The Benefits of Shaped Wire for Stamped Parts Manufacturing
The stamping process, also known as pressing, typically involves continuously running flat metal in coil form through a tool and die. The output of that process results in a stamped product manufactured to the specification needed for the part. In some cases, manufacturers will also utilize blanks for their production, which are also used for individual stamping.
A stamping press is designed specifically for stamping metal parts out of raw material, and upon running material, a tool and die will form the metal into a specified shape. Several types of stamping techniques may be used to achieve an end product, including punching, blanking, bending, coining, and more. Each of these processes can be effective in arriving at the desired shape, however, there are different cost variables involved with each.
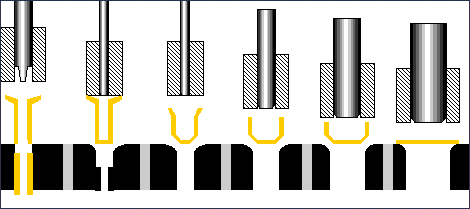
How Can Shaped Wire Benefit Stampers?
Starting with a Shaped Wire Product can supplement the stamping process by pre-rolling in features to the material that otherwise cannot be stamped in. This is a tremendous advantage to stampers as using a pre-formed profile will allow the stamper to start with a near-net shape, potentially replacing some initial stamping or forming steps. The elimination of these steps could increase overall production yield by reducing processing time, tooling costs, and scrap.
The Importance of Scrap Reduction
Today, far more manufacturers are focusing on reducing scrap from production. This is beneficial to the environment and the manufacturer's bottom line, while also giving customers the opportunity to see a reduction in cost and turnaround time which makes the manufacturer more competitive. As many stamping processes are multi-step, progressive processes, less scrap is typically produced when starting with a shaped wire product. Generally, using a shaped wire product can provide tighter tolerances over the alternative, which might help eliminate certain stages or steps in the stamping process that may otherwise be necessary when using regular flat material. This is possible through Ulbrich’s capabilities to pre-shape material.
At Ulbrich Shaped Wire, we produce a shaped material manufactured into its final profile by rolling round wire flat and then shaping the material by pulling or pushing the material through steel rolls. To start, we take round wire that progresses through the wire shaping process, where it is drawn down to what we require as our starting size. The drawing process elongates the wire and leaves an extremely low percentage of product leftover as scrap. This wire is then used to begin our rolling and shaping process. Fortunately, the overall scrap levels remain low, and this savings is essential as it helps provide our customers with the most competitive pricing we can offer.
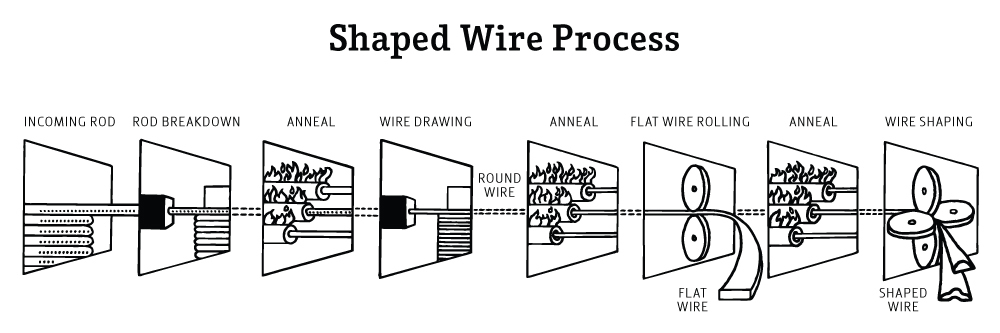
By combining this process with what a shaped or profiled product can offer, the stamper receives raw material that positions them very competitively once they begin running their jobs. This same benefit is afforded to our customers. When it hits their shop floor, the shape being near net allows them to avoid the scrap that would otherwise be produced by performing the operations to achieve the shape they need to start their manufacturing. This can be incredibly advantageous from a scrap prevention perspective but also has advantages in production speed.
How Shaped Profile Wire Minimizes Costly Machining
It's all about maximizing yield and reducing scrap. By rolling the material to shape rather than removing material, Ulbrich can take full advantage of the entire metal wire material. When machining metal products, there is ultimately a lot of material lost in the process. Unlike machining, when shaping wire to a specific profile, the process is essentially "squeezing" (and elongating) the material through a group of steel rolls/dies. The amount of material you started with is preserved. Since coils can potentially weigh a thousand pounds, the possibility of eliminating countless hours of machining time due to a near-net-shape result is very real.
Another benefit that the ability to pre-shape wire presents is in reducing costs due to the potentially high expense of tooling/dies. Quite often, tooling is the costliest part of the stamping process, outside of a press' initial cost. The dies must be acquired, and if there is a custom aspect to them, the time it takes to have them manufactured translates into even more cost. Suppose a pre-shaped product might afford the manufacturer the chance to eliminate the need to buy tooling while also reducing the number of potential die changes that must be made. In that case, there is an added cost reduction benefit to be had.

One good example of what Ulbrich can provide includes blade products for specific applications. For instance, a customer initially using a flat strip product needed to add processing to skive the edges. In contrast, Ulbrich was able to supply them with a shaped profile, allowing them to eliminate the additional edging operations. This was a boon to their entire manufacturing operation as it saved them a ton of time and money. Continue reading this other article to learn about the other advantages of using a wire product relative to strip.
