The Role of Formability and Ductility in Stamping Success
In the world of precision stamping, the interplay between formability and ductility is paramount to achieving manufacturing success. These material properties are not just technical jargon; they are critical factors that directly influence the efficiency and quality of the stamping process. Understanding and optimizing these properties can mean the difference between flawless production runs and costly errors.
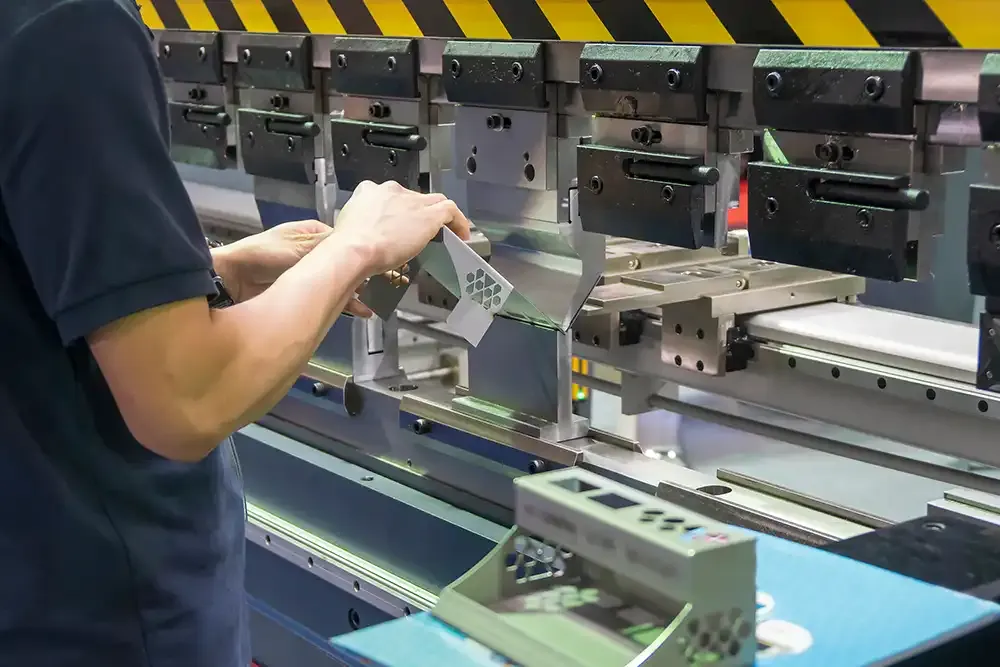
Understanding Yield Strength and Tensile Strength in Stamping
Yield strength and tensile strength are foundational to material selection and process design in stamping.
Yield strength is the stress level at which a material begins to deform plastically. Alloys such as 301 and 302 with chemistries designed for high tensile and high yield applications vs standard 304, 305, or 316 have dramatically different yield characteristics.
Tensile strength is the maximum stress a material can withstand while being stretched before breaking. For example, titanium alloys like Grade 5 (Ti-6Al-4V) offer high tensile strength and durability but can be challenging to work with due to their lower ductility. On the other hand, softer metals like alloys 5052 or 6061 balance moderate tensile strength with excellent ductility, making them a popular choice for applications requiring deep drawing.
Balancing these two properties is critical. Materials that are too strong may fracture, while those that are too soft may not maintain the necessary structural integrity for the application. Collaborating with metallurgical experts can help manufacturers select materials that align with the specific requirements of their projects.
How Formability Impacts Process Efficiency
Formability refers to a material’s ability to undergo plastic deformation without cracking. In stamping, this property directly impacts several key aspects of the process. Highly formable materials reduce stress on tooling, extending the lifespan of dies and presses. Certain grades of stainless steel, such as 304, are known for their excellent formability and can be processed more quickly, improving production throughput. Enhanced formability also minimizes defects such as wrinkling or tearing, resulting in higher yield rates.
