Metal Ductility: The key to deep drawing stainless and stainless alloys
Before we dive into metal ductility and how it may affect a manufacturing operation, let’s backtrack and take a look at the history of metal forming. The history of manufacturing operations and metal forming of a ferrous material’s ductility began with the blacksmith’s hammer, but a lot of what they learned to manipulate metal, their mistakes, and innovations have gotten us to where we are today. Centuries ago, Blacksmiths hammered away at metal and formed swords and other weaponry. Although the process was vastly different, the goal of metal forming was the same. Take this raw material and form it into a new shape that will be sold to a customer for their use. As we all know, this could be for a variety of markets, applications and volumes.
Through innovation, metal forming evolved into the more complex processes we have today. Modern metal manufacturing of stainless steel starts with metal that is melted and then hot rolled down into various thicknesses. From here, metal may be sent to a precision re-roller, such as Ulbrich Stainless Steels. That metal is then further “cold-rolled” down to thicknesses less than .001 inches with incredibly tight tolerances.
Manufacturers today, especially stampers and those performing deep draw operations on a material, like blacksmiths, exploit a metal’s ductility. The same characteristic that allowed metal forming centuries ago. Ductility is a measure of a metal’s ability to withstand tensile stress. Tensile stress is stress that pulls an object in two different directions, which tends to elongate the material until breaking point. A good example of this would be an extreme game of tug of war where both parties are evenly matched, and the rope’s tensile strength would be the point at which it stops elongating and actually begins to break or rip apart.
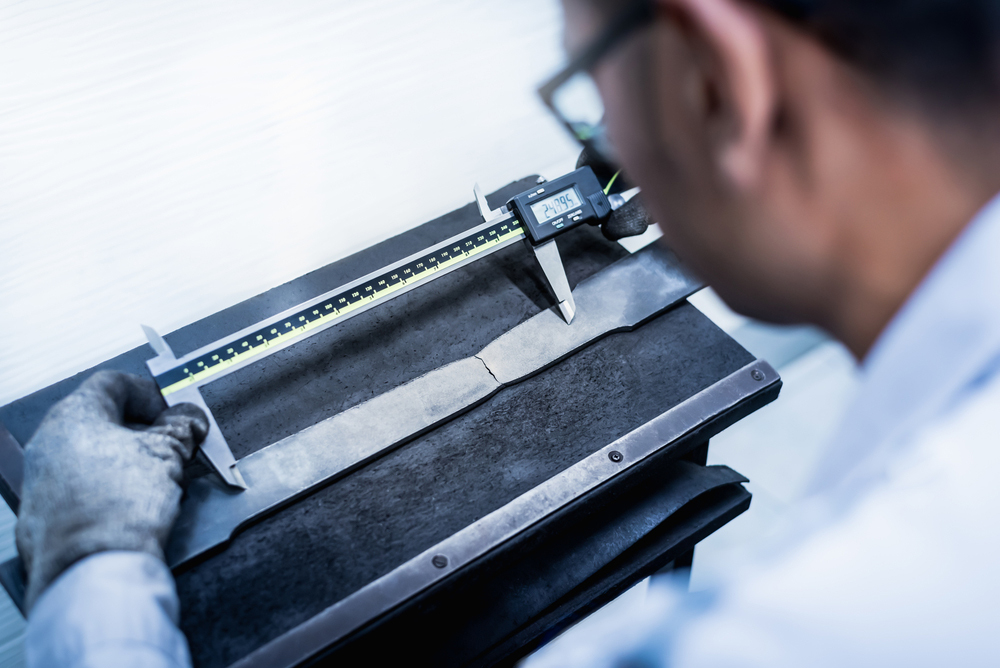
The beauty of metal, unlike the rope, is that metal maintains the shape it takes when plastically deformed. Metals with higher ductility can be stretched into longer, thinner forms without breaking. Matter, as you know, cannot be created or destroyed, so as the metal becomes thinner it must also become longer. Ductility comes into play with the amount of reduction in thickness that can be done without breaking the material. This reduction needs to be done while maintain the appropriate ductility for the stamping, bending or drawing operations coming at the next tier of manufacturing. With stainless steel, the thickness will be reduced until a certain point and then annealed to reset the mechanical properties and allow the material to be further reduced in thickness (and increased in length). As the material deforms and changes shape, it also becomes stronger (in most cases). This is known as work-hardening and the work-hardening rate of a material is the other factor that affects when the reduction in thickness must stop.
Different materials and metals all have different ductility and work hardening rates. Looking even within the grades of stainless steel, the differences are vast. For those not familiar with stainless steel, there are three main groups: Austenitic Stainless Steels, Ferritic Stainless Steels and Martensitic Stainless Steels. PH Grades and Duplex Steel also exist but we won’t get too deep in the weeds yet. There are many grades within each stainless steel category and different grades have different characteristics, such as increased corrosion resistance or greater ductility. Let’s compare the effect of two grades with different ductility, starting with 301 stainless steel and 305 stainless steel.
