Lean Manufacturing for Process Improvements: Key Strategies and Benefits
One of Ulbrich’s core tenets is continuous improvement, which we embrace through our commitment to lifelong learning and openness to innovation —whoever it comes from and whenever it arrives.
Or as our founder Fred Ulbrich Sr. simply stated, “I aim to be the best in all that I do.”
It’s no surprise then that we’ve been early adopters and ongoing practitioners of lean manufacturing, which stresses continual process improvements.
Keep reading to learn how lean manufacturing can help you refine existing processes and open the door to new opportunities.
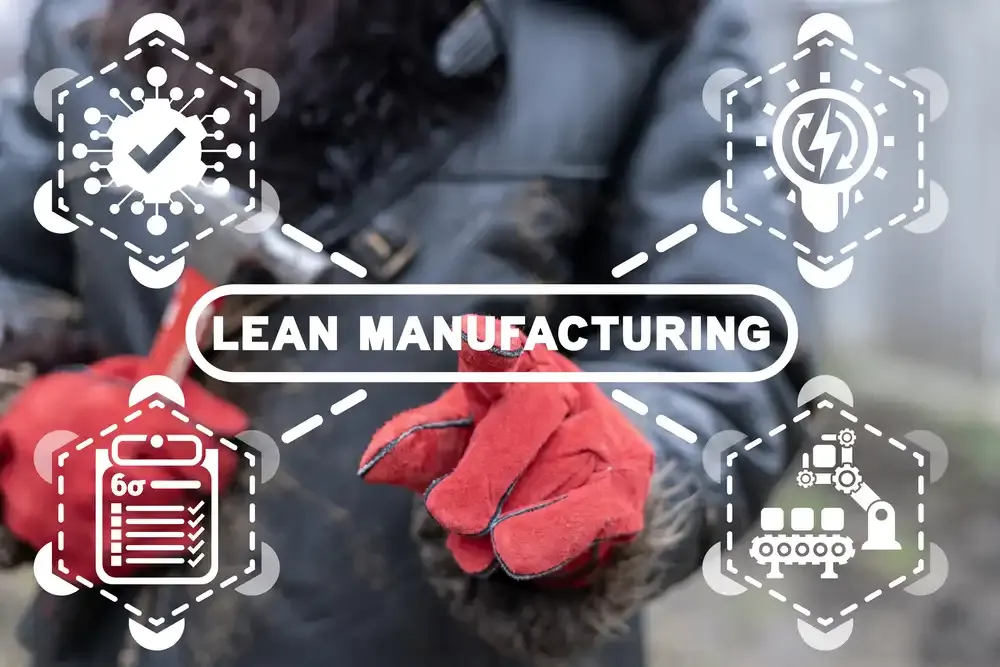
Lean Manufacturing 101
Lean manufacturing is all about eliminating waste and maximizing productivity. To effectively implement lean processes, companies must address some key principles.
Key Principles of Lean Manufacturing
Lean methodology can improve processes and increase efficiencies, but the strategy must be monitored to ensure progress. To achieve this, lean thinking must address each lean principle:
- Identifying Value: Understanding what adds value from the customer's perspective.
- Mapping the Value Stream: Analyzing the flow of materials and information to identify waste.
- Creating Flow: Ensuring that the production process flows smoothly without interruptions.
- Establishing a Pull System: Producing only what is needed when it is needed.
- Striving for Continuous Improvement: Constantly seeking ways to improve processes.
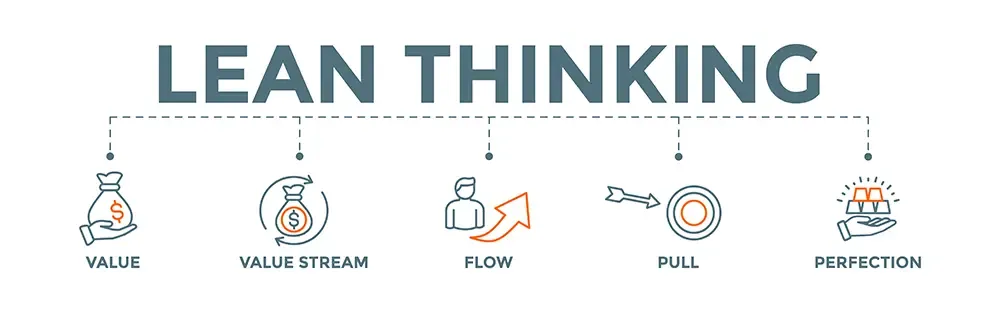
Different lean methods—like continuous flow, value stream mapping, Kanban, and Lean Six Sigma—can help manufacturers reap the benefits of lean manufacturing principles.
