Alloys for Medical Manufacturing: Things to consider when evaluating wire alloys for your medical application
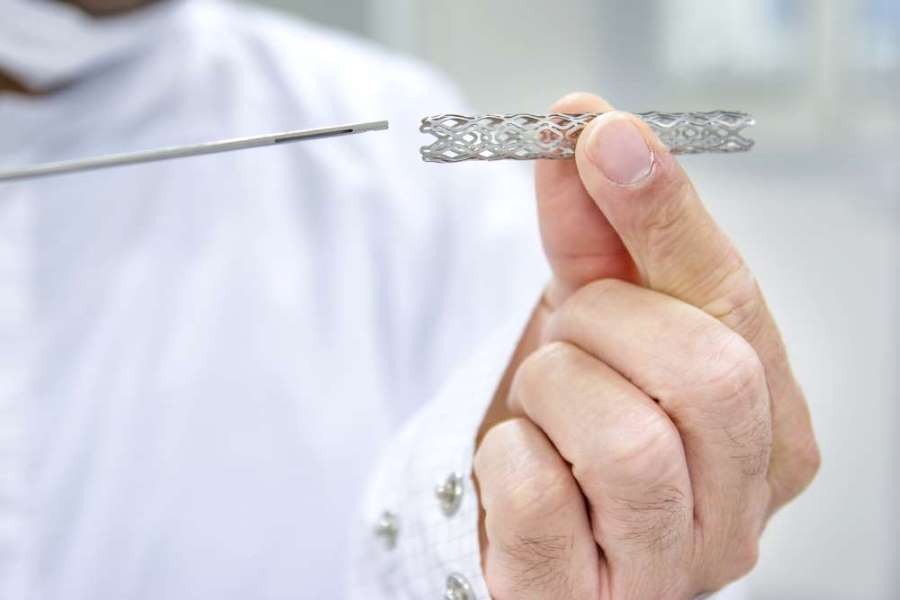
WHAT ARE THE PROPERTIES TO CONSIDER WHEN DECIDING ON A CERTAIN METAL ALLOY FOR A MEDICAL DEVICE?
The short answer: any decision on chemical, mechanical and physical properties of metal alloys is highly dependent on the what task the medical device will perform and the environment in which it will operate.
End-use applications dictate every single decision that goes into selecting an alloy, determining its shape and size and quantifying the amount of material needed. Other properties medical manufacturers and buyers to consider might be: atomic properties, electrical properties, environmental properties, magnetic properties, manufacturing properties such as castability or machinability, radiological properties, and even perhaps thermal properties the material.
When specifying an alloy for your medical application, correct and uniform chemical properties should be decided upon early in the metal selection process. Taking careful steps to select the right chemical makeup of an alloy allows precision re-rollers or other metal suppliers to source accurate, high quality raw material - that has been smelted or manufactured long before arriving at our loading bays. Engineers, Product Managers and seasoned Sales professionals at Ulbrich work together to communicate the best route to take in terms of material selection. At Ulbrich Specialty Wire Products in Westminster, South Carolina where most of our medical device customers procure precision round and flat wire, we have medical manufacturing and metallurgical experts who help our customers select and procure the right material with the right properties based on their specific application demands.
