Nuclear Strip & Wire: Special Alloys, Common Applications, and Critical Process Controls
In 2020, U.S. nuclear power plants generated 790 kilowatt hours of electricity. This figure is significant because it marks the first year nuclear power generated more electricity than coal domestically.
While the United States is the world's largest producer of nuclear energy, this isn't an isolated phenomenon. As of 2022, countries like China and India are building over 100 new nuclear reactors worldwide. French President Emmanuel Macron pledged to construct up to 14 reactors and a fleet of smaller nuclear plants to help the country reduce greenhouse gas emissions.
As the demand for nuclear power grows, so will the demand for specialized materials able to withstand the radiation, high temperatures, and highly corrosive environments of nuclear fission reactors.
Additionally, cutting-edge advancements in alternates to fission technology are creating the need for more materials to meet the varying requirements of these emerging nuclear power applications.
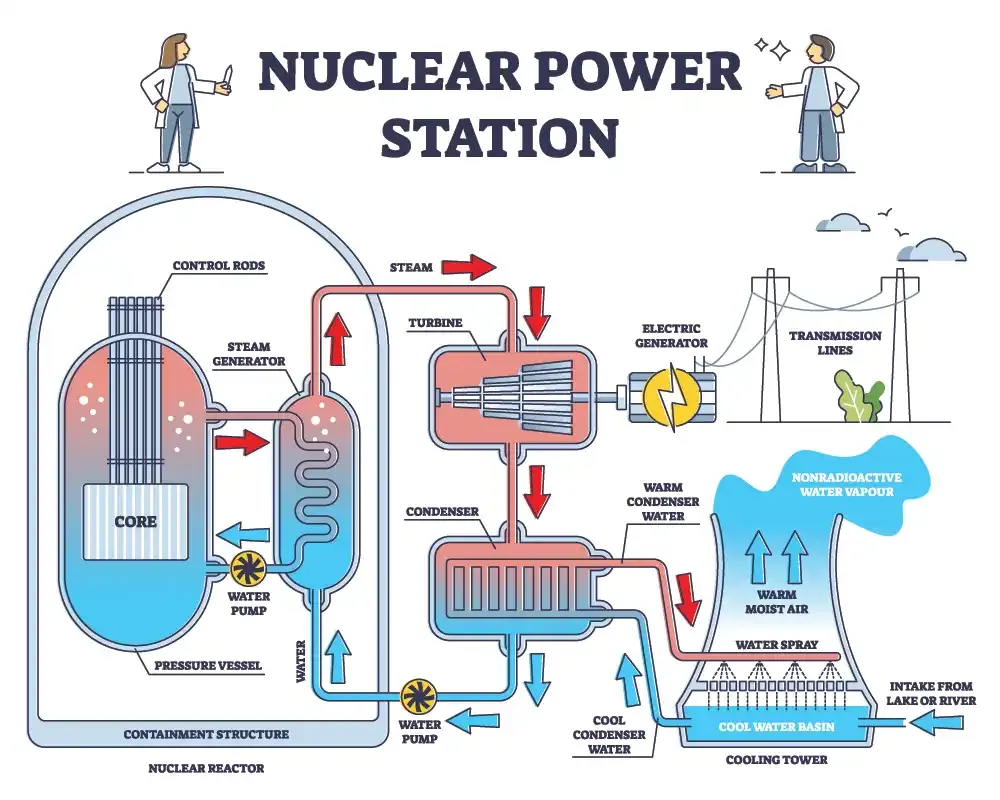
What is Nuclear Energy?
First, nuclear fuel is processed to release heat. That heat is applied to water, creating steam which spins a turbine. As the turbine spins, it turns a generator, producing a magnetic field and creating electricity.
At a nuclear power plant, heat is created by splitting atoms — often uranium — inside a nuclear reactor through a process known as nuclear fission.
Because the heat source isn't a burning fossil fuel, no greenhouse gases are emitted, making nuclear energy a cleaner and more sustainable option than many other power sources. And while tragic accidents have occurred, atomic power has among the fewest fatalities per unit of energy generated.
Nuclear energy, in terms of overall safety record, is better than other energy.
-Bill Gates
Some other nuclear power facts from the U.S. Department of Energy:
- Nuclear energy provided 52% of America's carbon-free electricity in 2020, making it the largest domestic source of clean energy.