Lean Process Improvement Benefits
An organization can also use lean processes to reduce inventory and improve quality, which aids in increased customer satisfaction. Additionally, lean practices can reduce costs and increase profits, meaning a healthier overall company.
Most Common Obstacles of Lean Processes
Not all companies have the resources that lean implementation requires, so time and money can be obstacles for manufacturers striving to use lean manufacturing principles. Another common challenge to implementing lean is buy-in from stakeholders who focus on potential drawbacks of lean strategies, such as:
- Lean principles might be difficult to standardize throughout the company.
- The strategy must be constantly monitored to ensure continuous improvement and progress.
- Many changes must be implemented at once.
Fortunately, tools exist to help overcome these obstacles. Perhaps one of the most important lean process improvement tools is the A3 problem-solving method.
The A3 Method in Manufacturing
The A3 process sounds simple: compile problems and potential solutions on one side of an A3 (11”x17”) piece of paper. Since the Toyota Motor Corporation created the A3 method, it has evolved into a complex problem-solving and team-building business strategy.
Understanding the A3 Method
The A3 method began in the 1940s as part of the Toyota Production System. Management at the Toyota Motor Company wanted succinctly summarized concerns, problems, and solutions, and the A3 process allowed managers to prioritize information on their A3 report. It also saved senior managers time by having the important information clearly organized on a single sheet of paper.