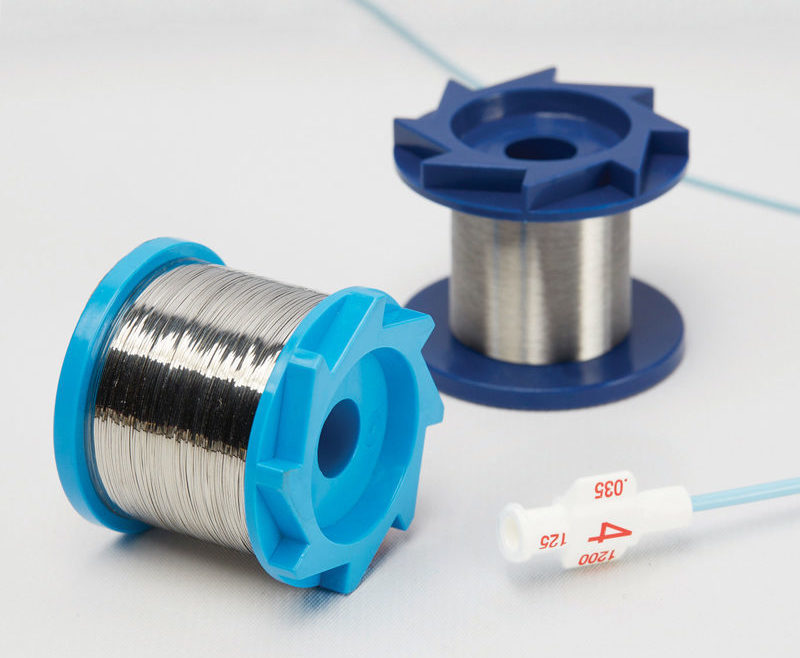
The most common mechanical properties are high strength and dimensional control for medical braid wire applications Dimensional control, surface smoothness and elongation have also become of high importance for Mandrel applications.
Mechanical properties and oxide layers related to the specialty metal Nitinol which is a shape-memory alloy, are known to be critical factors in the medical device industry these days.
Biocompatibility, or the capacity of the human body to adapt to contact with metal such as Titanium, is also a factor that medical manufacturers must often consider. For example, Titanium rods applied in oral surgeries bind to human flesh. The Titanium rods are permanently and effectively set in place making their biocompatibility extremely important to prevent rejection, corrosion, or infection. Titanium is highly biocompatible so it is often used in medical manufacturing such as dental implants, allowing patients to heal quickly and to use their jaw/teeth as if nothing happened.
Many medical manufacturers use a spring temper flat, round or custom shaped wire for their application. Different required characteristics that might be desirable based on manufacturing process or end use might warrant annealed, full-hard, half-hard, and quarter-hard wire which can be provided upon request from wire manufacturers. The harder the temper, the more rigid the structure will be. This gives a good torque response to the device, also known as “torquability”. For example, in the production of catheters, special maneuverability is key to success, making torquability of the material used in their production a very important requirement.
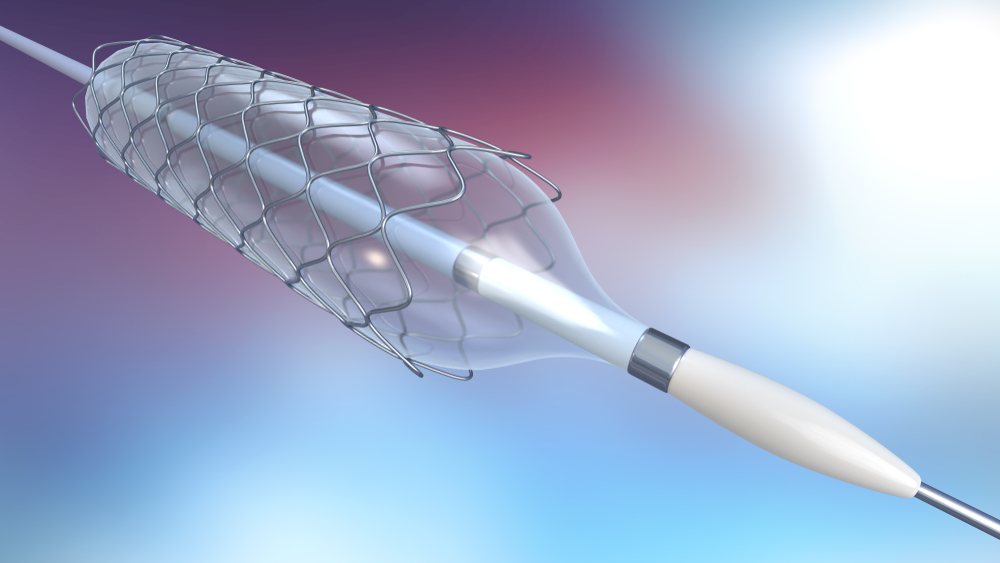
Catheters are medical devices that can be inserted in the body to treat diseases or perform surgical procedures. Mechanical properties play a huge role in the selection of metal for making catheters, which are extruded over specialty metals like Nitinol to create catheters. Medical device customers must also decide whether coiled-enforced or braid-enforced catheters are the correct for their application. In the production of catheters many customers are now using Nitinol for coiled catheters used in especially sensitive surgeries where precision is paramount, like neural or cardiovascular surgeries.