Critical Steps for Quality Products Developed at USW
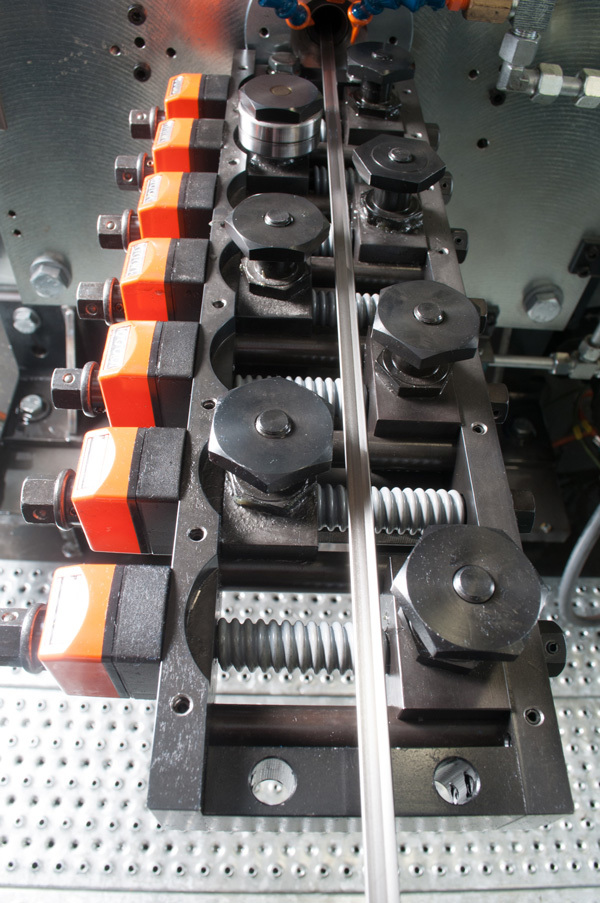
At Ulbrich Shaped Wire, we constantly analyze our operations and offerings in a never-ending quest to optimize what we do and innovate. We are extraordinarily data-driven and continually learning and iterating on the things we do and the products we sell.
On the customer side, developing a process that will provide a customer with value-added raw material begins with initial inquiry and investigation. Working together with our team of experts, Ulbrich Shaped Wire often takes concepts provided by our customers and works with them in a highly collaborative way to arrive at an outcome that will provide cost savings.
Technical conversations are very common as we ultimately want to provide a functional profile that saves costs for our customers. These conversations surround the determination of alloys, material properties, tolerances, and individual needs. We take extra care to review any specifications with our customers and our best-in-class engineering and metallurgy teams to ensure quality and compliance.
Upon agreement, a technical drawing is provided for approval to make sure that it meets our customer's needs. We also have a team of product managers available at all times throughout the development process for additional commercial support. Once we have ensured that we are aligned with our customers on the concept and material needs, we will produce the final profile.
Ulbrich Shaped Wire’s Role in Process Improvement
Metallurgical and technical excellence are high priorities at Ulbrich Shaped Wire. Our broad product offerings and robust supply line enables us to leverage a wide selection of alloys in our wire rolling mills, which furthers our rapid prototyping and custom wire profiling capabilities to develop superior wire for customers whether they require a standard or custom cross-section.
USW can provide material that may offer a stamper the opportunity to eliminate the need for tooling steps by getting the material closer to the final stamped part outcome. Improvements in both process time and cost reduction are seen when the amount of setup time due to the number of tooling changes is reduced. Additionally, we can add features to the profile that cannot be achieved during the stamping process. Some of these features might include rounded sections, bladed edges, or unique dimensional requirements. One of our most powerful capabilities is our ability to partner with our customers in order to understand their operations and material needs completely, which enables us to collaborate on the design of the wire material's profile to meet their needs and optimize their production processes. Starting with a "near net" shape may allow stampers to remove early press operations necessary when starting with a flat blank. Reducing the number of stamping operations may reduce processing time, tooling costs, and scrap.
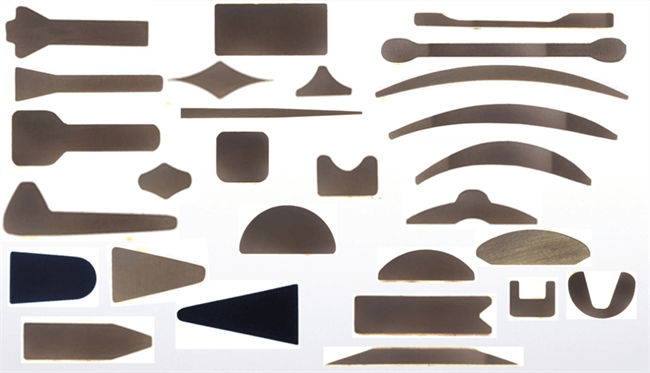
Ulbrich works with 300 series and 400 series stainless steels, Titanium, and Hi-temperature advanced Nickel Alloys such as Inconel and Monel. Overall, Ulbrich has worked with more than 165 alloys through the years. All tooling is custom manufactured in-house by our state-of-the-art New England tooling center. Some of the basic profiles that we provide include half rounds with special corner radii, rounded sides, bladed or razor-edged flats, wedge wire and Kamm profiles, and many other custom profile products. Depending on the profile's complexity, shapes are provided in net or near-net suitable for stamping, coining, forming, or machining. Continue learning how Ulbrich provides the highest value material by offering the least downtime and part variability, allowing our customers to produce higher quality products at a lower overall cost by downloading our Metal Alloys for Stamping & Deep Drawn Part Manufacturing Whitepaper, then contact us to discuss your stamping needs!