Smart Manufacturing: Leveraging Data and Automation in Metal Stamping
The metal stamping industry is undergoing a transformation, driven by advancements in smart manufacturing technologies. At the forefront of this evolution are data-driven insights and automation, which enable companies to achieve unprecedented levels of precision, efficiency, and uptime. By embracing Industry 4.0 principles, predictive maintenance, and cutting-edge automation trends, metal stampers can enhance their operations to meet the demands of today’s competitive marketplace.
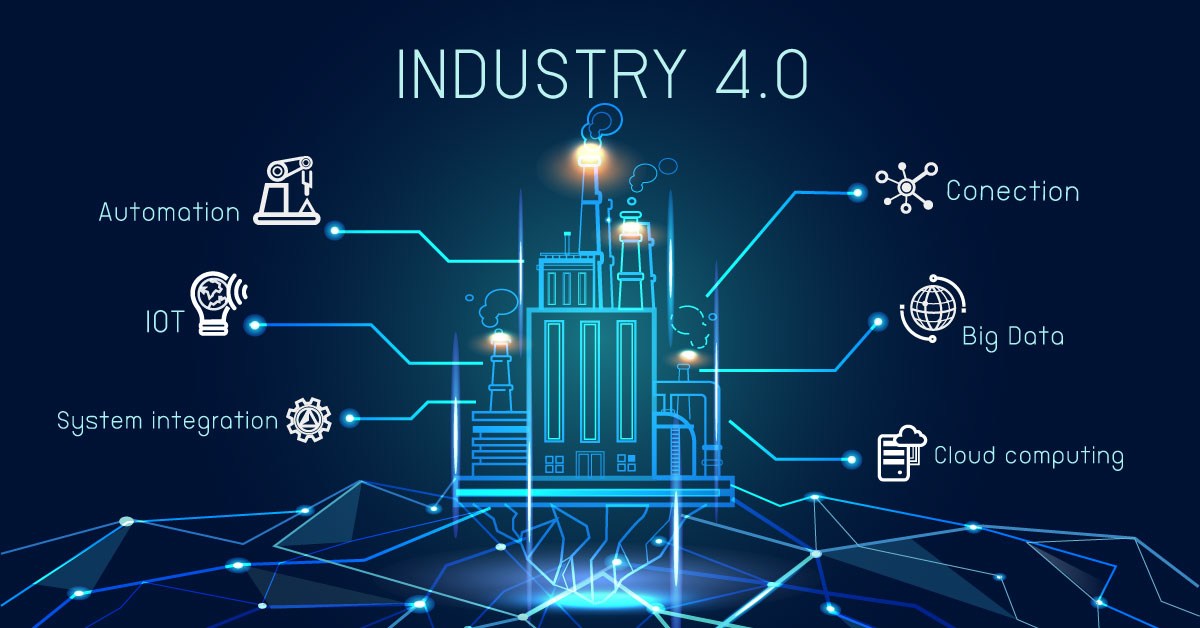
Industry 4.0 and Its Impact on Metal Stamping
Industry 4.0 represents the convergence of digital and physical technologies in manufacturing. For metal stamping, this means integrating smart sensors, IoT devices, and cloud computing into production processes. These technologies provide real-time data on equipment performance, material usage, and environmental conditions, allowing manufacturers to make informed decisions quickly.
One major benefit of Industry 4.0 is the ability to implement adaptive manufacturing. Through interconnected systems, metal stampers can adjust machine settings automatically to accommodate variations in materials or design requirements, ensuring consistent quality. Additionally, digital twins—virtual replicas of physical processes—can simulate operations and identify bottlenecks or inefficiencies before they occur, reducing waste and downtime.
Using Predictive Maintenance to Improve Uptime
Predictive maintenance is a game-changer for the metal stamping industry. By leveraging data from sensors and machine learning algorithms, manufacturers can predict when equipment is likely to fail and schedule maintenance proactively. This approach minimizes unexpected downtime and extends the lifespan of critical machinery.
