Overcoming Saltwater Corrosion with Stainless Steel
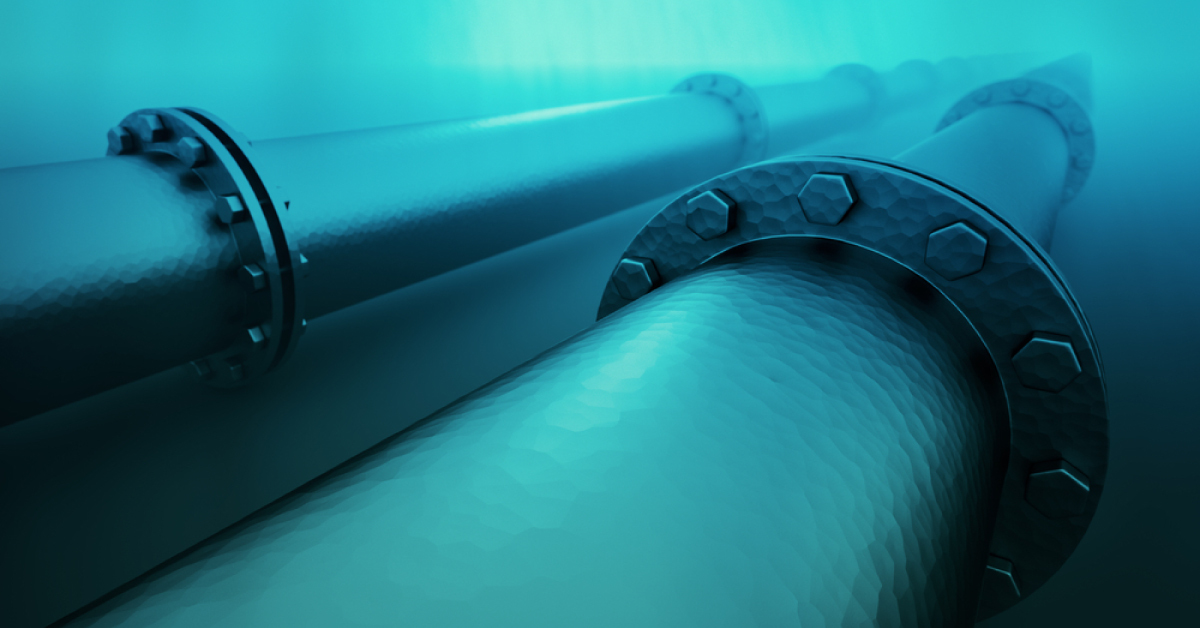
Metals are among the most versatile materials – they're incredibly flexible and strong. But they can be astonishingly fragile when exposed to certain conditions. Metals used in areas with significant saltwater exposure can be unforgiving to metals because corrosive exposure is inevitable in these applications.
Corrosion usually results from the reaction between metal atoms and their environments. One great example is rusting, which forms iron oxide due to the reaction between iron and oxygen molecules. Saline environments catalyze the process by creating an electrolyte solution around it. The metal doesn't have to be fully submerged underwater to experience corrosion. The air alone can harm metals like steel since there's always a small moisture percentage to facilitate corrosion.
However, stainless steel products are less likely to suffer extensive damage from corrosives because of the interaction between its alloying elements and the environment. The alloying elements that comprise stainless steel react with oxygen from water and air to form a very thin, stable film layer which acts as a barrier that protects the material from corrosives such as saltwater.
What Is Stainless Steel?
The term stainless steel applies to a range of steel varieties and doesn't refer to a single alloy. Instead, it applies to a wide variety of iron-based alloys comprising at least 10.5 percent Chromium (Cr). Besides chromium content, several other elements can be added, and the cranium percentage can be raised to enhance the metal's robustness and corrosion resistance.
There are many grades of stainless steel, each with their own unique chemistries. The American Iron and Steel Institute (AISI) recognizes more than 50 grades of stainless steel.
The most important element within stainless steel when it comes to corrosion resistance in general, is Chromium. The Chromium within stainless steel forms a thin oxide layer to the surface, referred to as the 'passive layer.' The corrosion resistance of stainless can be improved by adding more Chromium, leading to a more robust protective passive layer. This is why some grades of stainless steel are better at resisting corrosion from saltwater than others. However, this passive layer does not make stainless steel immune to corrosion. Stainless steel can, in fact, rust and corrode if continuously exposed to saltwater or other corrosive conditions over time.
Grade 304, otherwise referred to as the UNS 30400, is the most popular of Austenitic or the 300 series. It is a primary alloy comprising 18 percent chromium and 8 percent nickel, hence the tag' 18-8 alloy'. Another variant, Grade 316 or UNS 31600, comes with an additional 2 percent molybdenum. That's why this metal displays a higher resistance to corrosion by salty water.
