RF Cable Materials Q&A: How to Go Beyond Industry Specs for Next-Generation Requirements
The high-performance cable market is constantly evolving and almost all manufacturers face common challenges in taking the performance of their products to the next level.
To put it simply, the next generation of cables is demanding more from cable manufacturers than ever before. Lower signal loss and higher capacities are needed along longer lengths and at higher speeds. Cables in critical applications must get smaller and lighter, particularly in aerospace and satellite markets. And to make matters even more difficult, materials once commonly used are unable to withstand extreme environments (like space) or meet advancing performance requirements.
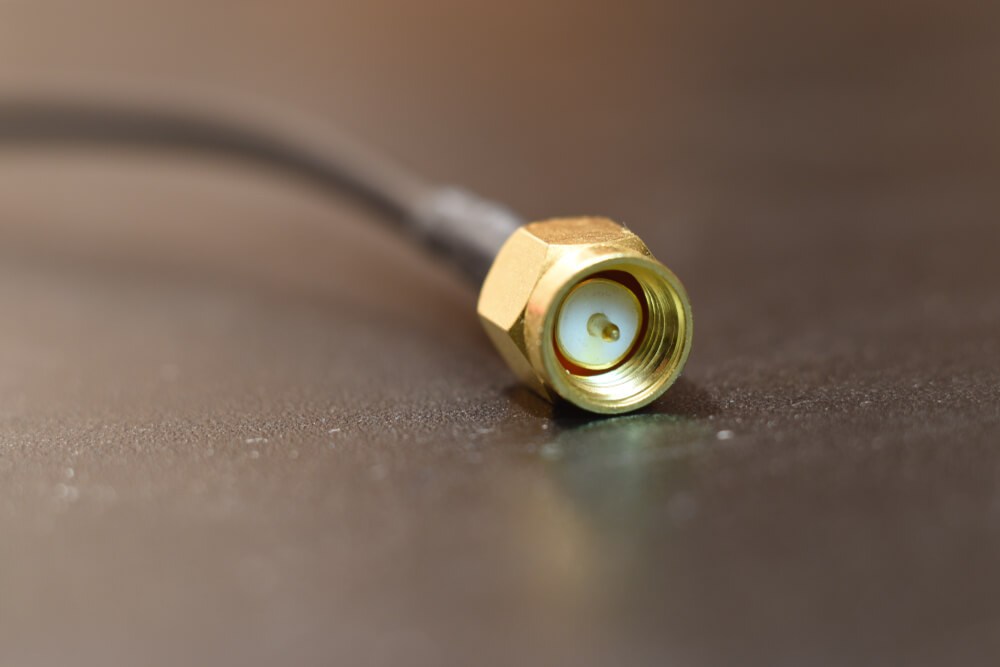
Given the unique capabilities of each manufacturer, one size has never fit all in cables but these design advancements are outpacing industry material specifications. As a result, industry specifications are no longer able to predict real-world success. As one customer told us, "we often don't know if the wire material works until a cable is made." It's only getting more difficult for purchasers to source materials up to the task.
To meet these challenges, Ulbrich is taking a two-pronged approach. One, we're adopting new alloys and creating forms able to rise to the demands of next-generation cables. Two, we've evolved our testing capabilities so that we can predict how our materials will impact final cable performance.
Fast Fourier Transformation (FFT) is utilized to detect any variations in dimension that pose a risk for data transmission in the final cable product. This helps us manage VSWR levels which is the ratio of the maximum voltage to the minimum voltage in a standing wave pattern along the length of a transmission line structure. As the demands for higher performance cables permeate information sciences and technologies, so does the demand for precision wire which is free of irregularities that can disrupt the signal transfer across long lengths of cable. By reducing VSWR, cable manufacturers can reduce reflections and lower the impedance between components, improving cable performance.
Customers frequently ask us about these advancements and how to optimize the performance of their cables. We’ve collected some recently asked questions and included answers from our cable material experts to help you meet next-generation requirements.
If you'd first like to learn more about how materials impact the performance of helical wrap-wire cabling, watch this webinar hosted by our RF cable experts.
How does switching helical wrap wire material from SPC to aluminum alloy affect coax attenuation? Assuming everything else is left unchanged.
It's unclear whether the material change itself affects attenuation in the assembled cables. That said, we can hold copper-clad aluminum products to similar FFT limits (from a dimensional standpoint) as traditional copper wrap wires. This indicates that (assuming everything else is left unchanged), the switch shouldn't introduce irregularities that will disrupt data transmission.
Under what specific process conditions or material properties is FFT applied?
FFT Measurements are only performed on the wire’s physical dimensions. Thickness and width FFTs are first checked while the rolling process is being set up to ensure the machine is in its optimal condition. FFTs are then rechecked at spooling to ensure dimensions remained consistent throughout the entire run.