WHAT ARE SOME OF THE DIFFERENT METHODS FOR ENSURING MATERIAL QUALITY FOR MEDICAL WIRE AND WHAT DO THEY ACCOMPLISH?
Methods for ensuring quality stainless steels and special metals for medical wire should be a big focus, not only for the quality assurance team at your organization, but it should be an expectation of yours that it is the utmost priority of your medical rolling mill.
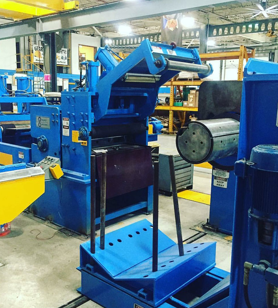
Continuous dimensional data collection (SPC data) should be collected as the metal runs through the mill because it improves consistency in performance for your manufacturing process and the device. Working closely with metal manufacturers who have metallurgists on staff who have knowledge of how metal is shaped and sized at the miniscule, mathematical level is extraordinarily advantageous for medical device manufacturers. This type of quality control ensures that defects are less likely and therefore, time and energy savings are benefitting your medical device or component business and streamlining your production while reducing scrap, waste and failure. Most of all, dimensional data collection assures that materials are within your specifications and meet all regulatory and manufacturing requirements.
Surface cleanliness is another major factor that has an impact on either improving or degrading material performance in demanding medical applications. Methods to ensure cleanliness can never be stringent enough, because people’s lives are literally on the line. Precision strip, flat wire and round wire must be as particulate-free as possible to ensure peak results, because anything else could be catastrophic.
Quality Control Coordinators, Machine Operators and Helpers at Ulbrich are continuously inspecting each work order with vigorous attention to detail. Team communication and collaboration are paramount to ensuring quality throughout the supply chain. When selecting a materials partner, you should work to understand if they have the same level of commitment to quality up and down the org chart as you would expect. Compliance with the latest ISO certifications are well and good, however, to meet the material needs of medical device customers, special precautions and utmost care should not only be standardized in the process, but engrained in the culture.
Personal Protective Equipment (PPE) is only step one to keeping material free and clear of contaminants. Custom barriers, guards, and other means of contaminant prevention should be installed on the machinery at every stage of material production to protect metal in progress (as well as Machine Operators) from being compromised. This will ensure that the material you receive is ready for, and has been manufactured to, the same level of cleanliness and attention to quality and performance that you set for yourself as a medical manufacturer.
A method on the front end of the manufacturing process starts with purchasing. Buying material from qualified sources and reputable vendors is essential. The chemistry makeup of the material must be carefully inspected while at the same time, inclusion rates should be as low as possible (non-existent in a perfect world). In choosing a supplier and an alloy, medical device customers must seek those sources who sell materials with consistent and undeviating mechanical properties which are paramount to processing medical wire. Manufacturing sources as well as production methods are equally vital in the supply chain to attaining success in the world of high-tech medical devices.
Lastly, tedious spooling methods to avoid tangles during production are also of high importance. When medical device customers go to use bulk, Steeger or Wardwell bobbins they do not want any breakages due to tangling wires. With round wire as thin as 0.00075” for nitinol and stainless alloys, tangling can cause massive strain on medical device production. Ulbrich cautiously wraps wire on spools with the next operation in mind and we ask for feedback on the performance of the spooling.