- Nuclear power plants operated at full capacity more than 92% of the time in 2020, making it America's most reliable energy source. That's about 1.5 to 2 times more reliable than natural gas (57%) and coal (40%) plants and roughly 2.5 to 3.5 times more reliable than wind (35%) and solar (25%) plants.
- Nuclear power plants are designed to run 24 hours a day, seven days a week, because they require less maintenance and can operate for longer stretches before refueling (typically every 1.5 or 2 years).
- Nuclear helps power 28 U.S. states.
- There are currently 94 commercial reactors helping power homes and businesses in 28 U.S. states. Illinois has 11 reactors—the most of any state—and joins South Carolina and New Hampshire in receiving more than 50% of its power from nuclear.
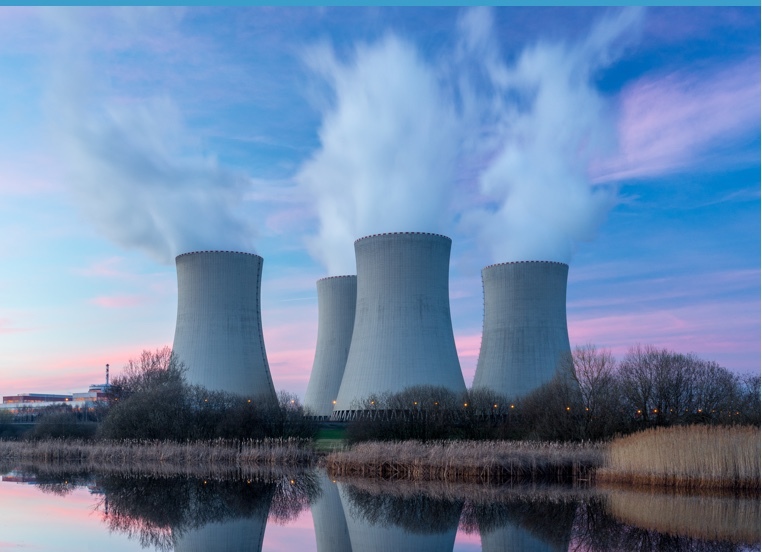
Nuclear Power's Past & Present
Following World War II, the only nations allowed by international law to enrich uranium (or plutonium) were the United States, Great Britain, France, the Soviet Union, and China.
In the United States, commercial nuclear power was an outgrowth of the Navy's Nuclear program. This program led to the development of Boiling Water Reactors (BWRs) and Pressurized Water Reactors (PWRs).
BWRs and PWRs are light water reactors that use ordinary water to cool and heat the nuclear fuel.
The difference lies in how the reactor generates steam:
- Inside a boiling water reactor, heat from the fission process causes the water to boil, generating steam.
- In a pressurized water reactor, water is heated to incredibly high temperatures but doesn't boil because it's under pressure. The heated water must flow through a heat exchanger to generate steam. These heat exchangers are aptly known as the steam generation system.
Today, PWRs are the most used nuclear power technology (almost 70% of reactors worldwide), with BWRs a distant second (around 15%).
Internationally, other technologies were developed and used, like heavy water reactors (favored by Great Britain) and gas-cooled graphite reactors.
Heavy water reactors use a form of water that contains a heavier hydrogen isotope, increasing its mass and imparting different nuclear properties. While heavy water is costly to isolate from ordinary water, the way it absorbs neutrons eliminates the need for enriched uranium, which offsets costs. Heavy-water reactors are primarily used in Canada and are also found in India, Argentina, Romania, Pakistan, and China.
Instead of water, commercial gas-cooled reactors use carbon dioxide as a coolant. They are currently only used in the United Kingdom (only 3% of global reactors) and expected to be phased out by the mid-2020s.
Since the 1960s, Ulbrich has supplied the nuclear power market with high-performance alloys that withstand these various fission power plants' radiation, high temperatures, and highly corrosive environments.
As the demands of these reactors have changed, we've continued to evolve our capabilities and processes to ensure the safe processing of materials, exceeding standards set by governmental regulatory agencies.
