Titanium Grades: Everything Manufacturers Need to Know About Titanium Strip for Precision Applications
As a manufacturer in industries like aerospace, medical, automotive, or energy, choosing the right titanium grade for your application can make or break the performance and reliability of your products. Titanium’s combination of strength, light weight, and corrosion resistance makes it a cornerstone material for precision components—but not all titanium is created equal.
At Ulbrich, we understand the unique challenges manufacturers face when working with titanium strip coil. From optimizing material performance for stamping dies to achieving the perfect surface finish for medical implants, we’re here to help you select the ideal titanium grade and deliver it to your exact specifications. Let’s dive into the key factors and considerations that will help you make the best decisions for your applications.
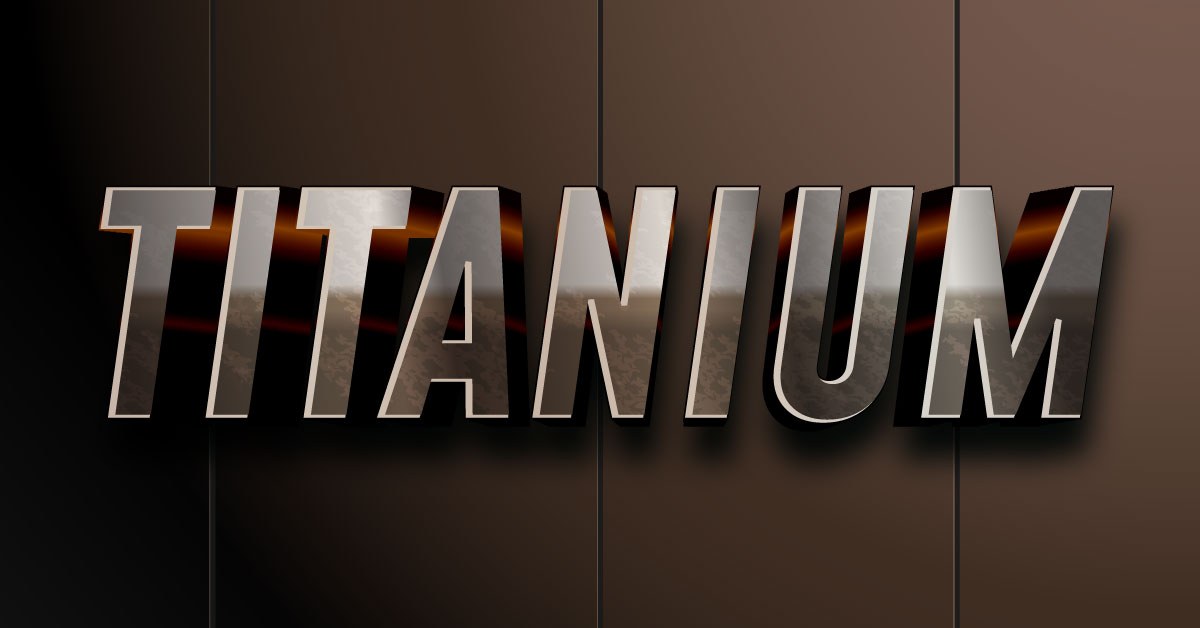
Challenges Manufacturers Face When Choosing Titanium Grades
Selecting the right titanium grade for your application can be a complex process. Manufacturers often encounter issues such as:
- Material inconsistencies that lead to tool wear and breakage during forming processes.
- High scrap rates due to cracking or poor formability.
- Surface defects that compromise the quality of aerospace or medical components.
- Confusion over grade selection, as each has unique properties suited to different applications.
- Supply chain challenges, including long mill lead times, which can delay projects and increase costs.
- Suboptimal material specifications, where titanium not manufactured to job-specific requirements leads to inefficiencies and waste.
These common challenges can lead to delays, increased costs, and customer dissatisfaction. That's why Ulbrich employs a team of metallurgists, supply chain experts, and engineers dedicated to supporting our customers at every stage. This proactive approach means that these sorts of obstacles are either identified and resolved quickly or prevented from happening at all. This allows our customers to maintain efficiency, reduce costs, and deliver high-quality products consistently.
Why Titanium's Lead Times Are So Long
Lead times for titanium can be up to three times longer than those for stainless steel, depending on the specific product and market conditions. For titanium, lead times often range from 12 to 20 weeks, while stainless steel products typically have lead times of 4 to 8 weeks.