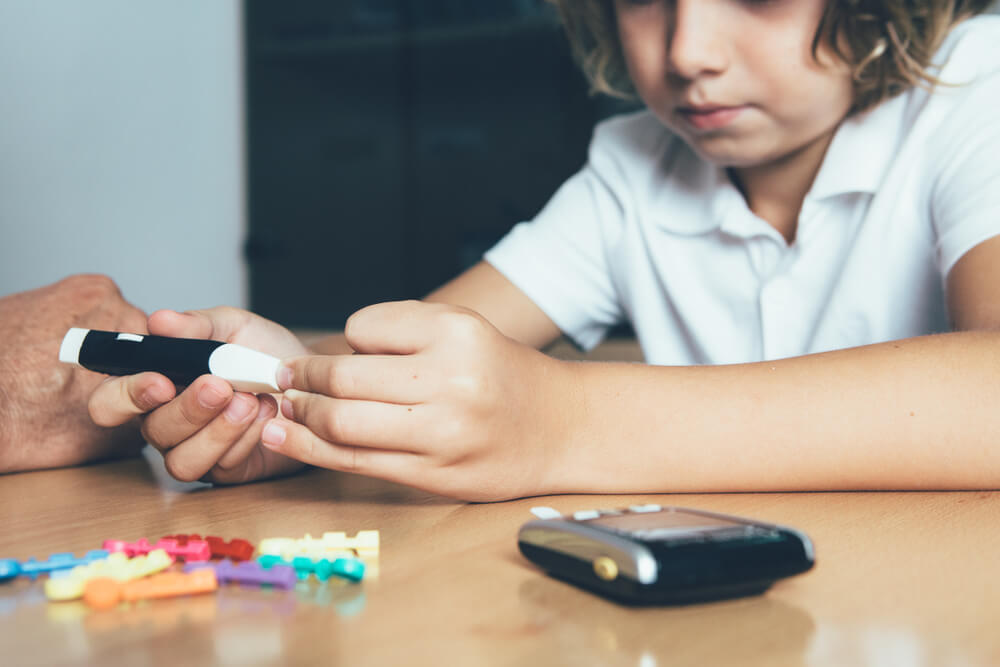
WHAT ENVIRONMENTAL OR CONTEXTUAL FACTORS ARE MEDICAL DEVICES SUBJECTED TO THAT AFFECT MATERIAL SELECTION?
Will the device be implanted in the body or how long will the device be in the body? Biocompatibility and response to blood is an essential factor here. MRI Compatibility may also be required depending on your application.
HOW IMPORTANT ARE THE CORROSION RESISTANT PROPERTIES OF STAINLESS STEEL OR SPECIAL METAL WIRE FOR MEDICAL MANUFACTURING?
Very important. For example, 304V stainless steel wire has been vacuum arc remelted so that it has a more uniform chemistry with minimal voids and contaminants. 304V is a flexible, robust material that can easily be soldered or welded. 304V Stainless Steel Wire is used in many medical applications because of its low cost compared to other materials that meet the minimum standards for corrosion resistance.
WHAT ARE SOME COMMON MATERIALS WE SEE MEDICAL MANUFACTURERS TURNING TO?
Bi-metals are becoming more widely used and popularized. Special alloys and various metals such as a developmental project-based alloy, MP35N, offer new, high performance capabilities for surgeons. Other bi-metals like Nitinol with a Platinum core (cladded) and a Nitinol with a Tantalum core have received greater exposure in the medical device marketplace as of late. Heavy metals like Platinum, Tantalum and Tungsten show up extremely well under a fluoroscope during cardiovascular surgery, for example, and allows surgeons to see where they are going within the human body. Though 304V stainless steel wire is still most often used in the majority of medical applications because the alloy meets the minimum standards for corrosion resistance while being a safe and productive material.