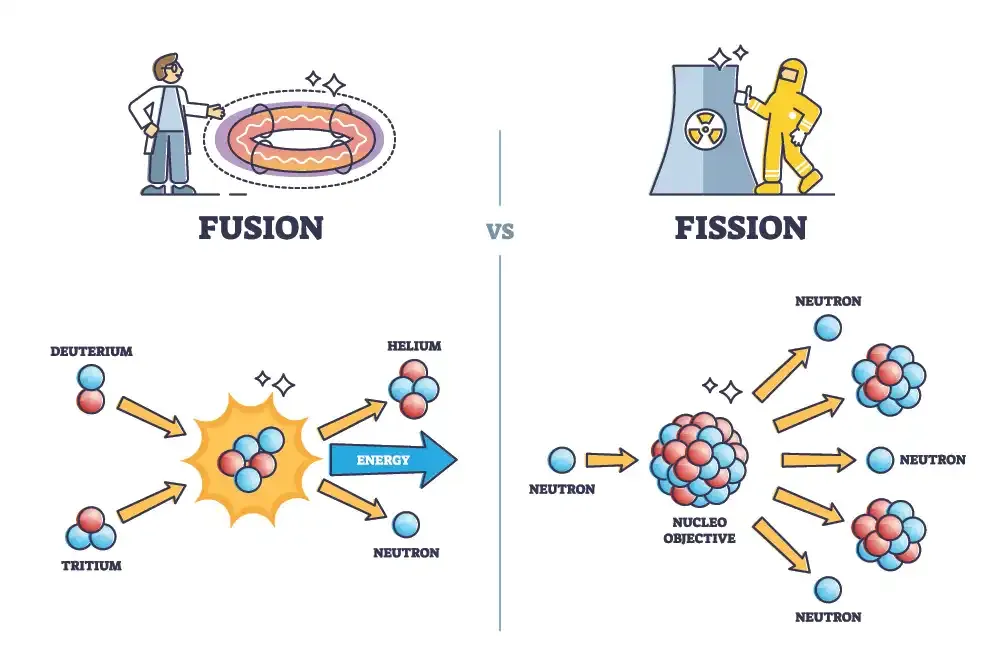
Nuclear Power's Future
As time passes, the nuclear power market will continue to evolve, focusing on addressing safety, waste disposal, development costs, and operational costs.
One exciting advancement is nuclear fusion, where energy is created not by splitting atoms apart but by fusing them, the same process our sun uses to generate power.
A nuclear fusion plant would produce nearly unlimited energy, in a safer manner than fission, while creating waste that is much more disposable.
On February 21, 2022, U.K. scientists broke the record for the most energy ever produced with a nuclear fusion reactor. In just five seconds, they created 59 megajoules, doubling previous records.
While a practical fusion is not yet feasible, successful experiments like this demonstrate the remarkable progress scientists are achieving.
Nuclear fusion applications demand different nuclear strip & wire products than traditional fission reactors; there are distinctly different alloys, applications, finish requirements, and mechanical properties. For example, Hastelloy C276 and other nickel alloys are more common in fusion applications where superconductivity is required.
Just as engineers must overcome challenging hurdles with innovative solutions, materials producers must advance their capabilities for new alloys, finish requirements, and mechanical properties to be part of this new frontier.
In the meantime, other exciting developments focus on improving the fission process, including using thorium as nuclear fuel instead of uranium or plutonium. Some scientists believe thorium to be critical to nuclear energy's future because it is much more abundant in nature, would produce less waste, and is harder to weaponize.

Quality & Safety Standards Needed for the Nuclear Power Market
When producing materials for nuclear energy applications, quality systems and safety are paramount.
These environments are too demanding, and the costs of material failure are too high to cut a single corner; most nuclear systems' failures involve the degradation of materials as they interact with these highly demanding radioactive environments.
Governmental regulations and oversight ensure the entire supply chain meets quality standards. In the United States, the Nuclear Regulatory Commission (NRC) is the main governing body. Examples in other countries include the Office for Nuclear Regulation (ONR) in the United Kingdom, Nuclear Regulation Authority (NRA) in Japan, and The European Commission (EUROPA) in the E.U.
These regulatory commissions partner with standards organizations, like the American Society of Mechanical Engineers (ASME), to develop consensus standards for systems, equipment, and materials used in the industry.