This is due to several critical factors:
- Raw Material Scarcity: Titanium ore is less abundant and more challenging to extract and process compared to the iron used in stainless steel.
- Complex Production Process: The Kroll process used to extract titanium from ore involves more steps and time than the processes for stainless steel production.
- Specialized Manufacturing Equipment: Titanium’s high strength and low machinability require specialized tools and expertise, which limits the number of facilities equipped to produce titanium products.
- Custom Production Runs: Titanium is often manufactured in smaller, application-specific batches, unlike the high-volume production typical for stainless steel.
- Market Demand: High demand from industries such as aerospace and medical further strains production capacity, contributing to longer lead times.
These factors make planning and forecasting essential when incorporating titanium into your supply chain.
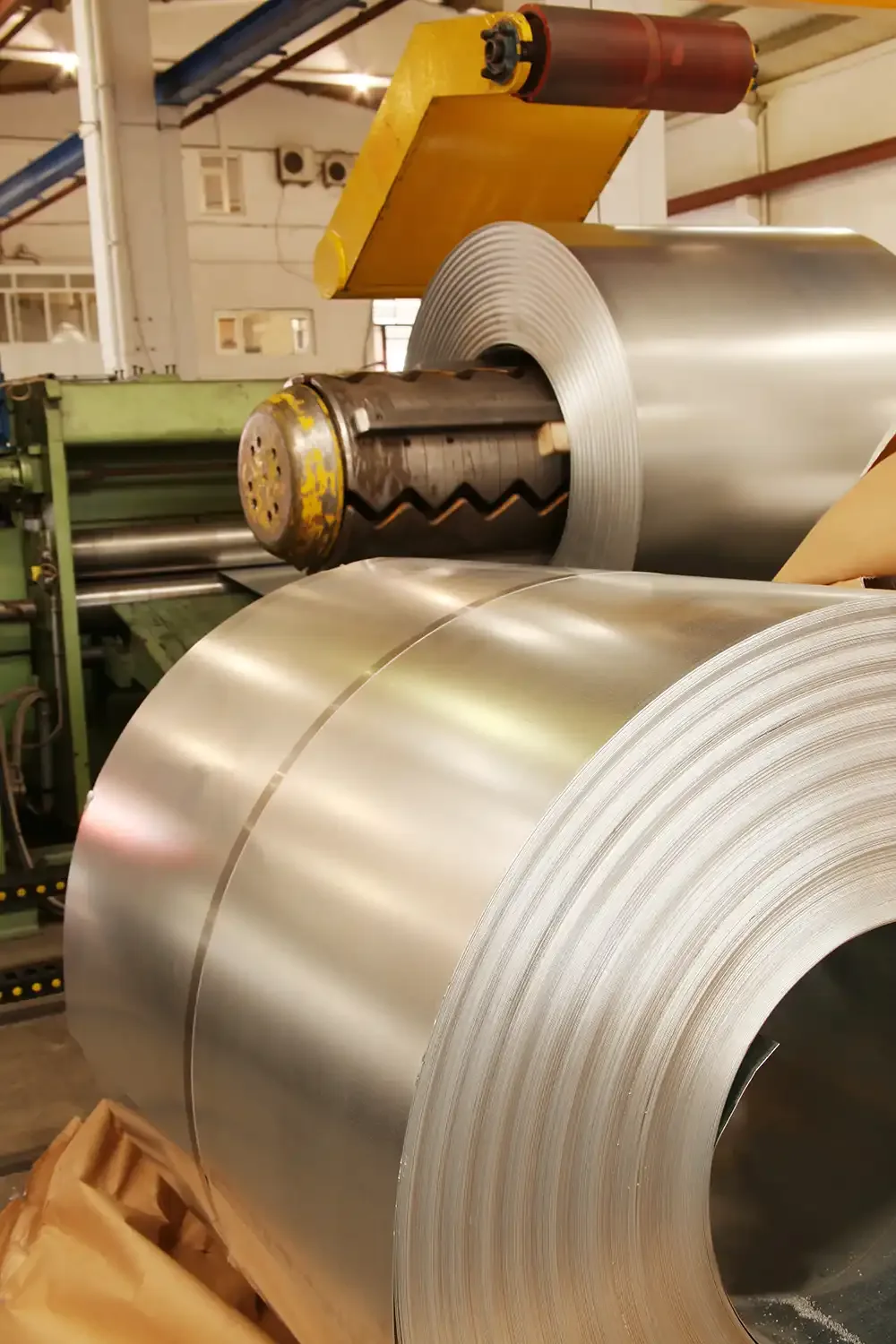
Understanding Grades of Titanium
Titanium is classified into grades based on its chemical composition and mechanical properties. Below is an overview of the most common grades and their applications:
Commercially Pure (CP) Titanium Grades 1–4
- Grade 1: The softest and most ductile grade, offering excellent formability and corrosion resistance. Ideal for medical implants and chemical processing equipment.