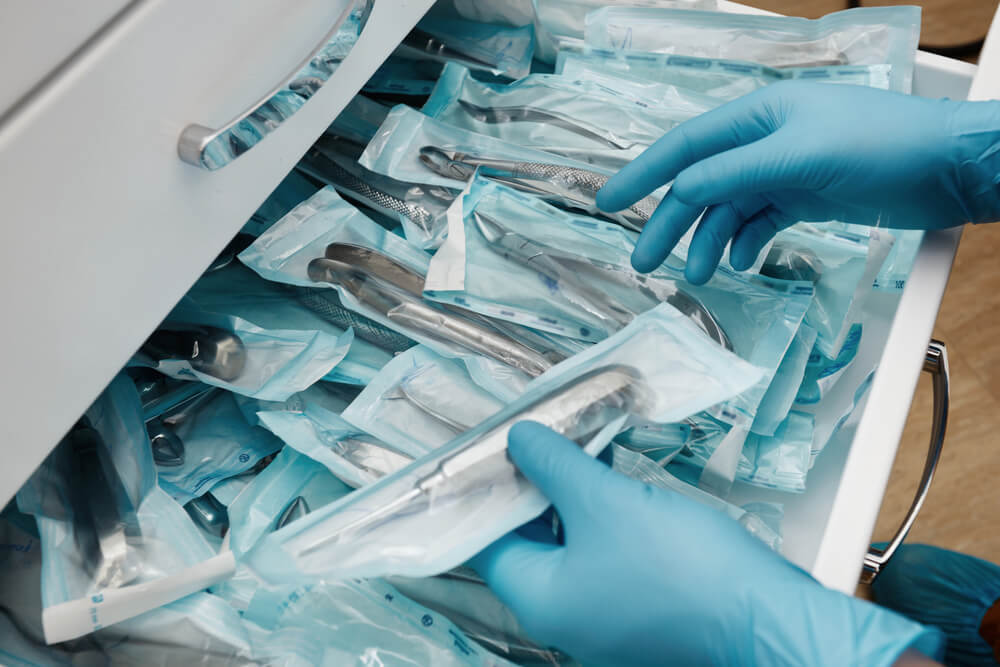
WHAT IS CRITICAL TO THE PRODUCTION & PERFORMANCE OF SURGICAL INSTRUMENTS?
When it comes to surgical instruments, stainless steel alloys—namely Austenitics, Martensitics, and Precipitation Hardening Grades—that are shaped and designed to perform very specific tasks are critical, and common. Alloys used to produce medical instruments should be manufactured to withstand the demands of daily use in healthcare environments, with rigorous attention to detail and quality. From cutting to pricking to stapling, the high-stakes demands of medical devices and surgical instruments require precision manufactured alloys with the exact specifications necessary to perform the job.
ULBRICH IS DRIVING MEDICAL INSTRUMENT INNOVATION THROUGH PRECISION ALLOYS.
With the help of precision special metals and alloys, doctors and workers in the medical field can restore and preserve the health of ailing people. At Ulbrich, we take great pride in the fact that our work plays a part—however big or small—in the health of millions. And that’s exactly why we’re always holding ourselves, our machines, and our processes to the highest of standards. Because with precision alloys, innovative surgical (increasingly robotic) instruments have the power to transform lives.
SURGICAL INSTRUMENTS MADE WITH PRECISION ALLOYS ARE SIMPLY BETTER
Different surgical instruments and incision tools require a diverse range of alloys and alloy characteristics. Choosing the best materials and having them produced to exacting chemical, mechanical, and physical specifications ensures that the resulting product, or component delivers more consistency, less waste, and lower failure rates. Ulbrich has a long history of providing alloys and bimetals to the medical industry due to our strategic sourcing methods, our huge inventory of alloys, and immense rolling and annealing capabilities. It gives us a competitive advantage that we are able to pass on to our customers. So, whether your medical device requires an alloy to be heat-treated to a higher hardness (like PH Grade alloys) or something non-magnetic and highly resistant to corrosion (like Austenitic alloys), we're able to make it happen.