What Makes Stainless Steel Stand Out from Other Alloys?
While aluminum is light, it has limited corrosion resistance in seawater and requires significant maintenance. The typical carbon steel is made up of at least 95 percent iron and up to 2 percent carbon. A higher carbon component means more robust steel. Similarly, stainless steel is majorly comprised of iron, but the chromium level must be at least 10.5 percent. The carbon content, on the other hand, is relatively lower at a maximum of 0.08 percent.
Stainless steel doesn't obtain its strength from the carbon component. Instead, it relies on its metallurgical structure for its robustness. To strengthen carbon steel, it has to be subjected to heat treatment. This, however, is not possible when it comes to the 300 series stainless steel. These are usually made stronger by work-hardening the structure.
Grade 304 and 316 contain nickel ranging between 8% to 14% added to the essential chromium component. Grade 316, particularly, comprises of an extra element called molybdenum. Its concentration varies between 2% and 3%. All these elements combined are the reason why stainless steel differs from carbon steel.
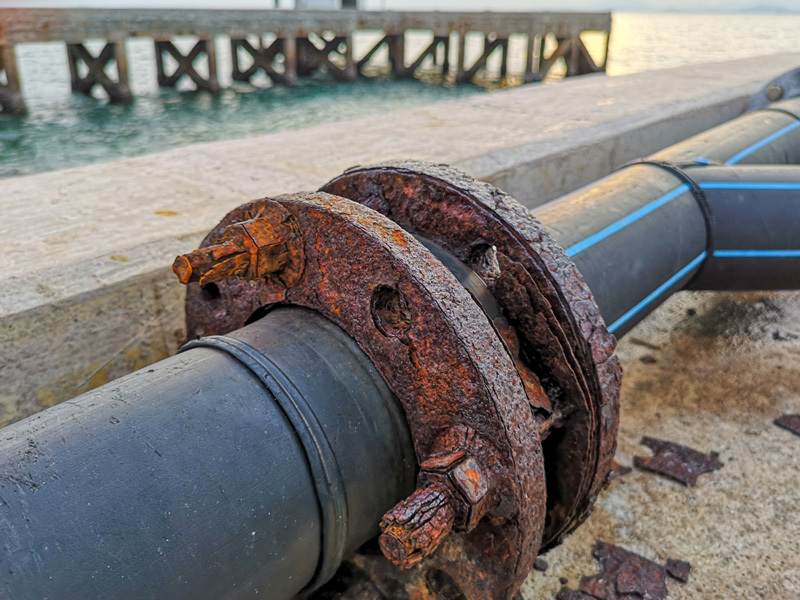
Carbon Steel Corrosion
The iron within the carbon steel can be easily oxidized to form an iron oxide layer on the surface, usually evident as red rust on the surfaces of marine appliances. The rust layer is typically several times broader than the original iron. It usually leads to flaking or spalling of the metal surface, hence reducing its thickness.
The United States and Canada are known to experience salt-laden mist originating from the oceans. The rainwater in these regions also has chloride concentrations, and people use deicing salts in the mountainous or northern regions within the U.S. All these scenarios lead to surroundings that are harsh to steel elements. As such, there's significant application corrosion experienced in these regions.
The best way to minimize the effects of such harsh conditions and limit your appliances' corrosion is by upgrading to grade 316.
How Stainless Steel Beats Corrosion
You are already familiar with the effect of Chromium in reducing corrosion in stainless steel offshore applications. The thin passive layer that covers the surface is usually tenacious. This means that even if you remove it by machining or scratching, it will still form again. The extra nickel in 304 helps by broadening the passivity range. Grade 316 stands out as the most robust since it contains at least 2% of molybdenum, a further addition that magnifies the passivity range. Although molybdenum is found in some other grades of stainless steel, it is the relatively high concentration present in 316 that helps to prevent the saltwater causing pitting or crevice corrosion.
Stainless steel should not rust if it has been well maintained. However, it is still likely to corrode when exposed to several conditions. The process will be different from the rusting experienced by carbon steel. The most common form of corrosion displayed by stainless steel is pitting, which occurs when the surrounding conditions overwhelm the passive film. The process is evident in small, dark-brown pits spread on the metal surface. However, it doesn't interfere with the steel's mechanical properties.
Stainless steel also experiences crevice corrosion resulting from deposits that create crevices on metal surfaces. It's almost similar to pitting but covers a larger surface area. While it may not affect the steel's mechanical processes, crevices are not attractive. You can minimize this type of seawater corrosion by creating designs without sharp corners and covering areas prone to cracking or pitting.
What causes stainless steel to corrode in marine environments?
