Inconel 718 vs. Inconel 625: Battle of the Titans
Some of the most advanced industrial applications today—especially those in the aerospace, automotive, and oil and gas industries—rely on alloy materials with exceptional strength and technical performance. Among these materials are two superalloys known as Inconel 718 and Inconel 625. These Inconel alloys together are used in several products that require high strength, high temperature resistance, and strong corrosion resistance. It’s critical to understand the differences between Inconel 718 vs. Inconel 625 in deciding which superalloy can best meet the end use requirements of a manufacturing process.
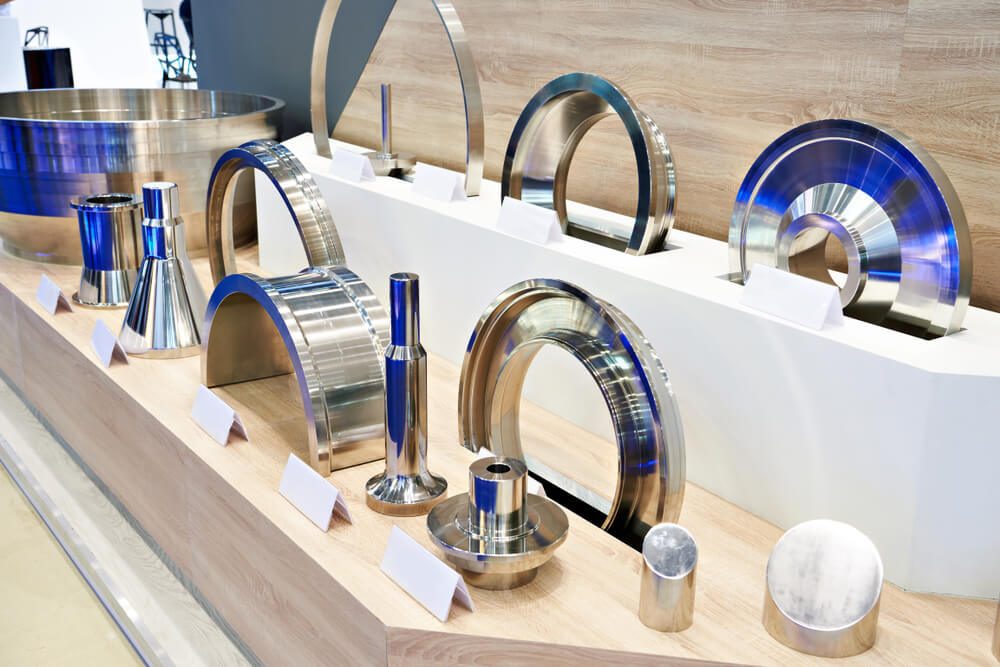
The history of superalloys dates back to the 1950s and 1960s, when researchers combined molybdenum and niobium with nickel to produce extra-strong alloys. Inconel 625 was first in development, driven by a need for strong steam-line piping products in steam power plants. The research was disrupted, however, when it incidentally led to the discovery of another superalloy, Inconel 718. Proving immediately useful for applications in the aerospace industry, particularly airplane engines, Inconel 718 raced its way to patent approval in 1962.
After the brief disruption by its older brother, Inconel 625 was filed at the patent office in the same year. As steam-line piping became less important, Inconel 625’s use would center on aerospace applications and additional industries.
Specifications of Inconel 718 vs. Inconel 625
Inconel 718 and Inconel 625 share many properties of the Inconel alloy family and more broadly share properties of the nickel alloy and stainless steel families. However, they also have discernible distinctions that make for unique use cases.
Inconel 625 is composed mainly of nickel and chromium. It also includes molybdenum and niobium, which provide for its high tensile strength and corrosion resistance, including resistance to crevice corrosion. Columbium and molybdenum account for its high strength in environments with a cryogenic temperature or a very high temperature. Inconel 625 can maintain its strength in environments up to 2,000° F, and according to its technical bulletin, it provides good oxidation resistance and resistance to carburization.