Mills and precision re-rollers that supply strip and wire for the nuclear industry must ensure that their teams are experts in this market and equipped to meet its exacting standards.
Additionally, approved supplier listings regularly need to be verified and validated. Ulbrich and its vendors maintain status under all current nuclear reactor design and fuel entities across the globe.
Frequent source inspections and audits by specific nuclear quality teams enforce oversight of suppliers and their vendors' process controls, quality controls, and quality systems.
Not only do Ulbrich's quality systems need to be kept up to date, but tight control of each strip and wire alloy is essential! PFOs (process flow outlines) are mandatory, and suppliers must train A.Q. personnel to be qualified and certified as production inspectors and auditors.
The bottom line is that quality, engineering, and Q.A. inspection are everything in this market.
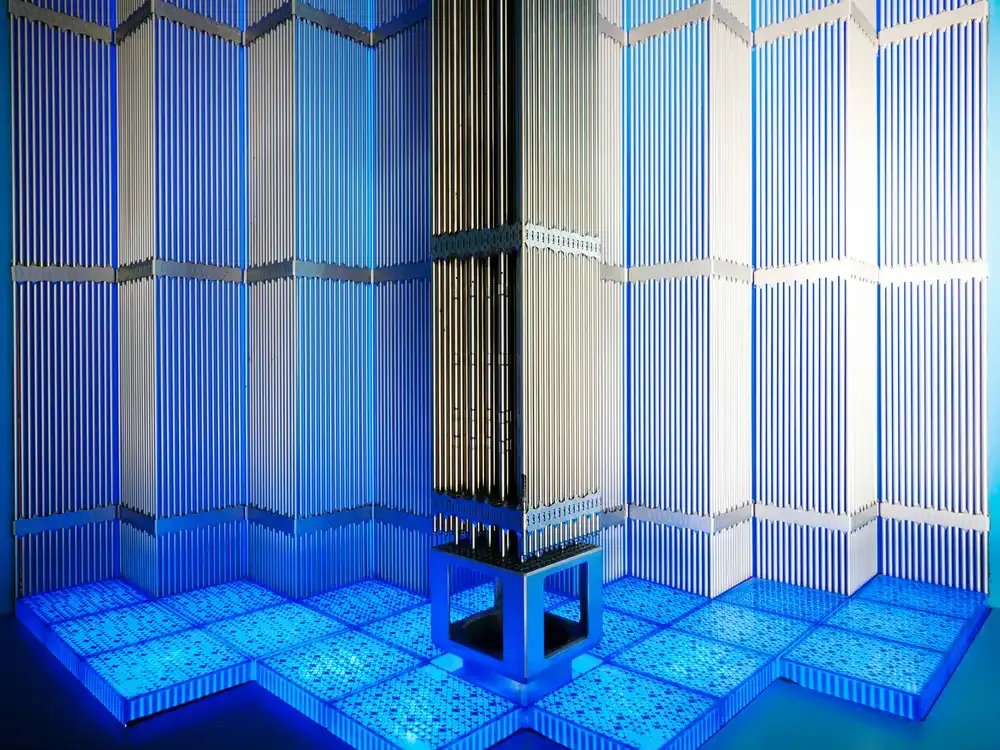
Nuclear Strip & Wire Applications
There are three main alloy systems for nuclear precision strip & wire. Several are commonly used close to fissile material in the fuel fabrication process and have properties suited for these highly-corrosive and high-temperature environments.
For strip & wire, these three commonly used nuclear energy alloys are I718N, X750N, and 316LN. Melt chemistries are closely controlled within these alloys, focusing on lower Cobalt (Co) percentages than typical chemistries. This tight control is essential for nuclear reactors to function properly, and a lack of attention could have catastrophic consequences.
Nickel Alloy 718N for Nuclear Energy Applications
I718N is Inconel® 718, a nickel-chromium alloy that is precipitation hardenable and has high creep-rupture strength at high temperatures to about 1300 °F (700 °C).
718N's resistance to high temperatures and other properties make it ideal for use in nuclear fuel bundle assemblies and structures in both strip & wire form.
For more information about the chemical properties of I718N, see our datasheet.