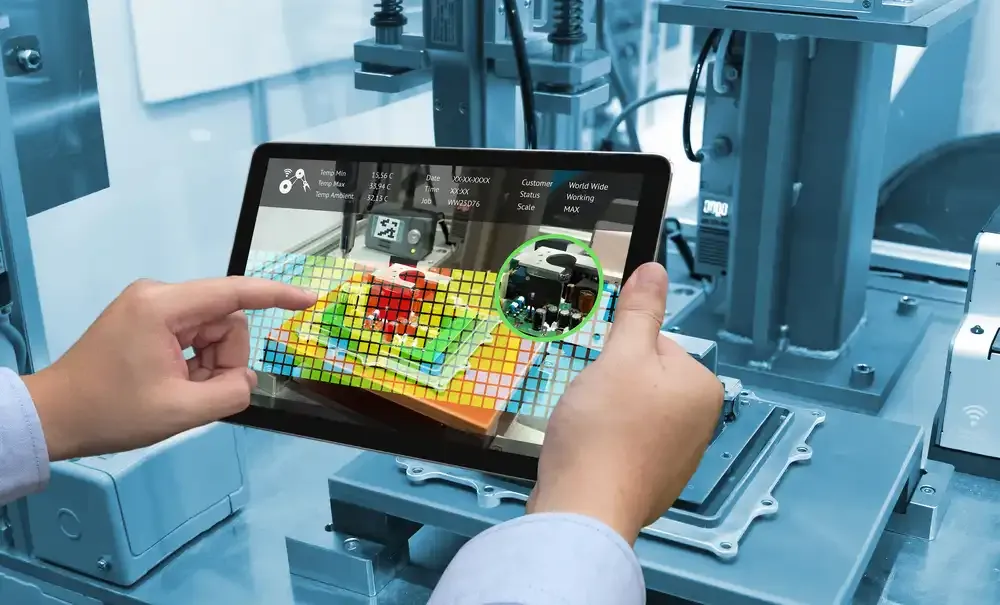
For example, vibration analysis, temperature monitoring, and lubricant condition tracking can provide early warning signs of wear or impending failure. Maintenance teams can then intervene before a breakdown occurs, ensuring uninterrupted production and reducing repair costs. Predictive maintenance not only improves equipment reliability but also boosts overall operational efficiency.
How Data Analytics Optimizes Manufacturing Efficiency
Data analytics is a cornerstone of smart manufacturing, offering actionable insights into every aspect of the metal stamping process. From material utilization to cycle times, analyzing data helps manufacturers identify areas for improvement and optimize resource allocation.
By tracking key performance indicators (KPIs), such as scrap rates and energy consumption, companies can pinpoint inefficiencies and implement corrective measures. Additionally, advanced analytics tools can forecast demand patterns, enabling better inventory management and production planning. With data as a guide, metal stampers can reduce waste, enhance quality, and lower operational costs.
Automation Trends and Their Benefits for Precision Metal Stampers
Automation is revolutionizing precision metal stamping by streamlining complex processes and reducing human error. Robotics, for instance, can handle repetitive tasks with unparalleled accuracy, while automated material handling systems improve workflow efficiency.