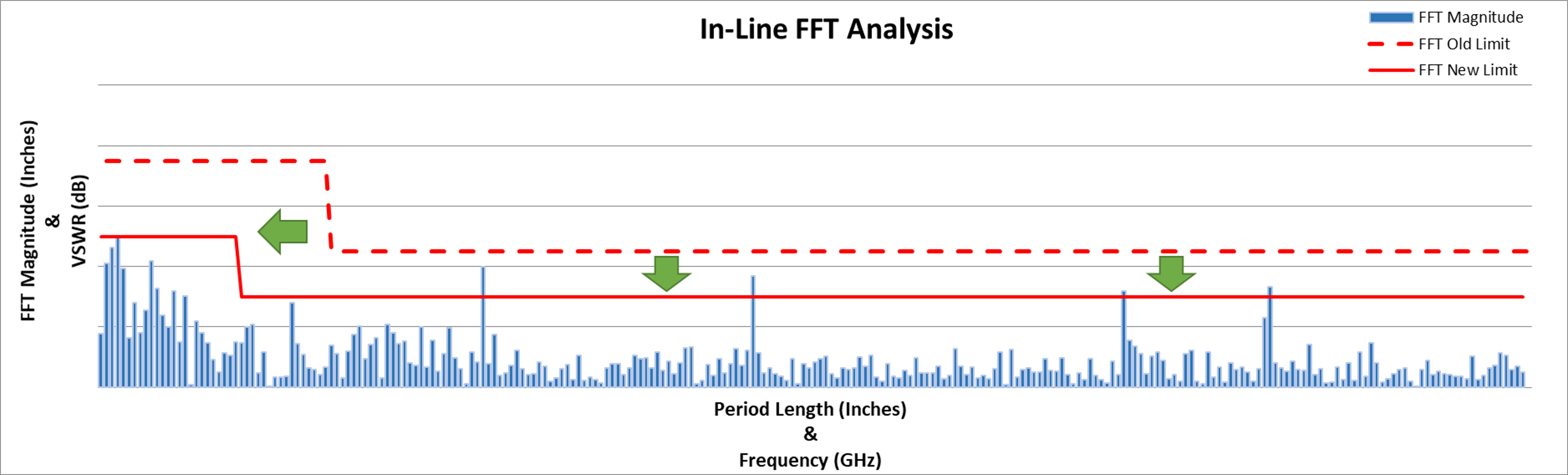
Do you offer stranded conductors and is FFT analysis available for them?
Ulbrich has recently begun a partnership with a company that can strand our wire. While FFTs have not yet been performed on stranded conductors, our gauging and FFT analysis program could possibly be adapted to look for repeating patterns in conductor lengths of interest.
What frequency range seems most common for FFT issues? For example, do FFT issues ever occur above 20 GHz or higher?
This will be different for different cable assemblies based upon cable diameter, wrap wire overlap, etc. but we are typically monitoring FFT spikes in the 1”-30” length along the wire. We're working towards measuring down to wire lengths as small as 0.1” to cover even the highest frequencies.
Do you perform FFT on round wire drawing?
Yes, we can perform FFT analysis on round wire drawing. We have typically provided this for center conductor applications. To establish the appropriate setting in the program, we would need to know some additional cable parameters.
What role do lubricants play in the process and final product?
Lubrication is used in rolling and drawing round wires using cold work. They aid in lowering friction, heat dissipation, tool wear, and surface finish. It's important to note that these lubricants must be free of silicon, which can compromise signal transfer in the finished RF cable.
Ulbrich uses engineered lubricants compatible with the specific metals being produced including silver-plated copper and bare coppers. We filter our lubricants to micron levels to remove metal fines.
In some cases, lubricants may be applied during the final winding. This is common when manufacturing braid wires. At Ulbrich, we use a “vanishing oil” called Isopar that can be used by itself or mixed with prescribed blends of mineral oil to apply evenly to the braid wire surface. This provides a smooth releasing agent during the dynamic motions required in braiding.
Can tighter specs than ATSM B298 be created?
Yes, we can create tighter specs than what is included in ASTM B298. We would need to see exactly what changes to ASTM B298 are being proposed but as long as we have the processing capability to meet the new spec, we are open to writing a customer-specific spec for your precise needs.
Can we get grade 40 and grade 30 copper-clad steel?
We commonly carry two grades of copper-clad steel, both with 40% IACS Alloy W40C06 would be for lower strength applications and we also carry W40C22 for higher strength applications. While we do not carry 30% IACS copper-clad steel, it is available to us through our supply chain.
Is it recommended to use lube for a helically-wrapped application? What lubes and mixtures are available?
Lubricants are typically only used on braid wires. However, the same application technique could be used on wrap wires. Ulbrich typically uses Isopar with anywhere from 0-10% mineral oils mixed in. If a customer has another lubricant they are interested in, we would be glad to discuss using that as well.
What sort of inspection methods are used to guarantee a proper wrap in the package spool to prevent wrinkles?
Wrinkles in the material can be managed with proper spooling settings. It's almost important that the spool itself is dimensionally solid and sound. To prevent wrinkles, our operators look for a level wind across the traverse without "build up" or "drop off" at the flange. We write specific spooling parameters into the process instructions for each part to ensure product consistency.
If you have further questions, don't hesitate to Contact Us. We're more than happy to share our expertise and learn more about your helical wrap wire needs.