Selecting Metals and Alloys for Medical Device Manufacturing
New technologies and clinical procedures demand more sophisticated metal components.
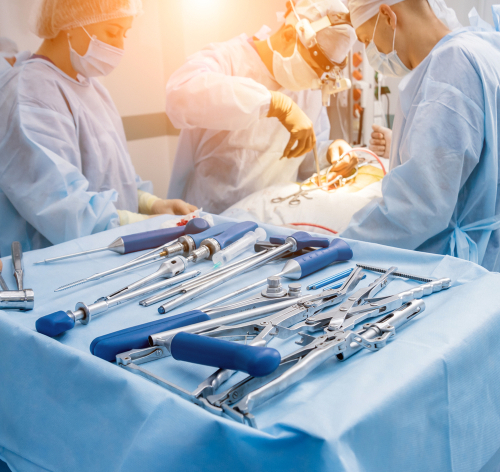
In recent years, suppliers of metal parts to the medical device industry have registered impressive gains in the quality of their performance. With the advent of statistical process control, ISO 9000 certifications and other initiatives, product quality of these alloys has never been higher.
Manufacturers of medical instruments and implantable devices have a wide array of useful metals to choose from today. Understanding the differences between these materials and the various possibilities each offers gives designers wide latitude in selecting the grade or alloy that most ideally suits the application. High strength and formability can be combined with clean, bright surfaces that promote sterile conditions.
Given the considerable difficulty of many of today’s surgical procedures and ever-present concerns about patient comfort and safety, device makers want assurances that the parts and materials they are buying are the absolute best for the job at hand. The growth of noninvasive and minimally invasive procedures, in which surgeons work without direct eye contact with the operating field, has put more emphasis than ever before on equipment that works the first time, every time, without a hitch.
Metal parts purchased through stamping houses and fabricators, along with the raw materials from which they are made, are coming under particular scrutiny because buyers are constantly searching for less costly, more efficient alternatives. Although plastics continue to make important inroads in the medical field – including replacing metals in some devices – metals remain indispensable to a great number of critical medical applications. Designers today can choose from an ever-growing array of metal materials and metal forms – a range of options available to help meet the medical equipment industry’s goals for higher quality levels and improved device performance.
How does metal selection play a role?
Metals are preferred for parts that must exhibit exceptional strength and stiffness, especially in small cross sections. They are also the best candidates for parts that must be formed or machined to intricate shapes, including blades, points, and probes; for mechanical parts that work in concert with other metal parts, such as gears, triggers, slides, and levers; for parts that are sterilized in high-heat atmospheres; and for any other parts requiring mechanical or physical properties exceeding those of polymer-based materials.
Metals typically offer a hard, bright surface that is conducive to easy cleanup and sterilization. The cleanliness requirements of most health-care applications rule out those metals that oxidize on the surface in an uncontrolled and destructive manner, such as steel, aluminum, or copper, and are the primary reason that materials such as stainless steel, nickel alloys, titanium, or titanium alloys are particularly prominent in the medical equipment field. These high-performance metals present special attributes, certain limitations, and tremendous versatility. Product engineers more familiar with the common metals or plastics will discover a wealth of possibilities in working with these materials, which frequently also require a fresh approach to design.
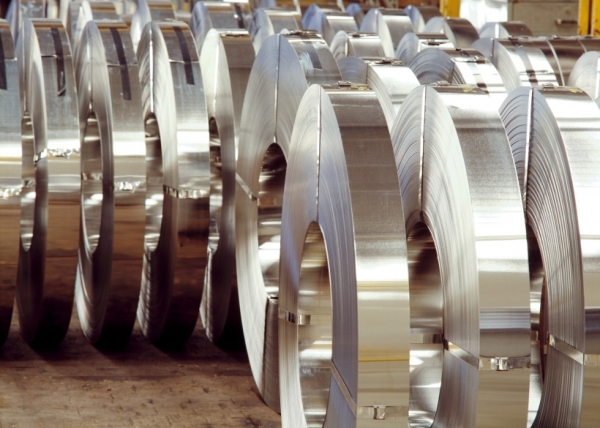
STAINLESS STEEL
When a metal part is indicated in the design of a medical instrument, the most common choice is one of the 300-series stainless steels. These alloys are essentially non-corrosive; offer a range of surface finishes, from reflective to matte; provide superior mechanical and physical properties; and are relatively easy to cold form or fabricate into specific parts.