No stainless steel is completely resistant to corrosion and the effectiveness varies with various factors including:
- Grade of stainless steel used
- Service temperature
- The concentration of salt in the seawater
- Water flow rates & oxygen levels of the water
- Amount of time in contact with saltwater
- Cleaning and maintenance frequency
Corrosion can occur in stages and increased chromium content in stainless steel can slow the process of corrosion down. The chromium on the surface of this steel creates a type of coating that protects the material from corrosion, when it is exposed to oxygen. This coating is what may appear as “rust” but is really working to slow corrosion on the material. Corrosion of a material can occur through the following devices:
- Biofilms
- Chemicals
- Galvanic Corrosion
- Stress Corrosion Cracking
- Intergranular Corrosion
These are all types of corrosion that can occur with stainless steel, whether it be a combination of smaller amounts of tensile stress, temperature and sea water (stress corrosion cracking) or just a passive layer on the stainless steel being attacked by a chemical reaction such as sulphuric acid.
There are of course more suitable special metal alloys for fully submerged applications, but austenitic stainless steels can be a great option for applications near saltwater or splash zones due to their high strength, lower cost, great formability and very good corrosion resistance.
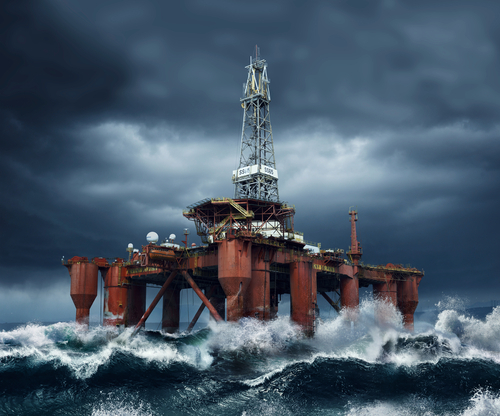
Specific Stainless Steels/Alloys Used in Saltwater Applications
There are many applications, especially within the oil and gas industry, in which metal is exposed to saltwater or other corrosive environments. When it comes to drilling for oil, there are well screens and screen wire used to filter the oil from the water or other contaminants, and those need to be made from a material that will not corrode easily. Common choices for this are alloys, such as:
These all work great, but stainless steel can be an ideal option for many high corrosion potential applications. Austenitic stainless steels, such as 316 or 316L stainless is a metal with very high corrosion resistance. It has an increased molybdenum and manganese content, which gives the metal corrosion protection and higher strength. This makes 316L stainless steel an option for many applications in corrosive environments. However, it is important to remember that corrosion resistance does not mean 'corrosion proof'; stainless steel is susceptible to localized attack mechanisms such as crevice and pitting corrosion. If your application experiences continuous seawater exposure, it is likely not a good idea to use stainless steel, and a different alloy should be selected. It is important not to let seawater stand in contact with the steel unnecessarily.
Applications can be exposed to corrosive water conditions in a variety of scenarios. As we already mentioned, there are offshore drilling sites exposed to the ocean and other extreme conditions, but there are also simple conditions such as rain or snow, or even saltwater content in the air that can make metal corrode rapidly. Cables and wires exposed to extreme conditions need cable wraps and shielding that can be provided by a metal that will not easily corrode. Sensors such as pressure sensors or monitors in marine environments are another application regularly exposed to saltwater. Choosing a reliable alloy that will reduce the corrosion rate is essential.
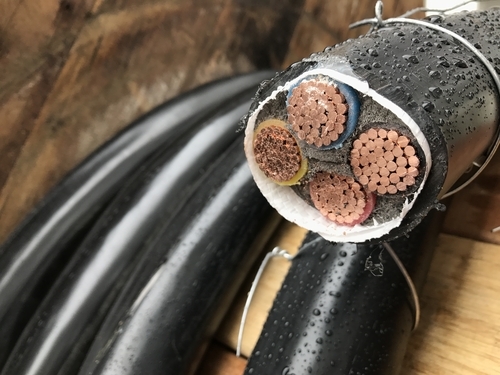
Key Takeaways
Rusting doesn't necessarily result from contact with saline water. Rainwater, airborne sea sprays, and dry salt particles in the wind may also lead to rusting and pitting in metals. But you can always avoid this by going for corrosion-resistant grades. As with all metals, it's essential to consider the application, environment of principle use, as well as the required mechanical and physical properties, and many other factors when selecting stainless steel. Stainless Steel is a great material to work with, and an excellent choice for many demanding applications, including those exposed to, but not continuously submerged within, saltwater conditions.
You need products made from unique rolling processes that create diverse metal thicknesses to be used in different environments. Contact us today if you need long-lasting, tailored steel solutions, and choose from a selection of over 165 alloys.