The understanding of alloying element effects drives the development of alloys. When we take examples like type 301 and type 305 stainless steels we can appreciate the practical implications of ductility. 305 will exhibit slightly greater elongation versus 301 in the annealed condition. Furthermore, 305 will receive less total increase in temper given the same deformation versus 301. This means if we deform 305 and 301 the same amount, 305 will have a lower yield strength but higher elongation. It will start with and end with more ductility given the same deformation. Now if you’re thinking this is relevant to your application, let’s take a closer look at how it will affect the forming of a part.
Ductility after work hardening is an important consideration.
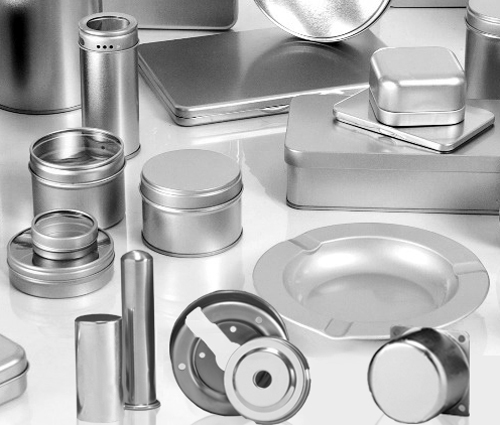
More specifically, ductility in the final configuration influences how the final part works. Let’s make up some numbers to the 301 vs. 305 scenario. If we bend equivalent dimensions with 301 and 305 we will end up with different mechanical properties. We began with different ductility and work hardened at different rates, so we will end up with different results. In a part dimension, let’s say we have a yield strength of 150,000 psi on our 305 and 180,000 psi on our 301. If this dimension received an applied load equivalent to 170,000 psi we have exceeded the yield strength on the 305 but not the 301. This means that the 305 will theoretically yield and therefore deform. We have a huge problem if we needed our part to not deform.
At Ulbrich, we too utilize the ductility of a metal when performing our rolling operations on the metals we work with, but ductility allows material to be deformed in many ways beyond rolling operations. When the material gets to the part manufacturers such as stampers or someone looking to perform a deep draw operation, ductility plays just as an important role. When it comes to a stamping operation, this is often a prior step to bending material into a final shape for the applicable part. With the final shape being permanent, the ductility and deformation of the material is very relevant because the bend has to occur without breaking the material and we also want this newly formed part to maintain its shape. In order for this to be as effective, the planning and process for this should start with alloy selection and degree of ductility within the alloy. From here, the rolling and work hardening of the alloy must be planned and routed in a way in which will get the tensile strength, yield strength and hardness to a desired range which is optimal for the stamping and bending operations done by the manufacturer. Ulbrich’s 15+ metallurgists on staff are essential in planning these routes and selecting the ideal alloy.
Material is rolled a certain way to preserve ductility for the deep draw operation. Movement of atoms within material is a big factor in the relationship between ductility and work hardening. Material undergoing deep draw must be drawn in a manner that facilitates a massive movement of atoms. Applying too much force will result in failure but not enough will also result in an unusable part. Similar to the stamping process described above, this must begin with the proper alloy selection for your material and the process in which that material is produced (rolled In Ulbrich’s case). All of these considerations need to be considered early in the development stages in order to avoid later issues such as broken parts or broken machines resulting in machine downtime and having to go back to the drawing board. Deep drawing requires ductility in all directions so Ulbrich must plan accordingly with dedicated processed routings that will yield the best possible result for the manufacturers receiving the material.
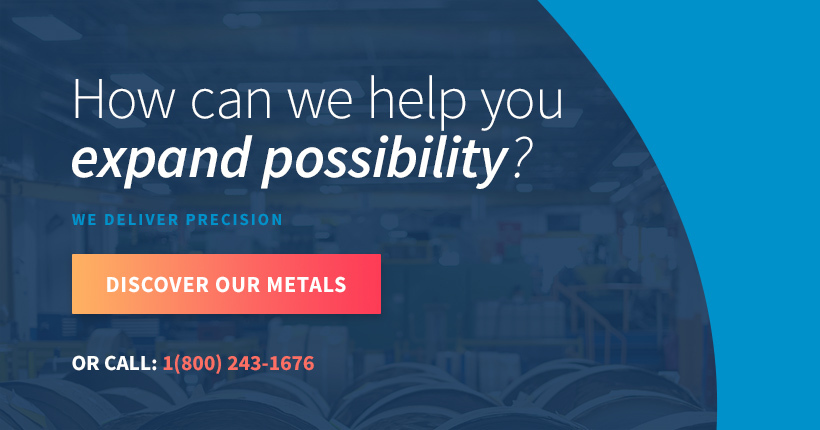