Stainless-steel alloys contain from 17 to 25% chromium and from 8 to 25% nickel. The presence of chromium contributes to the corrosion resistance of the stainless steel by forming a tough, adherent, and invisible chromium oxide film on the alloy surface. If damaged mechanically or chemically, this film is self-healing. Additions of molybdenum of up to 7% are sometimes provided to further enhance corrosion resistance.
The most popular stainless-steel grades for medical parts are 301, 304, 304L, and 305. These versions are slightly different from one another in alloy composition, and the choice of which grade to use depends on formability, corrosion requirements, or availability in the thickness and temper required. Surface condition and strength are the other important design parameters.
Stainless-steel alloys can be cold worked to high tensile and yield strengths while retaining good ductility and toughness. At room temperature, they exhibit yield strengths between 30 and 200 ksi, depending on composition and the amount of cold work. Stainless grades designated “austenitic” or “martensitic” refer to the metallurgical structure of the metals after they are heated above their critical temperature and then rapidly cooled. The mixture of alloys and the time and temperature of the heat treatment determine the final structure. Austenitic stainless steels are more formable, whereas martensitic grades are harder and stronger.
Austenitic stainless steels used for most medical device parts contain from 16 to 20% chromium and from 6 to 14% nickel. The presence of chromium achieves the desired corrosion resistance by forming a tough adherent and invisible chromium oxide film on the alloy surface. If damaged mechanically or chemically, this film is self-healing. In some grades, additions of molybdenum of up to 7% are made to further enhance corrosion resistance.
Among current medical applications, surgical staplers are a virtual showcase of 300-series stainless-steel parts, including the frames, springs, anvils, cartridge slides, and jaws. The staples themselves are made from various grades of stainless-steel wire. Other applications of 300-series stainless include arterial-plaque removers, catheters, and diagnostic instruments. An alloy with higher nickel content, stainless grade 316, is sometimes specified for braces because if its high creep strength at elevated temperatures. Grades 304L and 316L are low-carbon versions of the respective alloys and are recommended when welding is anticipated.
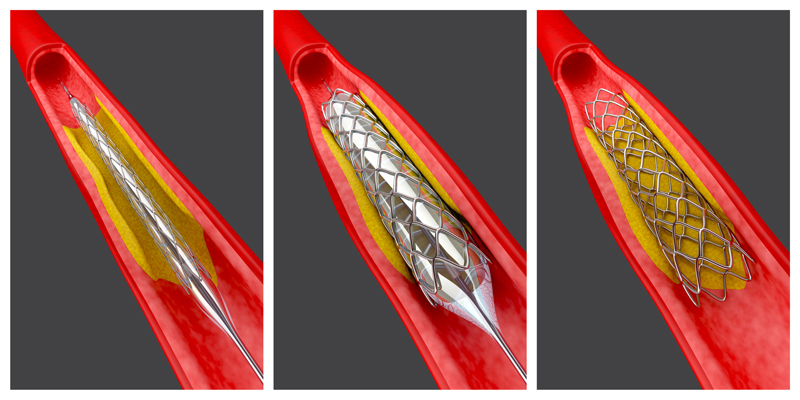
HARDENABLE ALLOYS
Four-hundred-series stainless steels, commonly used for surgical instruments, are less corrosion resistant that the 300 series but can be processed through heat treatment to higher strength and hardness levels. The two most common grades, 410, whereas 420, contain a minimum amount if chromium and no nickel. The general-purpose grade is 410, whereas 420 has more carbon content and is the more hardenable of the two.
Type 410 martensitic stainless steel is also used for surgical instruments. It is less corrosion resistant than any of the 300 series grades but can be processed through heat treatment to achieve higher strength and hardness levels. Type 410 contains only 11.5 to 13.5 percent chromium and no nickel.
