Navigating the Types of Rolling Processes
Precisely manufactured metals are the building blocks for all sorts of daily applications. From construction to cars to food packaging, metal is simply everywhere. One of the best ways to produce precision materials like sheet metal, strip, wire, and ribbon is through the rolling process.
Basically, metal rolling involves feeding sheet metal through a rolling mill at either room temperature or extreme heat. The temperature and exact process depend on both the type of metal and the desired end product. Thanks to the different types of rolling processes and advanced rolling capabilities, precision metalworkers can produce different types of metals and alloys to fit the exact specifications of each project for each customer.
Understanding the Rolling Process
Metal rolling isn’t a “one size fits all” process. The variety of methods and machines helps ensure that every product fits each customer’s unique needs—and this is one of the many reasons why rolling works for so many applications.
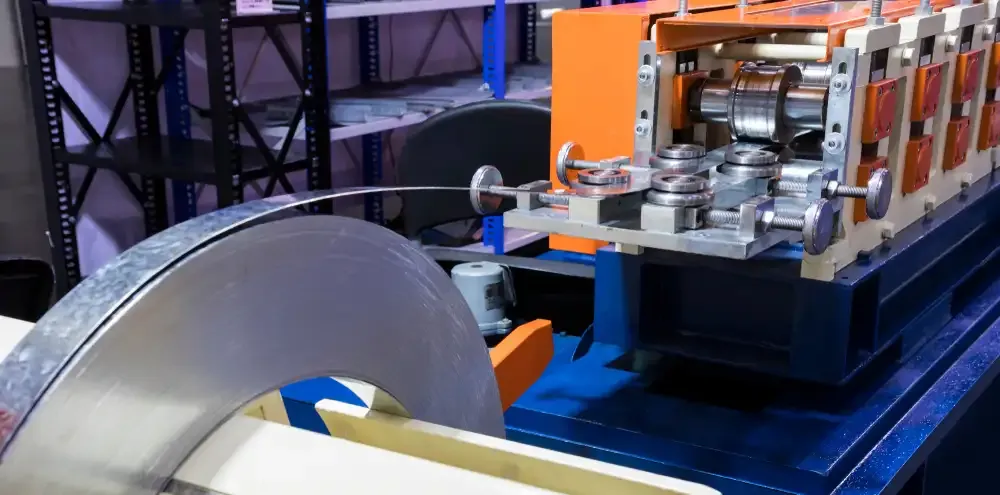
How Rolling Works
The metal rolling process begins with sheet metal or metal coil. The material is fed into a series of machines with large rollers known as a rolling mill, and the machines compress the metal to change its thickness or shape. Depending on the type of material used, its mechanical properties and properties such as ductility, plasticity, and hardness are also altered.
There are two main types of rolling processes:
- Cold rolling, which is performed at room temperature and thus below the metal’s recrystallization temperature.
- Hot rolling, where the metal is heated above its recrystallization temperature prior to being rolled.
Each type has advantages and disadvantages. However, having the option between these two methods is important to produce a wide variety of metal parts and products.
Importance of the Rolling Process
There are many reasons why so many industries rely on rolled metal. First, because the rolling process is so fast and so precise, it’s efficient from both a productivity and a cost standpoint. A continuous rolling mill can run at a high rolling speed without stopping, and advanced CAD programs direct the machines to roll and cut precise sizes without waste or runoff. With rolled material in coil form, manufacturers' machines can peel metal off the reel and directly into their machines. This way, metalworkers can mass-produce their products, lowering the cost per unit for their customers.
Second is versatility. Rolling mills don’t just alter the material’s thickness—they also ensure any custom bending requirements and the accurate plastic deformation of each product. This is perfect for producing sheet metal, U-channel, C-channel, and other end products in various thicknesses and lengths, among other applications.
Applications of the Rolling Process
Thanks to the efficiency and versatility of the rolling process, the applications are almost endless.
For example, precision cold-rolled metal has myriad applications, from industries as diverse as medical, aerospace, automotive, and oil & gas to power generation and electronics.
In other words, rolled metal is all around you thanks to the variety of materials and machines used in the rolling process.
Materials and Machines Used in Rolling Processes
Despite the huge variety of applications, the rolling process can’t be applied to just any material. Hard or brittle metals like cast iron aren’t formable and cannot be rolled, and metals with poor ductility or malleability like zinc aren’t suitable for this particular metal forming process. To achieve the desired end product, it’s crucial to choose the right material for the rolling process.