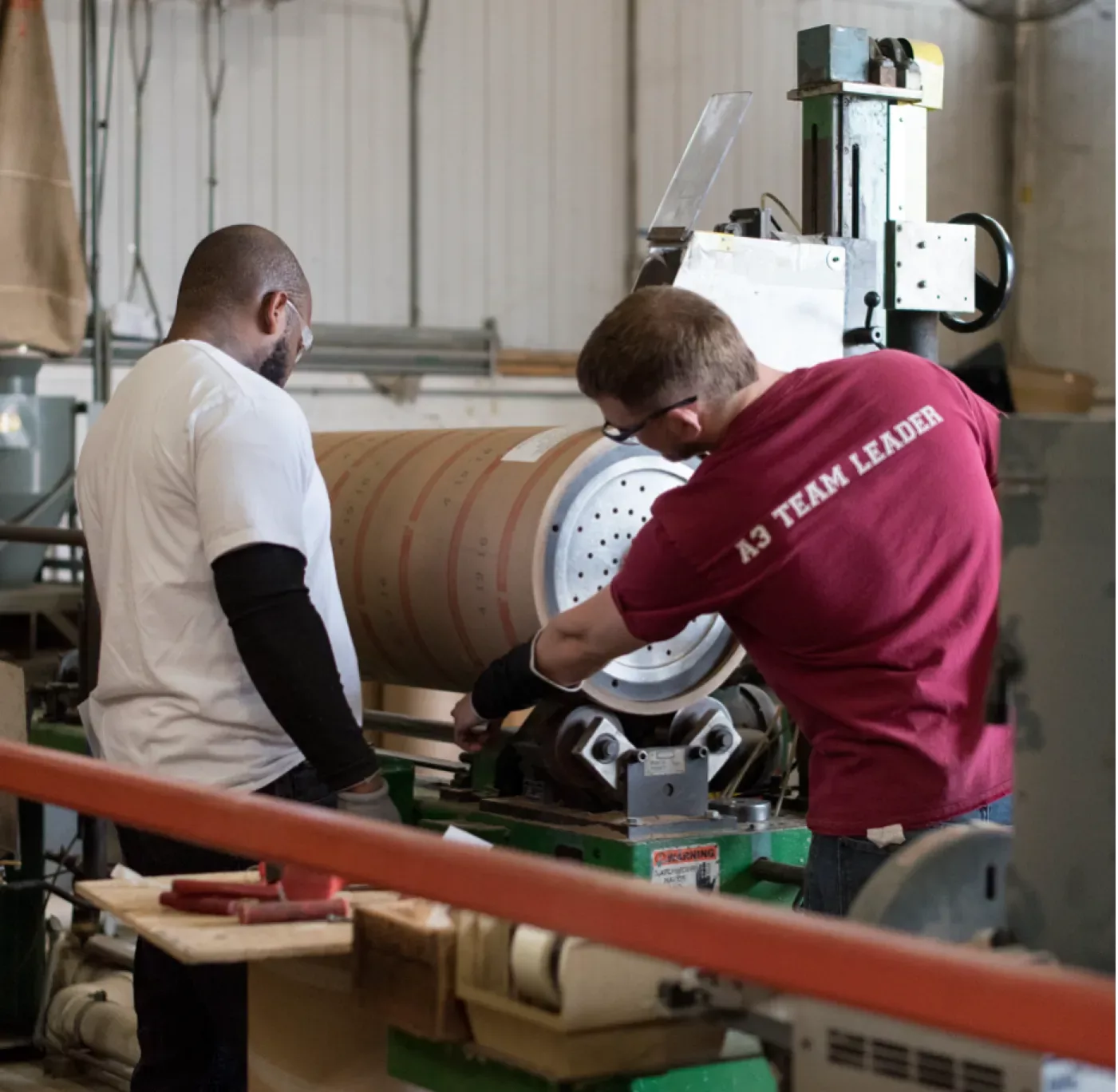
Since then, A3 thinking has evolved to become more than a problem-solving tool. The A3 method is now used to increase collaboration and help develop employees and teams.
How the A3 Method Works
The A3 process involves several steps:
- Identify the problem.
- Determine why the problem exists.
- Define the goals and outcomes.
- Develop an implementation plan.
- Obtain stakeholder buy-in.
- Implement the plan.
- Evaluate results.
There’s no universal A3 template, so these steps may have to be adjusted to meet an organization’s goals. If a company feels that the A3 method isn’t the best fit for their unique situation, there are other lean process strategies they can try.
A3 and Other Lean Process Strategies
Although A3 thinking has improved many organizations, it’s not ideal for every company. One alternative is value stream mapping. This method provides a visual flow diagram used to identify and reduce waste and pinpoint where process changes will be most impactful. Another tool is 5S (sort, set in order, shine, standardize, sustain), which helps create and maintain a healthy, productive work environment.
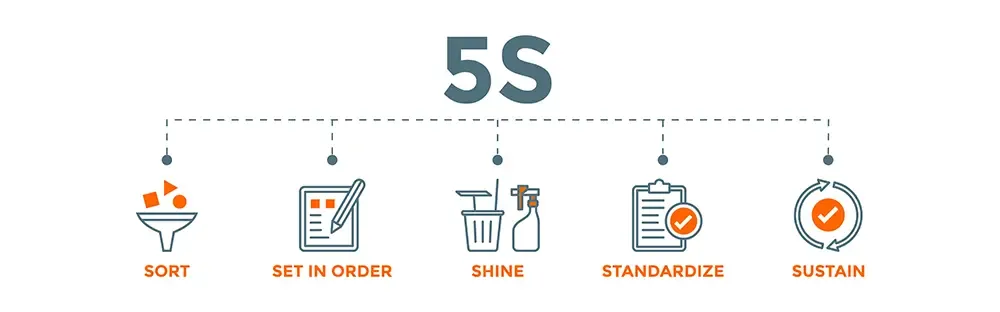
In addition to lean tools, there are plenty of examples of lean process improvements.
Examples of Lean Process Improvements
Implementing lean strategies is a complex process, so manufacturers must employ proper techniques and tools to ensure success.