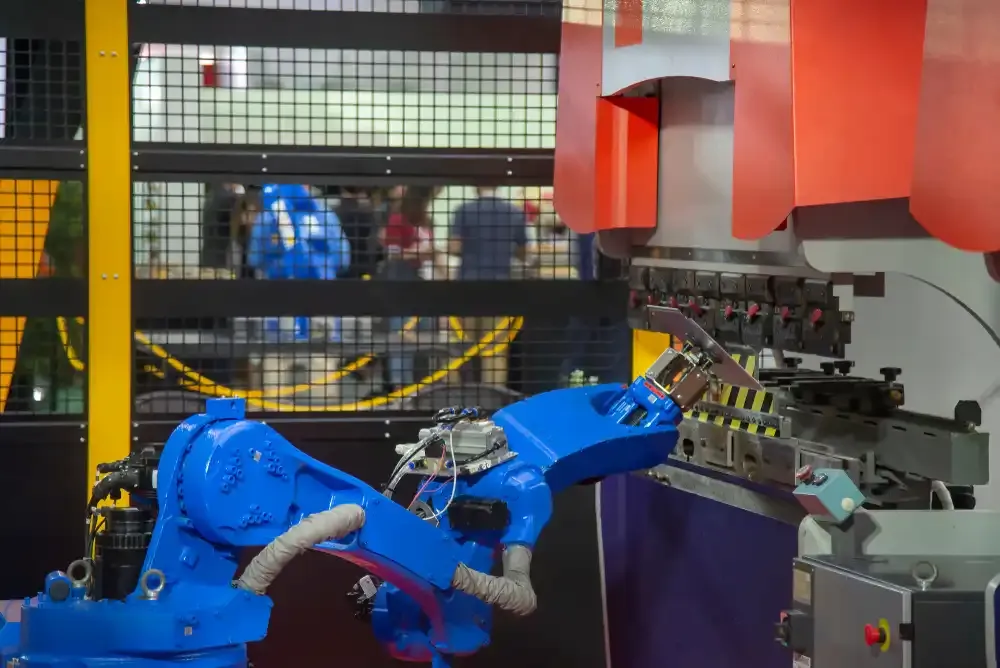
Collaborative robots (cobots) are another emerging trend, designed to work alongside human operators safely. Cobots can assist with tasks such as assembly, inspection, and packaging, freeing up skilled workers to focus on more strategic activities. Moreover, automated quality control systems equipped with machine vision technology can detect defects with microscopic precision, ensuring that every stamped part meets stringent standards.
The integration of automation not only enhances productivity but also enables metal stampers to scale operations without compromising quality. By adopting these technologies, manufacturers can remain agile and competitive in an ever-evolving market.
Ulbrich's Commitment to Smart Manufacturing
At Ulbrich Stainless Steels & Special Metals, Industry 4.0 principles are actively applied to processes such as rolling and annealing, with IoT sensors providing real-time data on material and equipment performance. This integration helps ensure consistent quality and reduce process variability.
Predictive maintenance practices are employed by analyzing equipment health data, such as temperature and vibration, to proactively address potential issues and improve uptime.
Furthermore, data analytics are utilized to track KPIs like energy usage and scrap rates, enabling operational efficiency improvements and waste reduction.
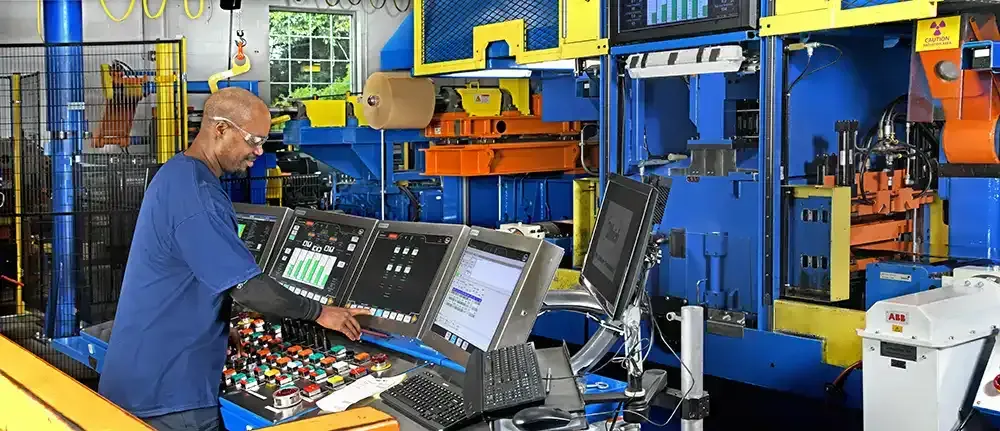
The Future of Smart Manufacturing in Metal Stamping
The fusion of data and automation is transforming the metal stamping industry, offering new opportunities for growth and innovation. Companies that embrace Industry 4.0 principles, predictive maintenance, data analytics, and automation will be well-positioned to thrive in the smart manufacturing era.
As a leader in specialty metals, Ulbrich Stainless Steels & Special Metals is committed to helping customers navigate these advancements. By providing high-performance materials and expert metallurgical support, we empower manufacturers to unlock the full potential of smart technologies.
To learn more about how Ulbrich can support your journey into smart manufacturing, contact us today.