SURGICAL INSTRUMENTS MADE WITH PRECISION ALLOYS INCLUDE:
- Scissors
- Sheers
- Surgical Draws
- Catheters
- Needles
- Lances
- Surgical Grills and Grinders
- Surgical Staplers/Anvils
- Stapler Springs, Staples
- Cardiovascular Clamps
- Tissue Grabbers
- Strip Square
- Surgical Robotic Instruments
- and more...
PRECISION ALLOYS USED IN SURGICAL INSTRUMENTS INCLUDE BUT ARE NOT LIMITED TO:
Stainless Steel Grades:
- 304 Stainless Steel
- 304V Stainless Steel
- 304LV Stainless Steel
- 304LVM Stainless Steel
- 316 Stainless Steel
- 316LVM Stainless Steel
Special Metals:
- Nitinol
- MP35N
- Copper
- Aluminum
- Tungsten
- Beryllium Copper
- Titanium
- Molybdenum
- Phosphor Bronze
- L605
- Many other “bi-metals” (combinations of cladded wire which may include Silver or Platinum).
Others Specialty Alloys include:
- 17-4PH® Stainless Steel UNS S17400
- 17-7PH® Stainless Steel UNS S17400
- 305 Stainless Steel UNS 30500
- 410 Stainless Steel UNS S41000
- 420 Stainless Steel UNS S42000
- 420 High Carbon Stainless Steel UNS S42000
- 420 LC Stainless Steel UNS S42000
- 440A Stainless Steel UNS S44002
AT ULBRICH, WE’RE ALWAYS LOOKING FOR WAYS TO INNOVATE AND IMPROVE UPON MEDICAL DEVICES.
In addition to our state-of-the-art capabilities in rolling, slitting, and annealing, Ulbrich is continuously testing, researching, and analyzing alloys and their chemical and mechanical properties to maximize performance potential. What does this mean for you? It means that when you partner with Ulbrich, you not only get the best of the best in personnel, process, and product—you also get a team that truly cares about making your medical device as consistently successful and effective as possible.
GLOBAL REPRESENTATION WITH SERVICE AND DISTRIBUTION CENTERS WORLDWIDE.
Ulbrich Stainless Steels & Special Metals, Inc. is a family owned company in its fourth generation of leadership. Established in 1924, Ulbrich has become a critical supplier of stainless steels and special metals to the Medical Device Industry. During this time, we have participated in the development and manufacturing of hundreds of innovative medical. With industry leading Dimensional Control, real time gauging and Statistical Process Control (SPC), a large variety of medical alloys, and the best customer service available, we strive to produce and distribute the highest quality materials. Ulbrich is comprised of a series of manufacturing divisions that supply specialty strip and precision wire, all with local management and all designed to provide custom metals products to satisfy the needs of the medical devices original equipment manufacturers.
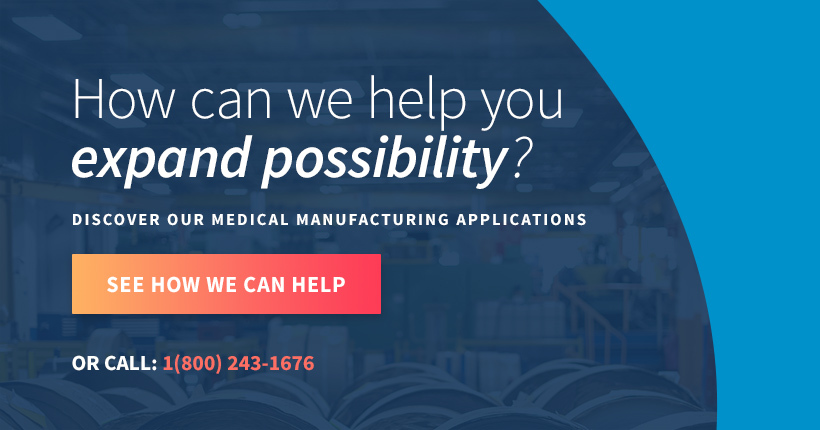