When a part requires extra strength and stiffness – as in equipment housing, for example – the designer may opt for one of the precipitation-hardening stainless steels, such as 17-7 PH or 17-4 PH. These metallurgical hybrids are very similar in composition to stainless type 301, the only difference being small additions of copper, aluminum, phosphorus, or titanium. After a part has been formed into its final shape, it is given an age-hardening treatment in which these added elements precipitate a phase transformation. The result is the formation of intermetallic compounds that significantly increase the hardness and strength of the part, sometimes by as much as 40%.
TITANIUM
Pure titanium, the most inert of the commonly used metal materials and the most expensive, is used for ultra-high-reliability parts or those that remain inside a patient after surgery. These include pacemaker cans, replacement joints, and other metal implants. Titanium alloys are also used in the medical field, primarily in parts for which stainless steel cannot meet the strength, hardness, corrosion-resistance, or other specifications.
Offering the strength of steel at less than two-thirds its weight, titanium is a superior biomaterial. Its outstanding corrosion resistance is based on its ability to form a tightly adherent, protective oxide film upon exposure to air or other oxidizing media. This passive film withstands all types of corrosion and will reform after damage to the metal’s surface.
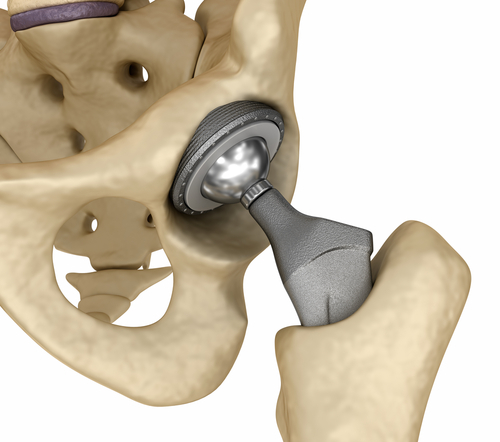
One of the most demanding applications in the medical field is also one of the most exotic in terms of fabrication and use of available alloys. The familiar hip-joint replacement is intended to be a lifetime prosthesis, and therefore requires materials of very high strength, superior wear resistance, and excellent corrosion resistance. Designs from various manufactures differ slightly, but one popular type consists of a titanium-alloy cup that fits into the hip socket, a cobalt-chromium head onto which the cup is mounted and a cobalt-chromium stem that fits into the femur.
For manufacturers of titanium hip stem joints, Ti-6AL-4V titanium alloys, including the low oxygen ELI grade, are usually preferred for implantable applications, in both bar and plate. Bar is the most common starting material when the part will be forged and is available in diameters up to seven inches.
Ti-6 AL-4V, the most widely used of the titanium alloys, has a minimum room-temperature tensile strength of 120,000 psi. It is fully heat-treatable in section sizes to one inch. Both hardness and strength can be increased by about 20% by heat treatment. After aging, typical yield strength of a one-inch bar is 150,000 psi, with a hardness of 360 Bhn.
Why are certain product forms preferred?
Stainless steels, hardenable alloys, and titanium alloys can be produced in various forms required by the medical industry, including foil, strip, sheet, wire, rod, bar, and plate. Because medical device parts tend to be very small and intricate, automatic stamping presses are normally used to form the shapes. Strip and wire are best suited to this type of processing and are the most common starting materials. These mill shapes come in a wide range of sizes. For example, strip varies from ultrathin foil of 0.001 in. up to a thickness of 0.125 in., whereas flat wire can be provided in thicknesses of 0.010 to 0.100 in. and widths of 0.150 to 0.750 in.
CONSIDERING FLAT WIRE AS AN ALTERNATIVE TO STRIP
In order to process strip through automatic stamping machines, precise widths are required to minimize scrap. Slitting to width is a function that can be fulfilled by strip rerollers or by strip service centers, with equal skill. For most stamped parts, edge condition of the strip is not a factor, but when it is, suppliers can remove the slit edge by deburring, rounding, or squaring it off.
