanium strip users in the military aerospace industry benefit from working with precision rerollers who have expertise in material thickness control, surface finish, formability, and deep supply chain partnerships. Typical thicknesses for honeycomb range from 0.001 (foil) to 0.007” (0.03 – 0.18 mm) with most of the demand on the thinner side of the range ±3 – 5% gauge tolerances in strip less than 1” (25 – mm) wide.
Titanium rerollers create a surface area that improves welding and brazing by shot-blasting rolls to a matte or brushed finish. Precision rerollers who serve this market must perform constant monitoring to ensure this precise, highly consistent finish. To control the formability of both chemically pure material and titanium alloys, processing or alloying methods are required in concert with cold working of the material. This is partly why Titanium is so difficult for rerollers—requiring deep expertise, experience, and equipment to produce with the precision characteristics demanded by military aerospace manufacturers. When the titanium material has been processed by the reroller, the formed material is then ready for drawing, punching, stamping, and forming on multislide and multiple-die-stamping equipment.
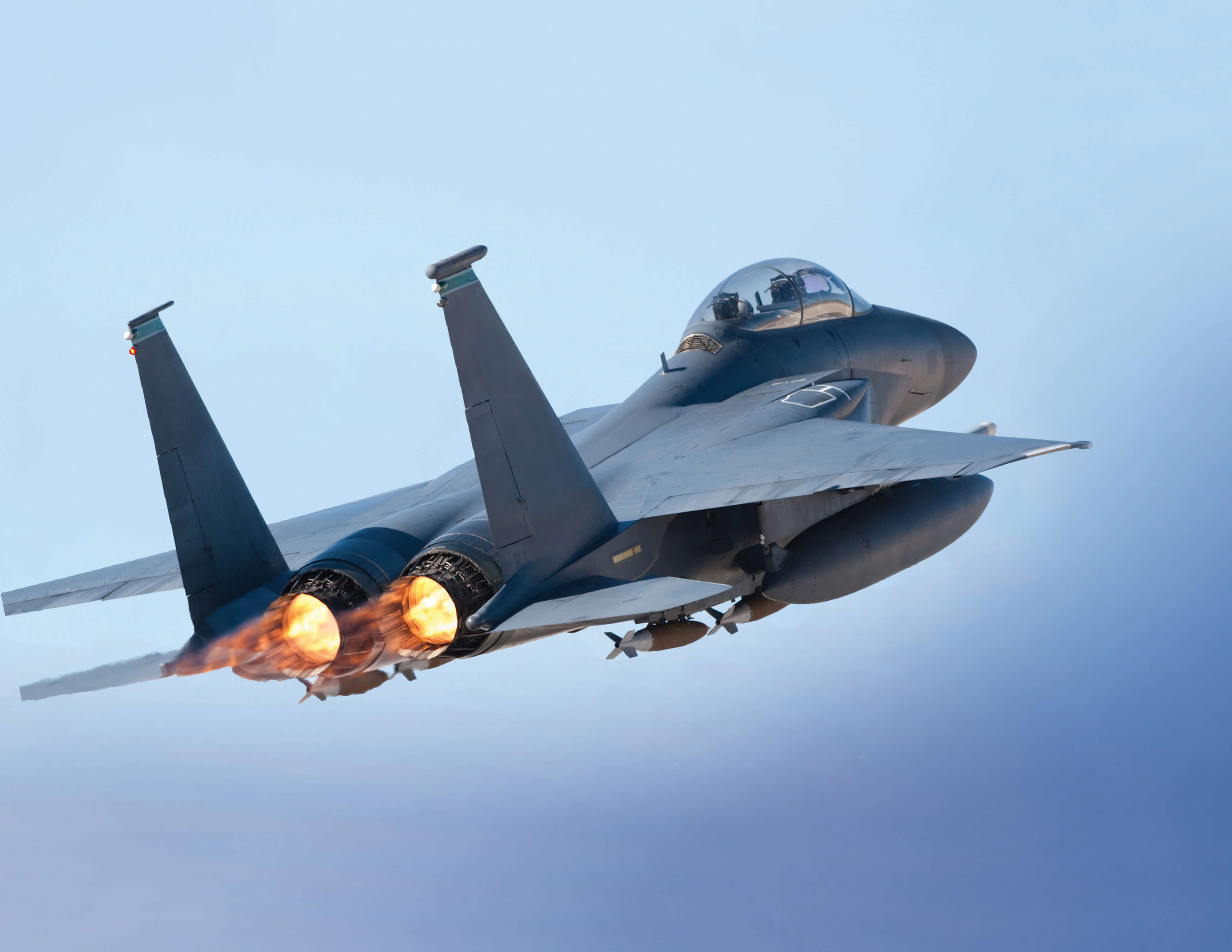
Titanium buyers benefit greatly from working with a precision reroller for their Ti needs. You may not need a 500 lb (225 – kg) coil of titanium, but buying from large producing mills usually means accepting a minimum coil of this size. The aerospace market has a growing need for titanium coiled strip and foil for the structural components fabricated to protect these airframes' engine components, but the high minimums required at large mills can be prohibitive.
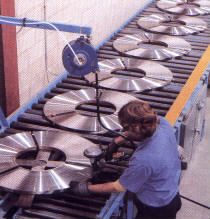
Working with a reroller who has a cultural commitment, in addition to the financial one required to be able to process this challenging metal can be extremely beneficial to part-makers within the aerospace industry. Ulbrich uses a service-center approach to slitting thin widths off mill-size coils and selling them in pancake or oscillate wound coils weighing under 60 lb (27 kg), putting the material within reach of fabricators. Ulbrich also uses less costly lengths of welded metals to start the coil so the roll gap is perfect by the time the titanium strip gets into mill stands. Slitting is done to precisely measured lengths for the same reason.
Ulbrich Stainless Steel & Special Metals, Inc. is a specialty reroller in metals fabrication quietly helping the titanium industry reduce costs so the work material can compete for nonmilitary applications. If you have a challenging application and wondering if Titanium or one of its alloys may be ideal to meet your requirements, speak to one of our in-house metallurgists today who would be happy to help you in your material evaluation and selection.