Nickel Alloy 750N for Nuclear Energy Applications
Inconel X750N, with the addition of titanium and aluminum, is a nickel-chromium precipitation-hardenable alloy having high creep-rupture strength at high temperatures to about 130.0°F (700°C). It also has excellent properties in cryogenic temperatures, superb corrosion and oxidation resistance, and high strength at temperatures up to 1300°F.
For more information about the chemical properties of X750N, see our datasheet.
Whether an application uses I718N or X750N depends on the design of the nuclear reactor. If you have questions about your use case, don't hesitate to contact us.
316LN Stainless Steel for Nuclear Energy Applications
316LN is a low-carbon, nitrogen-enhanced version of Type 316 austenitic stainless steel.
316 alloys are more resistant to general corrosion than conventional chromium-nickel austenitic stainless and offer higher creep, stress rupture, and tensile strength at elevated temperatures.
The nitrogen in 316LN provides solid solution hardening, raising its minimum specified yield strength compared to 316L stainless steel.
These properties make 316LN ideal for nuclear fuel bundles where strength and corrosion resistance are needed.
Other Alloys Used in Nuclear Energy:
- Niobium
- Niobium's very high melting point makes it nuclear reactor-grade.
- Hastelloy G30
- G30 is a higher-chromium version of G-3 with added cobalt and tungsten. Its superior corrosion resistance suits nuclear fuel reprocessing and nuclear waste processing components.
- Zirconium 702
- Commercially pure zirconium has a protective oxide layer for superior corrosion resistance.
Nuclear Strip & Wire Energy Applications
- Nuclear Springs and Washers
- Fuel Rod Components
- Filtration Systems
- Fuel Bundle Assemblies
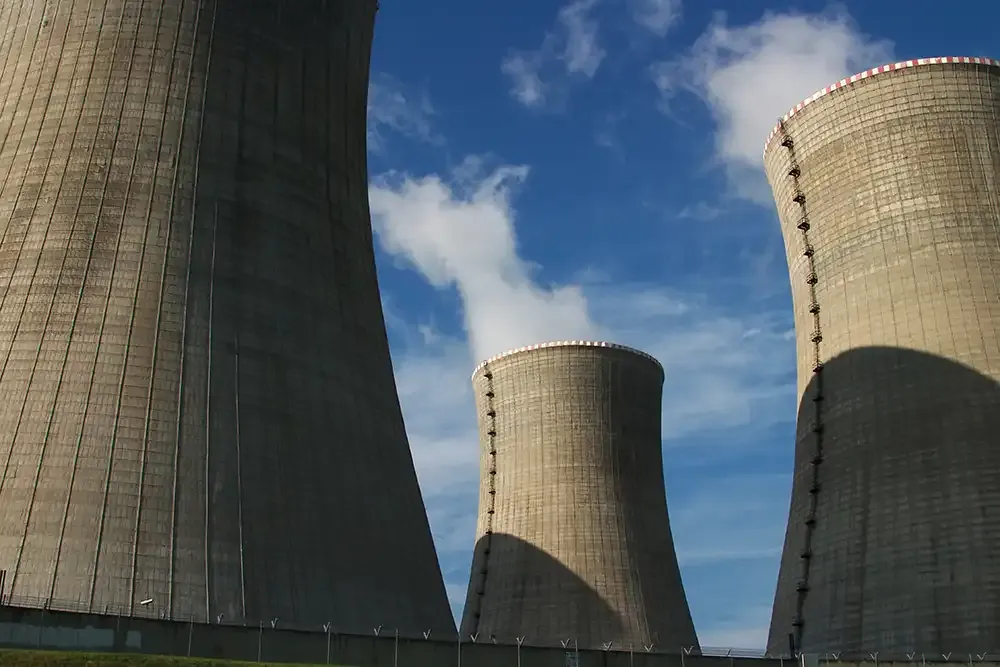
Final Considerations
It is important to note that the general public cannot buy nuclear-grade strip and wire, and sourcing options are minimal. Engineer-to-engineer communication is essential when selecting, designing, or specifying materials for use in nuclear applications.
Alloys such as I718N, I750N, and 316LN have unique restrictive chemistry limits and more advanced melting practices; this ensures each alloy can be used in nuclear reactors and creates a uniqueness not found in traditional stainless-steel grades.
Contact one of our nuclear metals specialists to share your requirements and learn more about our nuclear alloy capabilities.