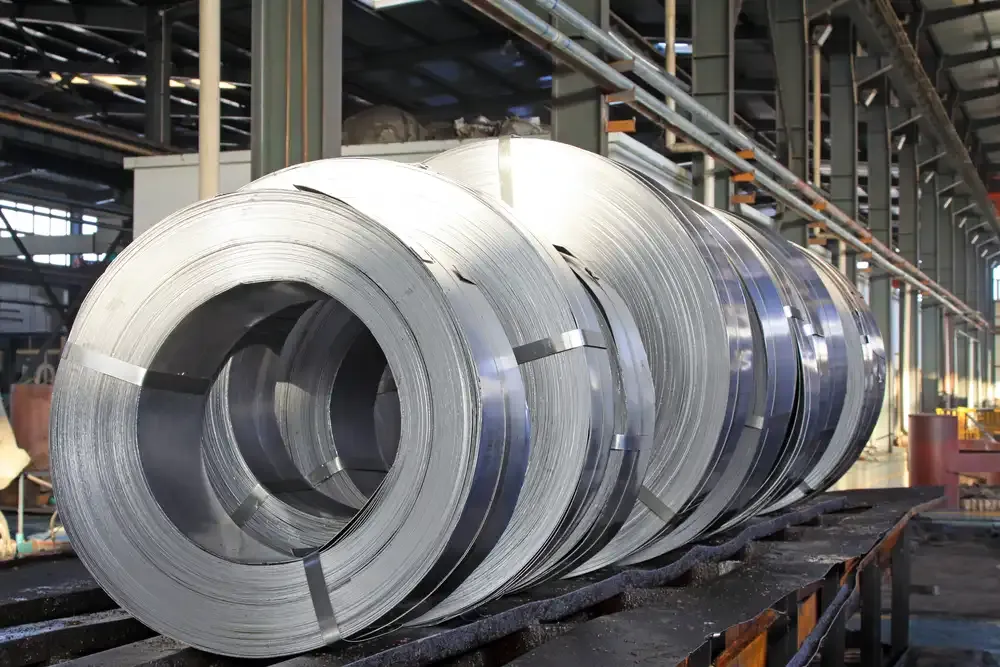
How to Choose Materials for the Rolling Process
Work rolls and sheet metal composed of different elements can be rolled, but it’s important to choose the right process for each material. Metals like titanium, aluminum, and some nickel alloys are well-suited to the cold rolling process. As long as the materials are high quality and free of impurities and imperfections, the end result will be a high-quality product made to the specifications and quality standards of each unique client.
Qualities of Materials Used in Rolling Processes
Material must be ductile and malleable to be rolled. Soft metals like aluminum and copper are ideal since they are easily bent and shaped. The tensile, yield, and elongation are desirable qualities of rolled metals since plastic deformation is often required to achieve the final desired shape. Additionally, most rolled materials have high tensile strength so they don’t fail under the pressure of the hot or cold rolling mill. Unsurprisingly, the machines used in the rolling process are dictated by the material itself.
Machines Used in the Rolling Process
As you might expect, rolling mills that work with heavy and hard metals are giant yet intricate machines. In both the cold and hot rolling processes, different types of mills are calibrated and programmed to accept large sheet metal or coil to output custom shapes, strips, and wires. Different types of the process yield different products, so the possibilities are just about endless.
Main Types of Rolling Processes
Different processes lead to different results—and the metal rolling process is no different. The type of material and the desired end product will dictate what types of rolling mills should and shouldn’t be used on any given metal or alloy.
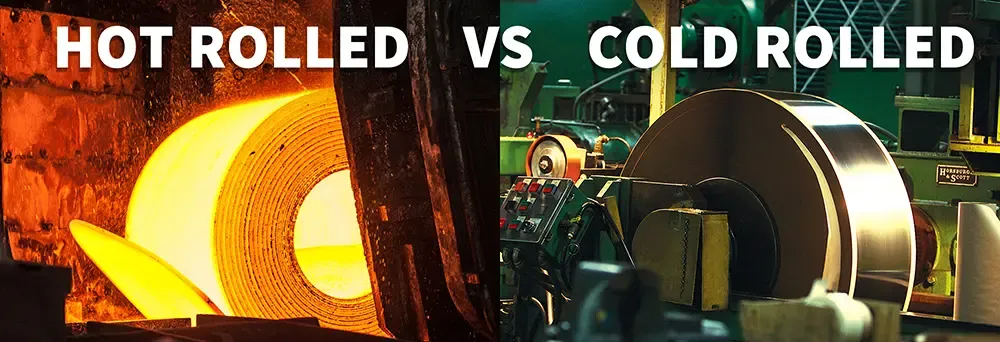
Hot Rolling and Cold Rolling
You’re already aware that the material itself will dictate whether a hot rolling or cold rolling process should be performed. Beyond that, there are several differences between these two processes. Here are a few notable distinctions:
- Cold rolling hardens the metal. It increases the material’s tensile strength and provides an ideal surface finish. However, it may also cause the material to become brittle and lose its ductility.