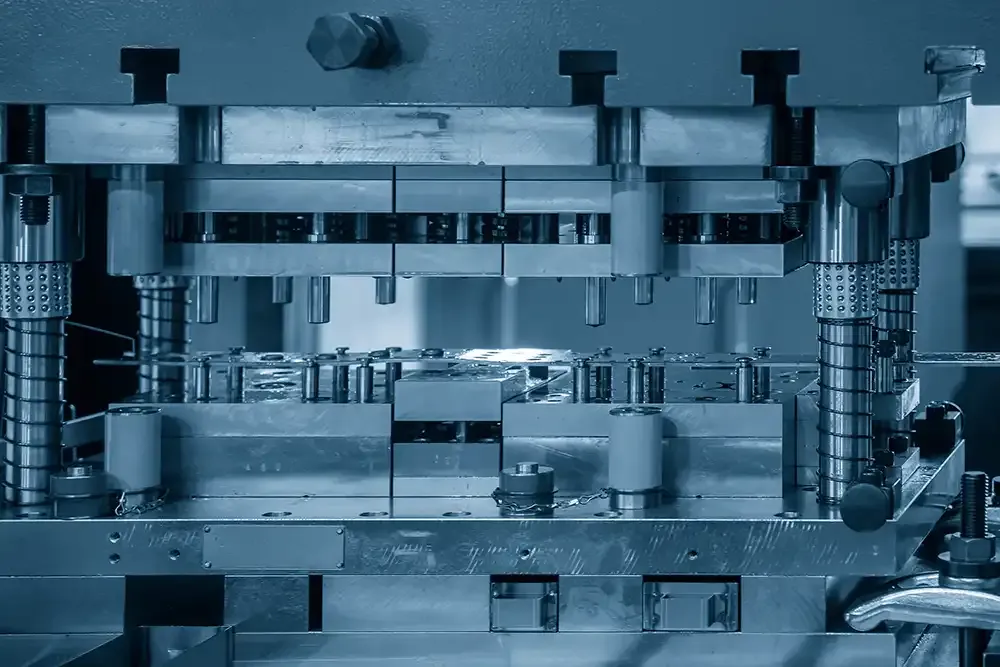
Materials like precipitation-hardened (PH) stainless steels and some 400 series steels are examples of heat-treated alloys that can be soft during forming and later hardened to achieve desired strength. This flexibility allows for easier processing during the stamping phase while maintaining high strength and durability in the final product. Although you have the advantage of forming the part in its softer state now you’re adding in the challenges related to the heat treatment of parts.
Optimizing formability requires a thorough understanding of material grades, thickness, and process conditions. Adjustments to lubrication, tooling geometry, and process parameters can significantly enhance material performance during forming.
Techniques for Evaluating and Testing Material Ductility
Ductility, or a material’s ability to stretch without breaking, is a crucial parameter in deep drawing and other complex forming processes. Closely related to ductility is elongation, which measures the extent to which a material can be stretched before it fractures. High elongation values are indicative of good ductility, making materials suitable for complex shapes and deep drawing operations. Key techniques for evaluating ductility include tensile testing, which provides data on elongation and reduction of area as direct indicators.
Proper testing ensures that materials meet the stringent requirements of precision stamping operations. Monitoring elongation values helps identify potential issues with material quality early, preventing costly downtime.
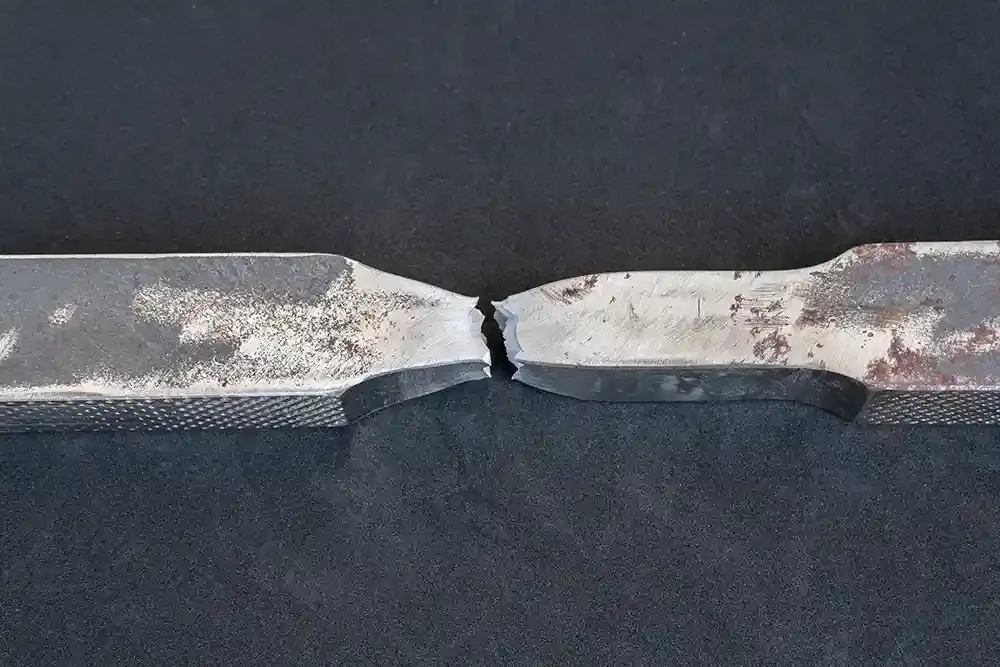
Troubleshooting Common Forming Issues in Deep Draw Processes
Deep drawing presents unique challenges, often revealing the limits of both material formability and ductility. Common issues include tearing, which is often caused by excessive tensile stress. This issue can be mitigated by using materials with higher ductility and adjusting blank holder pressure.