- Grade 2: A versatile grade that balances strength and ductility. Commonly used in aerospace and industrial applications.
- Grade 3: Stronger than grades 1 and 2 but less formable. Often selected for aerospace structures and industrial parts.
- Grade 4: The strongest CP titanium grade, used in aerospace and medical applications requiring high strength and corrosion resistance.
Alloyed Titanium Grades
- Grade 5 (Ti-6Al-4V): The most common titanium alloy, known for its high strength and excellent corrosion resistance. Widely used in aerospace parts, sports equipment, and marine applications.
- Grade 7: Enhanced with palladium for superior corrosion resistance. Frequently used in chemical environments and marine applications.
- Grade 9 (Ti-3Al-2.5V): A high-strength, lightweight alloy that compromises the ease of welding and manufacturing of pure grades and the high strength of Grade 5. Popular in aerospace tubing and high-performance automotive components.
- Grade 11: Combines corrosion resistance and low alloying elements, making it suitable for marine and energy applications.
- Grade 15-3-3-3 (Ti-15V-3Cr-3Sn-3Al): A beta titanium alloy known for its excellent fatigue resistance and structural integrity, making it a standout choice for critical applications. Its high strength and lightweight properties make it indispensable in aerospace and energy sectors for components exposed to cyclic stress and extreme conditions.
Each grade has specific advantages, and selecting the right one depends on your application’s strength, corrosion resistance, and formability requirements.
Alpha, Beta, and Alpha-Beta Titanium Alloys
Titanium alloys are categorized based on their crystal structure:
- Alpha Alloys: Contain neutral alloying elements like tin and are not heat treatable. They offer excellent weldability and are suitable for low-temperature applications. Examples include Commercially Pure (CP) Grades 1–4.
- Beta Alloys: Alloyed with elements like vanadium and molybdenum, these alloys are heat treatable and provide high strength. They are less formable than alpha alloys but are suitable for high-strength applications. An example is Grade 15-3-3-3 (Ti-15V-3Cr-3Sn-3Al).
- Alpha-Beta Alloys: Contain a mixture of alpha and beta stabilizers, offering a balance between strength and formability. Examples include Grade 5 (Ti-6Al-4V) and Grade 9 (Ti-3Al-2.5V).
While many titanium alloys are straightforward to categorize, some exhibit unique properties like metastability, for example Grade 15-3-3-3 (Ti-15V-3Cr-3Sn-3Al). The term "metastable" refers to a material state that is not the most stable form but remains stable under certain conditions unless disrupted.
This means that Grade 15-3-3-3 maintains a beta phase structure under room temperature or low stress but can transform to a more stable phase (such as alpha) if subjected to specific heat treatments or mechanical work. This characteristic enables the alloy to exhibit flexibility alongside exceptional strength, making it a standout choice for demanding environments.
Technical Comparisons Between Common Grades
To make informed decisions, it’s helpful to understand the detailed differences between commonly used titanium grades:
- Grade 2 vs. Grade 9: While Grade 2 offers excellent corrosion resistance and ductility, Grade 9 provides higher strength and is better suited for high-performance structural applications like aerospace tubing.
- Grade 1 vs. Grade 4: Grade 1 is preferred for applications requiring maximum ductility and formability, such as medical implants. In contrast, Grade 4’s higher strength makes it ideal for load-bearing applications in aerospace.
- Grade 5 vs. Grade 9: Grade 5 offers higher strength and is commonly used in aerospace parts, primarily due to its extensive documentation and military applications. However, its low formability makes it harder to work with compared to Grade 9, which is easier to weld and more cost-effective for precision production. Grade 9's balance of strength and manufacturability makes it suitable for diverse applications, from aerospace honeycomb structures to medical pacemakers.