- Hot rolling allows for greater formability and plastic deformation since the metal is heated up to a temperature that makes it malleable. Thanks to the high heat, the material is free of internal stressors that might cause breakage.
In addition to hot versus cold rolling, there are different types of mills that can accept different metal compounds and sizes.
Common Types of Rolling Mills
Although feeding metal through rolling machines might sound simple, it’s an extremely complex process. So complex, in fact, that there are several different types of rolling machines, each with its own capabilities. Here are the main types:
- Two High Rolling Mills—Two work rolls are processed at the same time: one clockwise and one counterclockwise.
- Three High Rolling Mills—Three work rolls are simultaneously processed. Two rotate in the same direction, and the third rotates in the opposite direction.
- Four High Rolling Mills—This huge machine positions four steel rolls to maximize the machine’s efficiency.
- Cluster Rolling Mills—These strong and giant mass-producers allow the manufacturer to use both large and small work rolls.
- Tandem Rolling Mills—Also called a continuous rolling mill, this machine can accept multiple steel rolls to produce large quantities of material.
These different mills all have their own specialties and excel in different types of rolling processes.
Types of Rolling Processes
The options for metal rolling don’t end with the type of machinery—there is also a variety of rolling processes. Here are some of the most common:
- Flat rolling is the most basic form of rolling. Here, the material is fed between two rollers that rotate in opposite directions.
- Shape rolling, a type of cold rolling, doesn’t involve changing the material’s thickness but can be used to cut different shapes.
- Thread rolling is basically cold rolling in which threaded dies are placed on the machine’s rollers to produce screws and bolts.
- Ring rolling increases metal ring diameter using high temperatures.
- Roll piercing is a bit of a different process. Here, cylindrical metal is fed into the machine, and the center can be drilled out to produce seamless pipes and tubes.
- Roll forging changes the shape of heated metal bars or plates by reducing the heated metal’s cross-sectional area.
- Skew rolling forms spherical metal balls like ball bearings
- Roll bending, in which sheet metal or plates is shaped into cylinders.
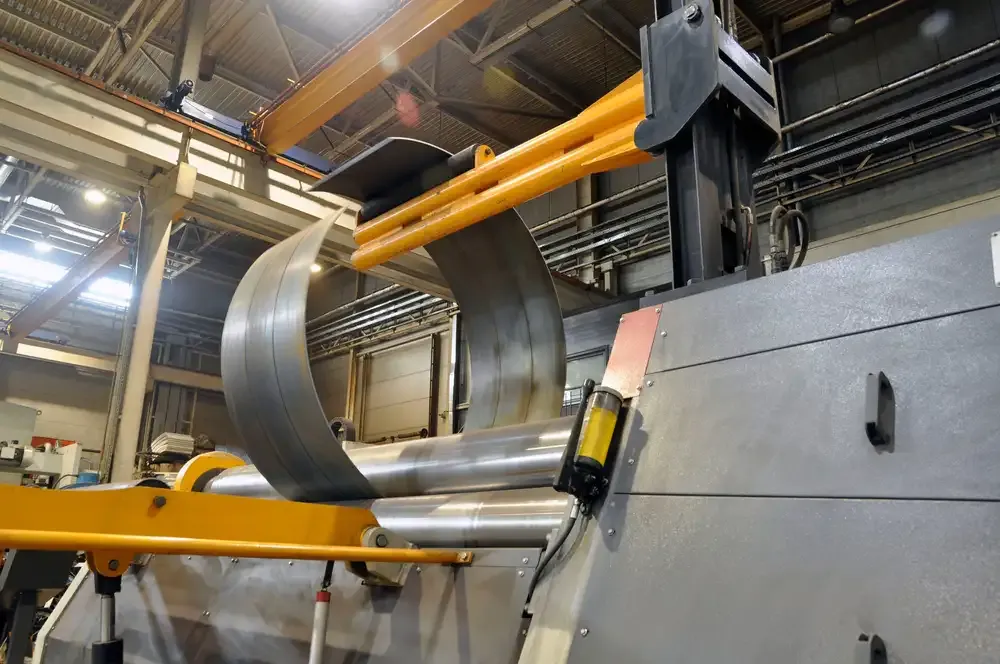
With all the products from the rolling process, it’s no wonder that rolled metal is everywhere in daily life.