Inconel 718 generally has a similar chemical composition to Inconel 625, with small variations. Inconel 718 is remarkable for its ability to be precipitation hardened without succumbing to post-weld cracking, also according to the technical bulletins linked above. It can also resist creep rupture at temperatures up to 1,300° F. Because of this capability, Inconel 718 can maintain high tensile strength while also possessing alloy characteristics like high formability.
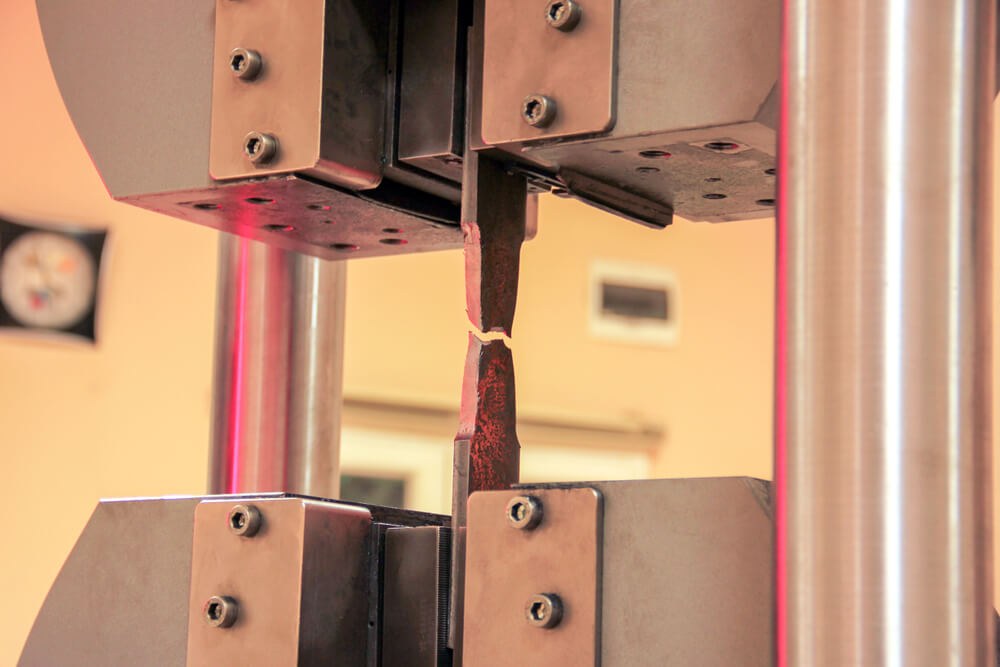
High weldability makes Inconel 718 similar in some ways to general stainless steel grades. Inconel 625 in annealed condition, on the other hand, can be significantly stronger and, as mentioned, particularly suited to resisting corrosion, including that caused by sea water environments.
Differences in Formability between Inconel 718 and Inconel 625
The high concentration of nickel in both types of Inconel alloy leads to generally high levels of formability. Both Inconel 718 and 625 can be stamped and cold formed. While both have exceptional tensile strength, Inconel 718’s resistance to post-weld, or strain-age, cracking during heat treatment makes it particularly suited to formability while maintaining high strength in an annealed condition.
Because of the shaping qualities of Inconel alloy, these materials can be rolled through a wire mill to produce various wire profiles for industries like aerospace and oil and gas. They can also be used to produce honeycombs, seal rings, bellows, and springs. They also serve as high performance fastener alloys for extreme conditions, including those where corrosion is likely.