- Grade 7 vs. Grade 11: Both grades excel in corrosion resistance due to their alloying elements. However, Grade 7 is better suited for aggressive chemical environments, while Grade 11 offers a balance of corrosion resistance and weldability for marine applications.
- Grade 15-3-3-3 vs. Grade 9: Grade 15-3-3-3 provides superior fatigue resistance and higher strength, making it the go-to choice for components under cyclic stress, whereas Grade 9 excels in lightweight structural applications.
These comparisons highlight how different grades perform under specific conditions, ensuring you can select the optimal material for your needs.
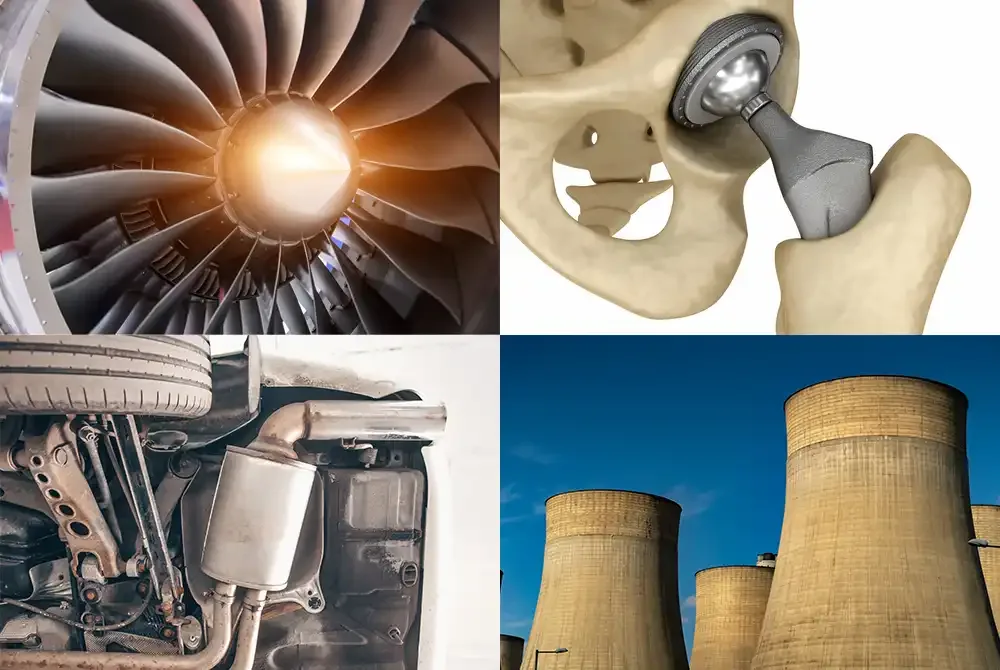
Applications by Industry
Aerospace
Titanium’s strength-to-weight ratio and ability to withstand extreme temperatures make it indispensable for aerospace components such as airframes, turbine blades, and engine parts. Grade 2 and Grade 9 are commonly used for their balance of performance and manufacturability.
Medical
For implants and medical devices, biocompatibility and corrosion resistance are critical. Grades 1 and 4 are often used for their reliability and compliance with ASTM and ISO standards.
Automotive
In the automotive industry, titanium is used for lightweighting and performance enhancement. Grade 9 is ideal for exhaust systems, suspension springs, and structural components due to its balance of strength, weight reduction, and cost efficiency.
Energy
Applications in energy, such as nuclear reactors and fuel cells, require titanium’s corrosion resistance and strength. Grade 7 is particularly well-suited for bipolar plates and heat exchangers.
Titanium vs. Steel: A Comparative Overview
When choosing materials, it's essential to compare titanium with other metals like steel:
- Density: Titanium has a density of approximately 4.51 g/cm³, which is about half that of steel (7.8–8 g/cm³), making titanium components lighter.
- Strength: While steel generally has higher tensile yield strength, certain titanium alloys, like Grade 5, offer comparable strength with significantly less weight.
- Corrosion Resistance: Titanium exhibits superior corrosion resistance, especially in harsh environments, compared to many types of steel.
- Cost: Titanium is generally more expensive than steel due to its processing requirements and desirable properties.