Ins and Outs of the Rolling Processes
Rolling produces all sorts of great metal products. While there are many advantages to this process, it’s also important to consider the limitations and possible alternatives in case the required final product should be manufactured using a different method.
Advantages of the Rolling Process
Speed, efficiency, and low cost are three of the main advantages of the rolling process. The metal parts are produced quickly without wasteful stoppage time or runoff, and these efficiencies help lower the manufacturer’s and clients’ overall cost. And since each mill and roll forming machine can be programmed to produce any precise size or shape product, it’s a very versatile process that provides accurate metal parts.
Additionally, the rolling process yields end products that are stronger than the metal that was originally fed through the machines. What’s more, rolling mills can turn out more aesthetic products than other machinery, thanks to their ability to add a surface finish. The finish might be milled, annealed, matte, shiny, or colored—whatever the end user needs.
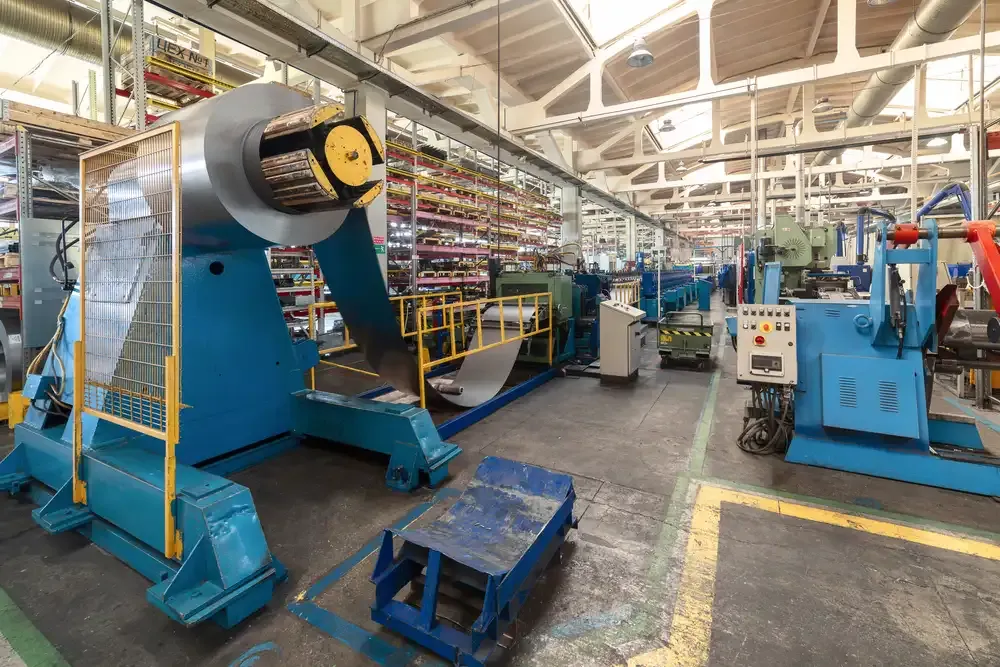
Limitations of Rolling Processes
Despite its many advantages, the rolling process has a few limitations. For example, some rolling methods yield an unrefined surface finish that requires additional finishing. The cross wedge rolling, in particular, sometimes requires visual inspection to ensure quality.
Another concern involves impurities or imperfections. Some material contains dirt or rust, which may lead to a weaker final product. Any cracks or center buckling in the sheet metal that goes into the machine will be exacerbated during the rolling process, potentially leading to wasted time and materials. And if the mills are rolling at high speeds, the metalworker needs to add a lubricant to keep things running smoothly. The lubricant can affect the surface finish, so if a particular finish is required, a product might have to be produced using an alternative to the rolling process.
Alternatives to the Rolling Process
In cases where the rolling process isn’t the best choice, here are a few alternatives that metalworkers can use:
- Metal drawing—Usually a cold process, material is pulled through a mold or die to create thin, lightweight products.
- Extruding—Metal is pushed through a die, which changes the material’s shape.
- Forging—The material is put under severe pressure, and the machine compresses it to create new shapes.
Between rolling, drawing, extruding, and forging, metalworkers have the capability to provide their customers with custom products of the highest quality.
Contact Ulbrich for Your Precision Metal Needs
Obtaining precise, consistent, high-end metal products is a difficult but necessary challenge for many industries. Fortunately, Ulbrich’s expertise and cutting-edge technology allow us to produce metal parts like strip metal and foil products to your exact—and even custom—specifications.
To speak with an Ulbrich specialist, receive a consultation, or request a quote, contact us today.