When a smooth edge is required, designers have the option of using flat wire instead of strip. Because flat wire is rolled with dies on all four sides, a smooth, uniform edge is guaranteed for the entire length. This can save the cost of conditioning the edge and provide additional benefits as well.
One of these advantages is producing a “strip” product that is exceptionally thick for its width. For very thin gauges, regular strip is available in slit widths as narrow as 0.035 in. As the thickness increases, however, the slitter needs more space between the knives in order to maintain camber, flatness, and other shape parameters. When the thickness of the strip approaches 20% of the width, flat wire can usually provide better tolerances, especially in widths under 0.75 in.
Buyers have almost as many choices of alloys for wire as they do for strip, so availability is not a problem. Wire comes in 300- and 400-series stainless steels, titanium, precipitation-hardening alloys, and many others.
What are some characteristics to keep in mind?
MACHINING
Machining characteristics of the 6-4 alloy are similar to those of austenitic stainless steels, both rated at about 22% of AISI B-1112 steel. However, titanium reacts with carbide tooling and heat intensities the reaction; consequently, heavy flooding with cutting fluid is recommended. Fluids containing halogen should not be used because of the risk of causing stress corrosion if they are not thoroughly removed after machining operations.
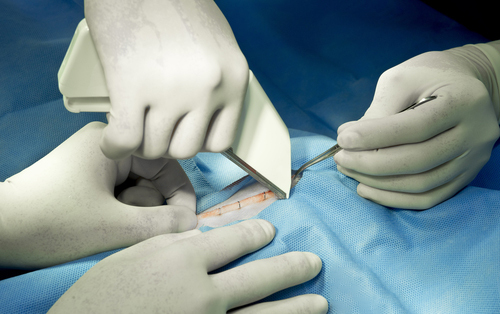
FORMABILITY
Although stampers prefer materials that are easy to cold form, formability is inversely related to the very things buyers may want when they specify these alloys in the first place – greater strength and hardness. Surgical staples, for instance, require maximum strength so they will not separate despite a very slim cross section. But they also must be formable enough so that surgeons can close them tight using noninvasive staple tools.
Achieving an effective trade-off between strength and formability is something that can be easily accomplished during the reroll stage. The appropriate level of formability is created while the strip is being rolled down to gauge, with annealing between the passes to remove the effects of work hardening. By alternating cold rolling with heat treating, rerollers provide a formable material that is ready for drawing, punching, and forming on conventional multislide and multidie stamping equipment.
Titanium and its alloys may have lower ductility than other common structural metals, but strip products can be readily formed at room temperature, although at a lower rate than stainless steel. With its low modulus of elasticity, about half that of steel, titanium springs back after cold forming. The higher the strength of the metal, the greater the springback.
Since ductility of titanium increases with temperature, forming operations may be done at elevated temperatures when room temperature efforts are not successful. Unalloyed titanium strip and sheet are normally cold formed. One exception are the alpha alloys which are sometimes heated up to 600°-1200°F to avoid springback. At temperatures above 1100°F, oxidation of titanium surfaces becomes a factor, so a descaling operation may be necessary.
Because the galling characteristics of titanium is greater than that of stainless steel, lubrication is extremely important in any operation in which titanium is in moving contact with metal dies or forming equipment.
CONTROLLING HARDNESS
Striking a balance between strength and formability is easily accomplished when rolling the alloy for thickness. By annealing between the passes to remove the effects of work hardening, cold rolling provides the desired temper, one that retains the material’s strength and provides the required formability.
To meet the often stringent specifications laid down for these alloys, and to control costs as much as possible, Ulbrich has metallurgists to assist you in alloy selection and to calculate a rolling/annealing sequence that will give you the best combination of properties.
SURFACE FINISH
The surface finish on stainless-steel and titanium-based strip products is also created at the reroll stage. Choices available to product designers include a bright, reflective finish; a matte surface that carries lubricant effectively; or other special surfaces required for effective welding, brazing, or bonding.