- Biocompatibility: Titanium is highly biocompatible, making it ideal for medical implants and devices, where compatibility with the human body and long-term reliability are essential. While stainless steel is also used in medical applications, titanium's superior biocompatibility often makes it the preferred material for implants that require prolonged interaction with human tissues.
Choosing between titanium and stainless steel depends on your application’s specific needs, including performance, weight, and cost. For applications requiring lightweight, corrosion-resistant, and biocompatible materials—where cost is less of a concern—titanium is often the superior choice.
However, stainless steel is often the better choice in applications where high tensile strength, ease of machining, material availability, and cost-effectiveness are priorities.
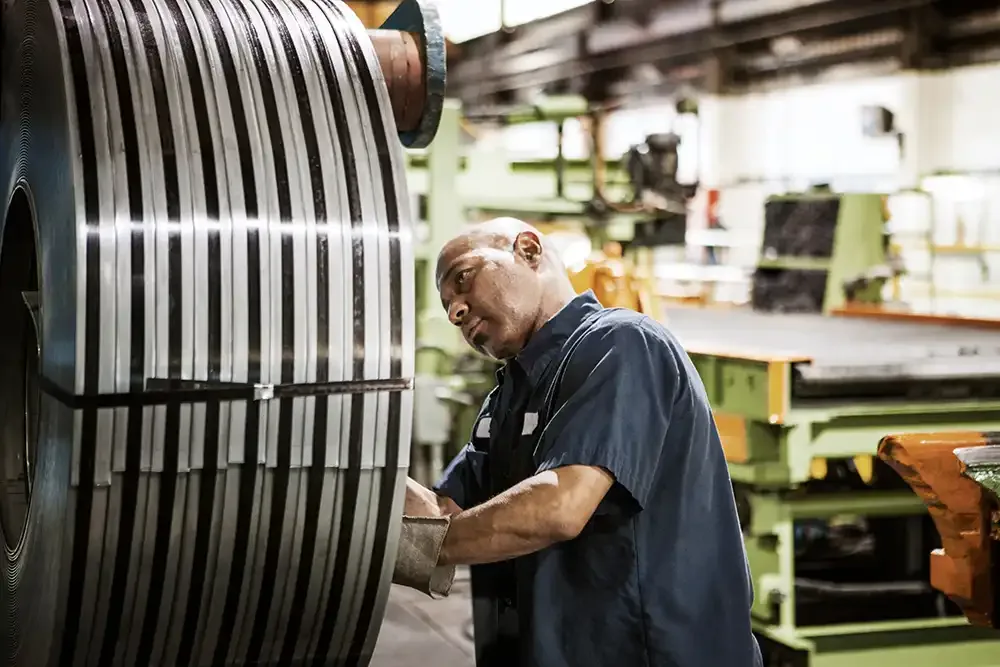
How Ulbrich Helps Solve Common Titanium Sourcing Challenges
At Ulbrich, we bring decades of expertise in producing precision titanium strip coil tailored to your needs. Here’s what sets us apart:
- Custom Mechanical Properties: We use advanced cold working and annealing processes to fine-tune strength, ductility, and formability.
- Precision Thickness and Width: Our titanium strip is rolled and slit to exact dimensions, ensuring compatibility with your tools and processes.
- Specialized Surface Finishes: From bright annealed to matte finishes, we deliver the ideal surface for your application.
- Comprehensive Grade Offering: We supply grades 1 through 4, 5, 7, 9, 11, 15-3-3-3, and more, ensuring the right material for any application.
Why Partner with Ulbrich?
By choosing Ulbrich as your titanium supplier, you can:
- Reduce Scrap Rates: Our consistent material quality minimizes waste.
- Extend Tool Life: Materials with precise mechanical properties reduce tool wear.
- Enhance Product Quality: Achieve superior results with titanium tailored to your specifications.
- Optimize Efficiency: Reliable, high-quality material means fewer production delays and higher yields.
- Avoid Pitfalls: Gain access to leading metallurgical, engineering, and sales support to fine-tune the materials you receive for your specific needs. This ensures optimal performance and helps you sidestep challenges often faced by those working with other suppliers.
If you’re ready to overcome the challenges of selecting and working with titanium strip coil, Ulbrich is here to help. Contact us to discuss your application and find the perfect titanium solution for your needs.