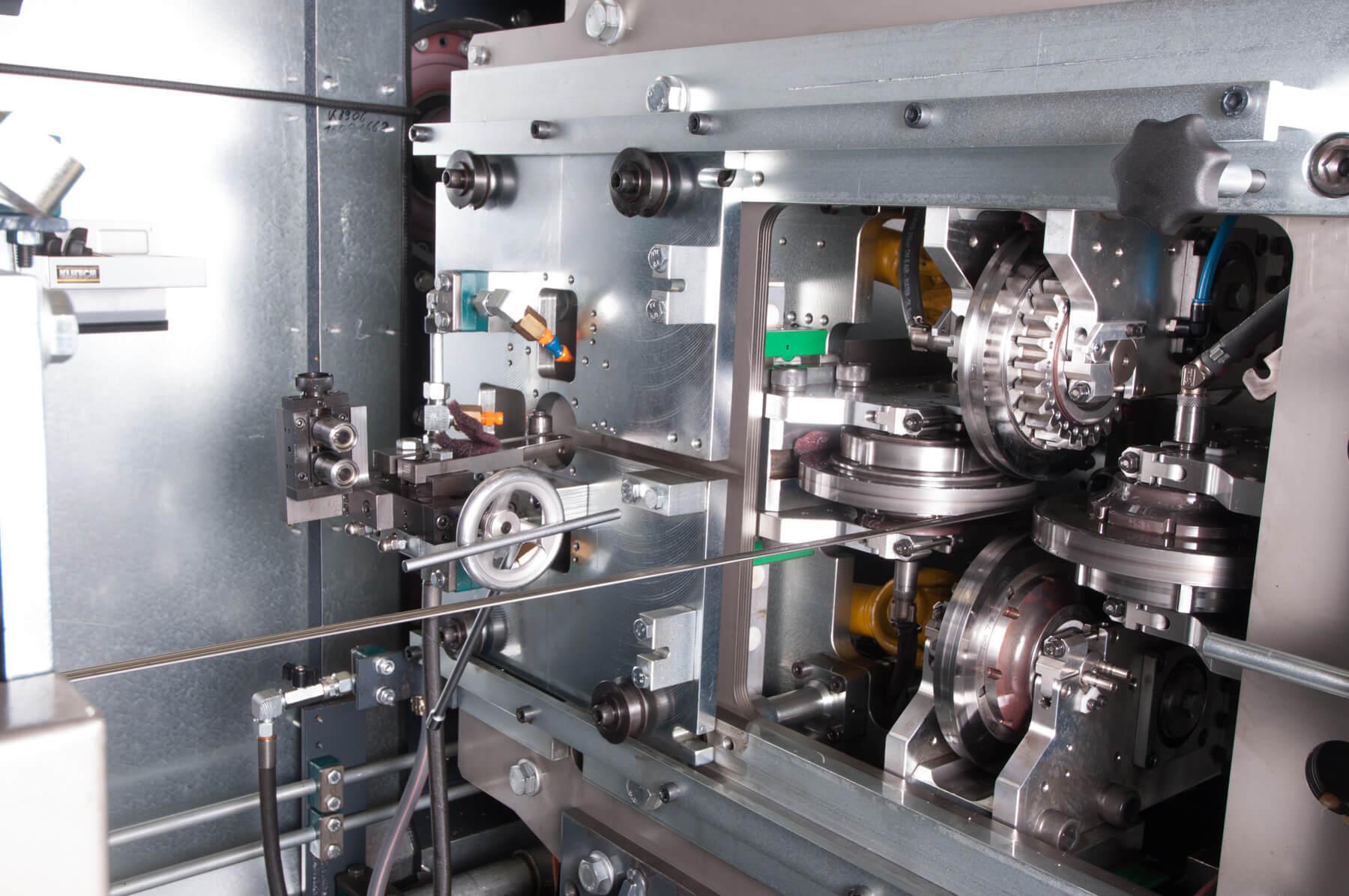
Common Uses for Inconel 718 and 625
Both Inconel 718 and 625 can be used in multiple forms of manufacturing applications. Product forms include strip, ribbon, and shaped wire, as well as round, flat, and square wire. Notably, neither of these alloy types are commonly deep drawn.
The two superalloys can be used for a variety of stamped parts—such as a diaphragm for a sensor measuring device. They’re especially helpful when resistance to high temperature and high-pressure conditions are needed. Inconel 625 particularly is used for flexible metal hoses, heat exchangers, header bars, and marine components due to its considerable strength in environments of elevated temperatures and corrosion, as well as its oxidation resistance.
