How to Balance Cost and Availability When Selecting Materials for Precision Metal Stamping
Precision metal stamping is an essential process across industries such as automotive, aerospace, medical devices, and electronics. A critical aspect of this process is selecting the right alloy, as this decision influences not only the performance but also the cost, formability, and corrosion resistance of the final product. Engineers often prioritize materials that seem technically impressive but may overlook factors like high-temperature performance, manufacturability, and cost implications. Selecting the wrong alloy can lead to challenges such as increased tool wear, higher part rejection rates, and overall inefficiencies that impact the bottom line. This article explores these considerations to help manufacturers balance cost and performance while meeting engineering requirements.
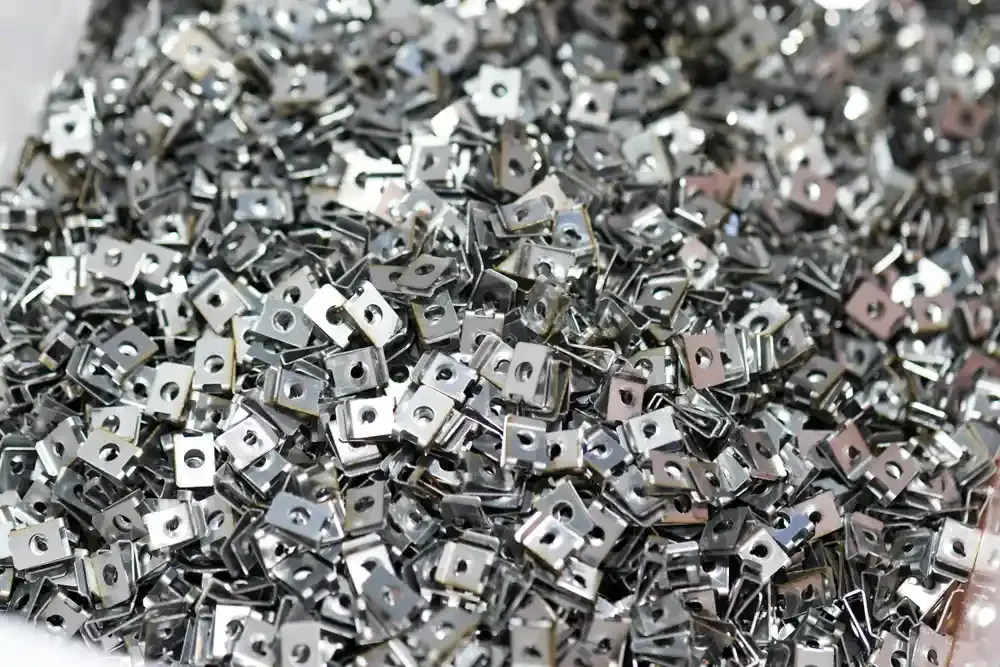
Cost Analysis: High-Volume Production vs. Specialty Components
For high-volume production, the choice of material significantly impacts overall costs. Materials like stainless steel and aluminum are often favored for their reliability and scalability. Total costs for large material orders can be steep, making it essential to work with suppliers who offer innovative sourcing strategies related to material selection and performance considerations to maximize efficiencies and yields.
On the other hand, specialty components may require materials with unique properties, such as titanium alloys or nickel-based superalloys. These materials are often costlier due to their specific attributes, including the ability to withstand extreme environments or deliver exceptional strength-to-weight ratios. However, the cost is not only influenced by the material itself but also by what is physically required to process these alloys. For example, achieving tight tolerances or specifying mechanical properties beyond standard ranges can significantly drive-up prices due to the additional labor, precision tooling, and quality control measures involved. A thorough cost-benefit analysis helps manufacturers weigh these trade-offs between material performance, processing requirements, and overall cost.
Material Availability and Its Impact on Manufacturing Timelines
Material availability is a critical factor influencing production schedules. Disruptions in the supply of raw materials can lead to delays, impacting delivery timelines and customer satisfaction. Lower-demand materials for high-performance applications, including certain stainless steel grades or specialty alloys, may have longer lead times due to production complexities or limited global supply. For instance, alloys like 718 often undergo double vacuum melting processes, such as Vacuum Induction Melting (VIM) followed by Vacuum Arc Remelting (VAR), to achieve the desired material properties. Similarly, titanium alloys require specialized processing techniques to maintain their unique properties, which can also contribute to longer lead times.
Partnering with reliable suppliers who maintain robust inventories and leverage their relationships with melt mill suppliers can mitigate risks associated with material shortages. Additionally, understanding market trends and anticipating fluctuations in material availability enables manufacturers to plan effectively.