Lean Manufacturing Techniques
Lean manufacturing techniques aren’t universal, and manufacturers must determine what works for them. Here are a few of the most popular lean process improvement methodologies used in manufacturing:
- Kanban: Strives for continuous communication and full transparency for the goal of improved workflow.
- Lean Six Sigma: Increases collaboration and reduces operational waste.
- Total Quality Management: Outlines long-term success via customer satisfaction.
- Work in Progress (WIP) Limits: Helps identify inefficiencies by determining the maximum amount of work possible.
Within these techniques, companies can implement tools for lean process improvement to upgrade the organization.
Tools for Lean Process Improvement
Manufacturers might combine multiple tools to implement lean processes. Perhaps a company already uses the A3 method, value stream maps, and a 5S system. The company might want to add bottleneck analysis to identify wasted time, just-in-time (JIT) manufacturing where it only produces items to meet demand, or a plan-do-check-act (PDCA) cycle to continually improve processes.
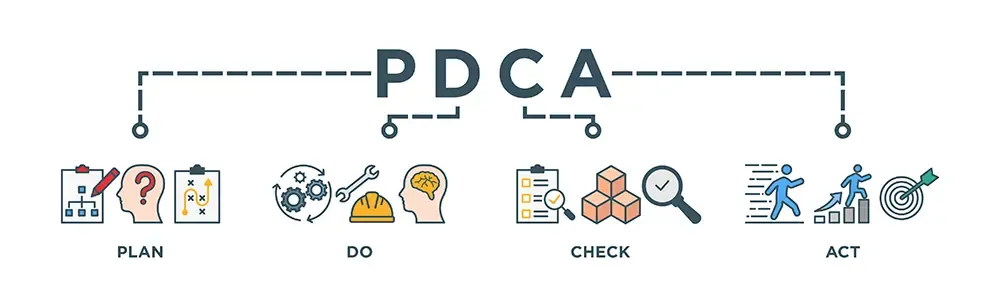
Sometimes it’s difficult to identify root causes or viable solutions. In these cases, a why analysis can help to fix the problem and begin to see improvements in the lean process.
Lean Process Improvements in Action
Implemented correctly, lean can improve a manufacturer’s production process. Here are examples of improvements due to lean manufacturing implementation:
- Reduced time and cost to manufacture parts.
- Reduced inventory and improved warehouse management.
- Improved employee satisfaction and productivity.
- Improved customer service.
Though it takes time and resources to implement, the results of lean process implementation can change the scope of the organization for the better.
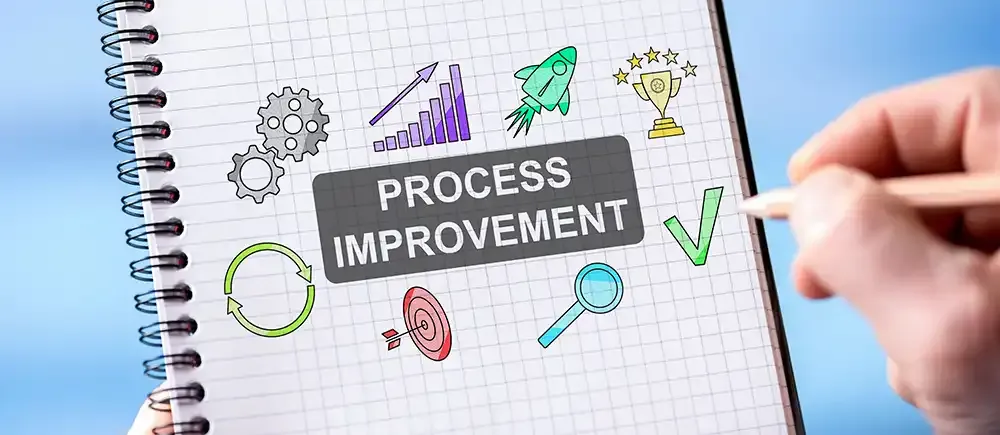
How to Implement Lean Processes in Manufacturing
Lean manufacturing implementation is a complex business process. To successfully implement it, certain steps must be followed.
Steps to Lean Processes in Manufacturing
Each company’s specific steps to implementing lean manufacturing will be unique. However, most will include the following:
- Identify and analyze which processes need improvement.