Industries That Commonly Use Inconel 625 and Inconel 718
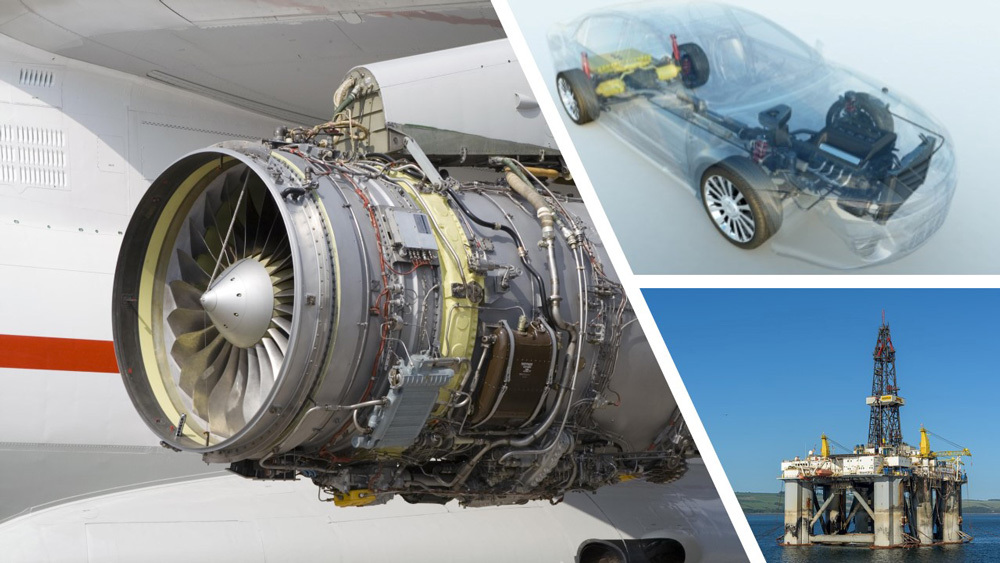
As already mentioned, Inconel 718 started its life in the aerospace industry and has only become more widespread in that field. According to one study, the alloy makes up more than 30 percent of a modern aircraft engine’s finished component mass. Airplane engines are an obvious use case for a high temperature alloy that can hold up in a high pressure, highly corrosive environment of burning jet fuel and extraordinary propulsion.
Similarly, car engines create high-stress environments for component alloys. Many components of automobile engines benefit from the use of a superalloy with high formability provided by the nickel content. An Inconel alloy can meet the specific shape needs of applications in the car engine while also maintaining the high corrosion resistance needed to ensure long-term reliability.
Because of its corrosion resistance, especially in sea salt environments, Inconel 625 has many marine industry uses as well. This includes oil and gas industry needs, such as downhole drilling applications like tieback on undersea lines. Inconel 625 is also applied in sea water environments for telecommunications lines, propeller blades, and wire ropes.
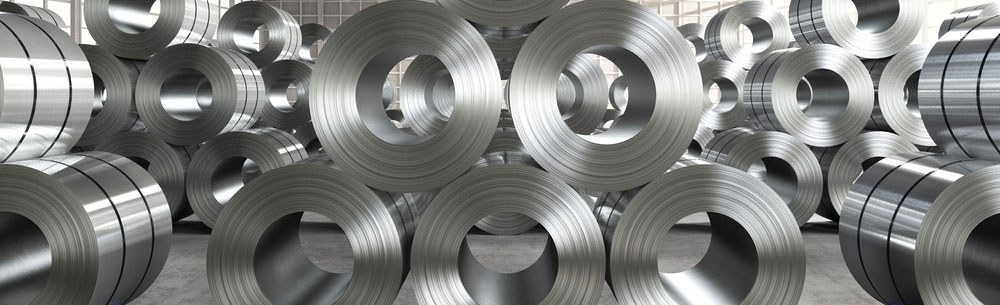
Understanding the differences between the titans of metal products, from stainless steel to nickel alloy to superalloys like Inconel 718 and 625, is critical for engineers and manufacturers. Also key is an understanding of how these alloys respond to various operations like stamping, deep draw, roll forming, and micro-laser welding. Even the most skilled buyers of alloys and most experienced mechanical engineers can benefit from the expertise of metallurgists who understand the properties and uses of alloys inside out. The team at Ulbrich Stainless Steel has the expertise to help customers procure the alloys that work best for their end use needs.