Surface finishes are imparted by the face of the work rolls in the rolling mill. Highly polished carbide rolls, for instance, create a mirror-bright reflective finish, whereas shot-blasted carbide rolls create an 18-20-µin. rms dull finish and shot-blasted steel rolls a 20-40 µin. rms matte finish. A 60- µin. rms is about as rough a surface as can be created by this process.
What is the best way to source your materials?
Most metal materials are readily available, because the grades in greatest demand for medical equipment parts are also widely used outside the medical field. This means that local and regional service centers usually stock these grades in the gauges and tempers required.
When the desired combination of temper and gauge cannot be found immediately, the services of a stainless-steel and high-alloy reroller like Ulbrich Stainless Steels may be enlisted. These specialists employ heavy-duty rolling mills to reduce strip thickness or wire diameters to exact dimensions. They also have the furnaces to anneal the metal between passes, removing the effects of work hardening and arriving at a temper that retains the material’s strength and provides the desired formability.
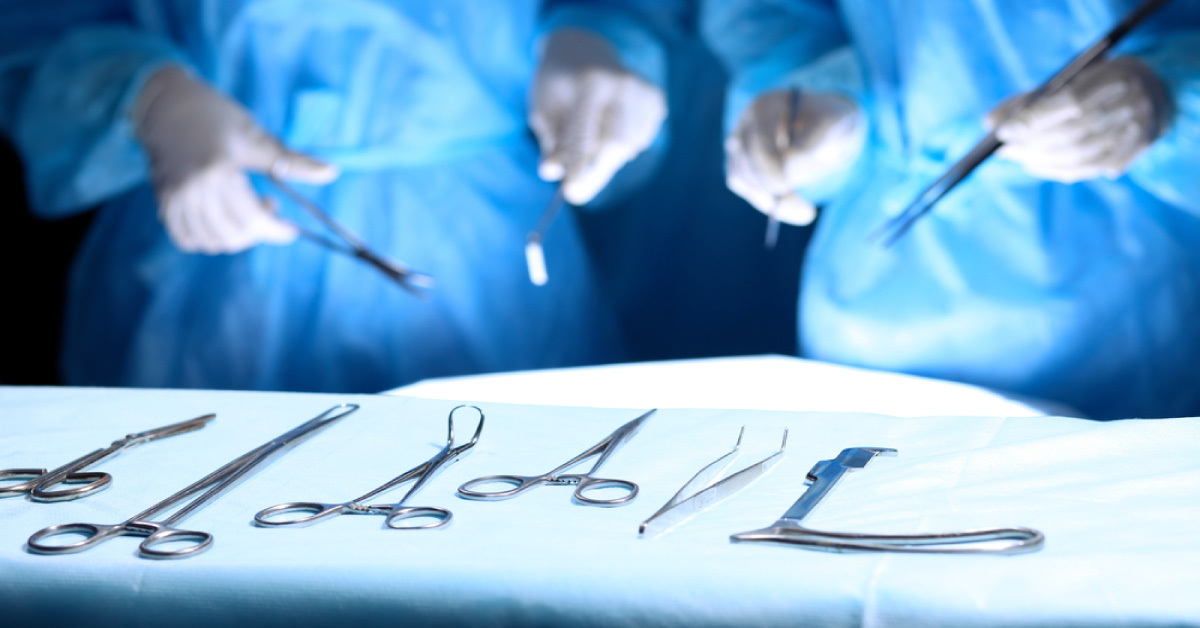
Which metal is right for your medical device?
Although stainless steel, titanium, and the nickel-based alloys are somewhat more complex from a user’s standpoint than more common materials, they also offer a significantly wider range of capabilities. These “metallurgical animals” can be customized through heating, cooling, and quenching to exhibit specific mechanical properties. If desired, they can be further altered during processing: for example, rolling out thinner gauges can harden the metals, whereupon follow-up annealing can bring their properties back to a precise temper for cost-effective forming.
Once designers become familiar with the complexities of the materials, they will find that these special metals provide a number of unequalled benefits in many medical products, including unparalleled corrosion resistance, superior mechanical properties, a wide choice of surface finishes, and great production versatility. Ulbrich is here as your development partner and will be glad to answer any questions you may have pertaining to your medical applications.