- Identify the improvements that should be made.
- Implement process improvement tools and techniques.
- Monitor process improvement execution.
- Assess the value of process improvement efforts.
This assessment includes identifying what activities add value, limiting risk, standardizing the process, ensuring compliance, and improving the customer experience.
If the implementation can identify value, create flow, and achieve other lean goals, their lean manufacturing strategy can work together with a continuous improvement philosophy.
Lean Manufacturing and Continuous Improvement
Continuous improvement is an organizational approach that improves overall operations. Lean manufacturing can minimize waste and maximize productivity and may be used as part of the continuous improvement strategy.
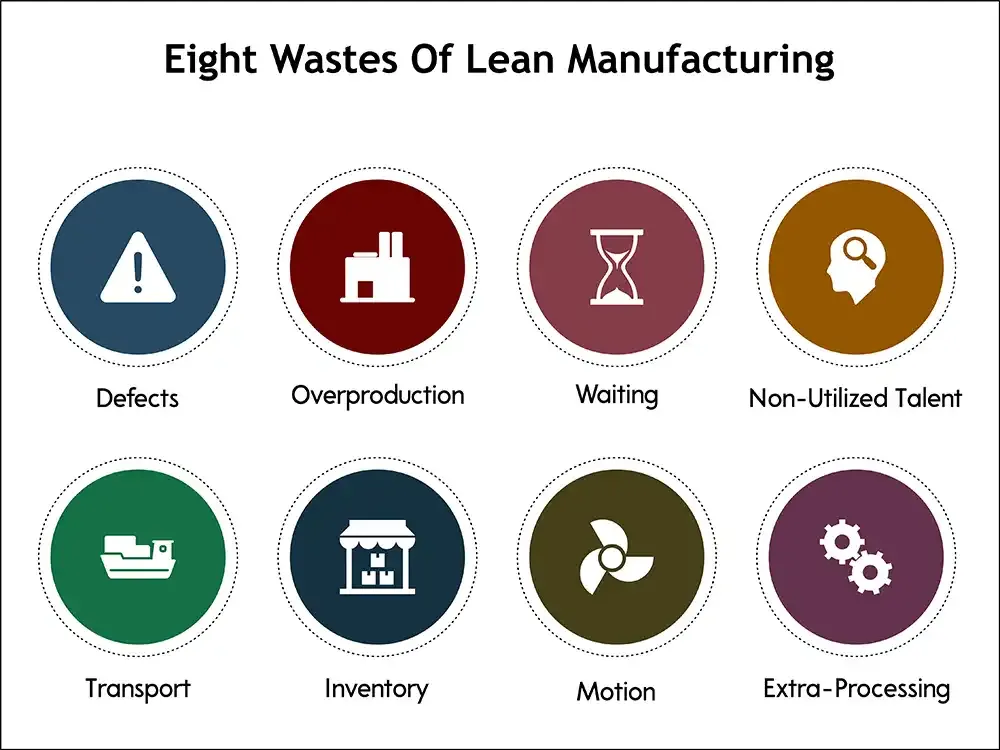
With tools like lean manufacturing and A3 in practice, a company has set itself up with the keys to success.
Keys to Success
Lean manufacturing can’t be implemented overnight. Here are a few ways to help the implementation succeed:
- Develop the lean manufacturing strategy.
- Obtain buy-in before implementing.
- Implement slowly.
Lean process improvement tools are essential for all manufacturers. Embracing lean goes beyond just implementing a business process; it represents a comprehensive methodology, philosophy, and mindset. This holistic approach leads to the creation of better products, more efficient workflows, and ultimately, happier customers.
Contact Ulbrich Today
Ulbrich uses the lean manufacturing process to ensure high-quality products, improved lead time, and increased customer satisfaction. But lean isn’t just for manufacturing processes and production— everything from routine paperwork and customer satisfaction to credit, invoicing, certifications, and material renewal can be improved with lean methodologies.
Let us show you how our holistic lean approach means a better customer experience for you. Contact an Ulbrich specialist today to learn how we can become an extension of your team.