Wrinkling typically results from compressive stresses and can be addressed by optimizing tooling design and lubrication. Highly formable materials like 305 stainless steels are less prone to wrinkling when processed under proper conditions.
Springback, a common issue with high-strength materials like martensitic stainless steels, can be minimized through process adjustments and careful material selection. Working closely with material suppliers and leveraging advanced simulations can help troubleshoot and resolve these challenges effectively.
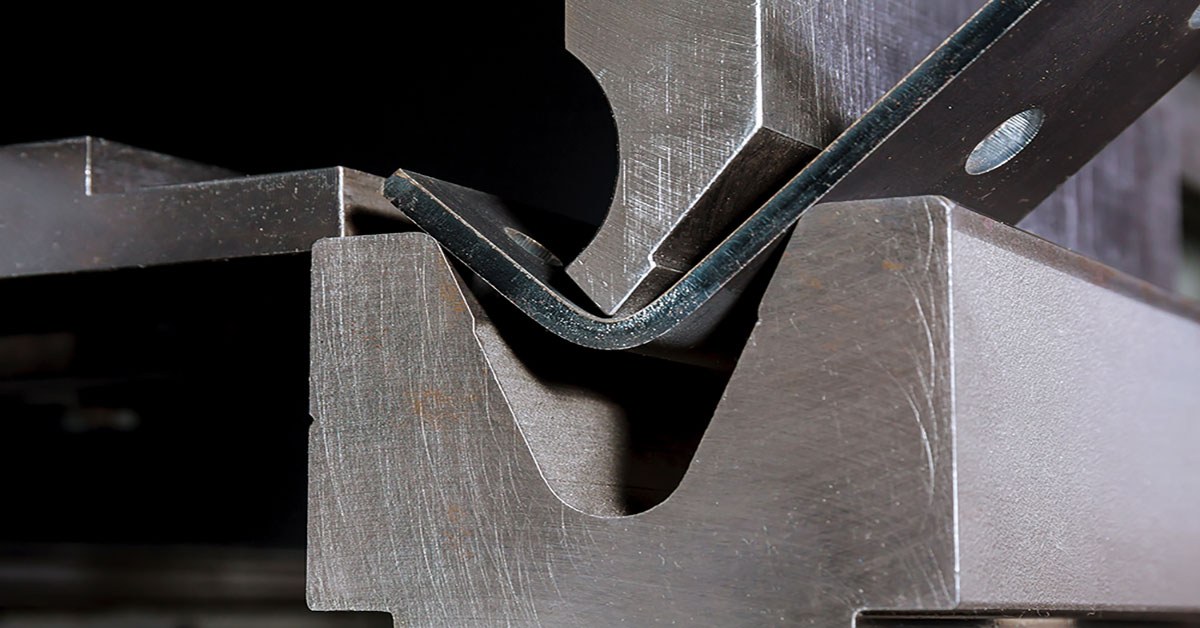
Achieve Success in Your Stamping Operations
Formability and ductility are at the heart of successful stamping operations. By understanding the nuances of yield strength and tensile strength, evaluating material properties through rigorous testing, and proactively addressing common forming issues, manufacturers can optimize their processes for efficiency and reliability.
Selecting the right material—whether it’s a formable stainless steel or a strong but manageable titanium alloy—is key to achieving your desired outcomes.
For expert guidance and high-performance materials tailored to your stamping needs, contact Ulbrich Stainless Steel & Special Metals today.