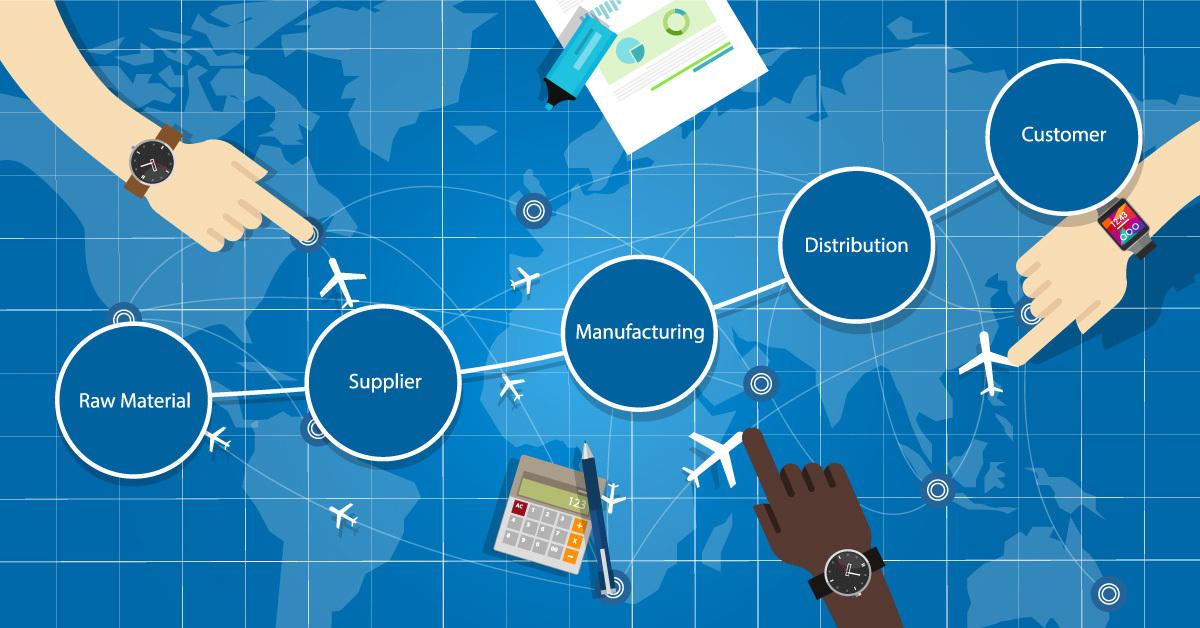
The Role of Global Supply Chains in Metal Procurement
Global supply chains play a pivotal role in the procurement of metals for precision stamping. Factors such as geopolitical tensions, tariffs, and logistical bottlenecks can affect pricing and availability. Manufacturers must stay informed about these dynamics to adapt their sourcing strategies accordingly.
Partnering with a vendor that maintains a diverse supply network, including relationships with multiple melt mills, can provide manufacturers with greater flexibility and resilience. This approach reduces the risk of being tied to a single source, ensuring more consistent material availability even during disruptions.
Additionally, collaborating with suppliers who prioritize transparency and traceability ensures compliance with regulatory standards and builds trust in the supply chain.
Best Practices for Achieving Cost-Performance Balance in Material Selection
- Collaborate with Material Experts: Engaging with metallurgical experts and engineers can help identify materials that meet performance requirements without unnecessary cost premiums.
- Leverage Supplier Relationships: Building a strong partnership with a supplier facilitates access to technical support, insights into emerging material technologies, and consistent sourcing options that can reduce total costs and risk.
- Consider Long-Term Costs: While lower-cost materials may seem appealing, a deeper evaluation of their impact on production is essential to calculate true cost-effectiveness. Materials that are inconsistent in quality, have loose tolerances, or exhibit issues with chemistry can lead to extended setup times and frequent adjustments during production. For instance, high-quality materials, like those sourced from Ulbrich, often require minimal tool changes, allowing manufacturers to quickly achieve a reliable setup and maintain consistent run rates throughout an entire coil. In contrast, lower-cost materials—sometimes sourced from regions with less stringent quality controls—can result in longer setups, repeated tweaks, and unanticipated downtime. These inefficiencies, coupled with increased tool wear, maintenance, and part rejection rates, can drive up costs significantly over the long term. Investing in high-quality, reliable materials ensures smoother operations, better performance, and ultimately, a more cost-effective production process.
- Optimize Material Utilization: Using advanced stamping techniques and minimizing scrap can reduce material waste, further driving down costs.
- Evaluate Sustainability: Selecting materials with recyclability or lower environmental impact can align with corporate sustainability goals while mitigating future regulatory risks.
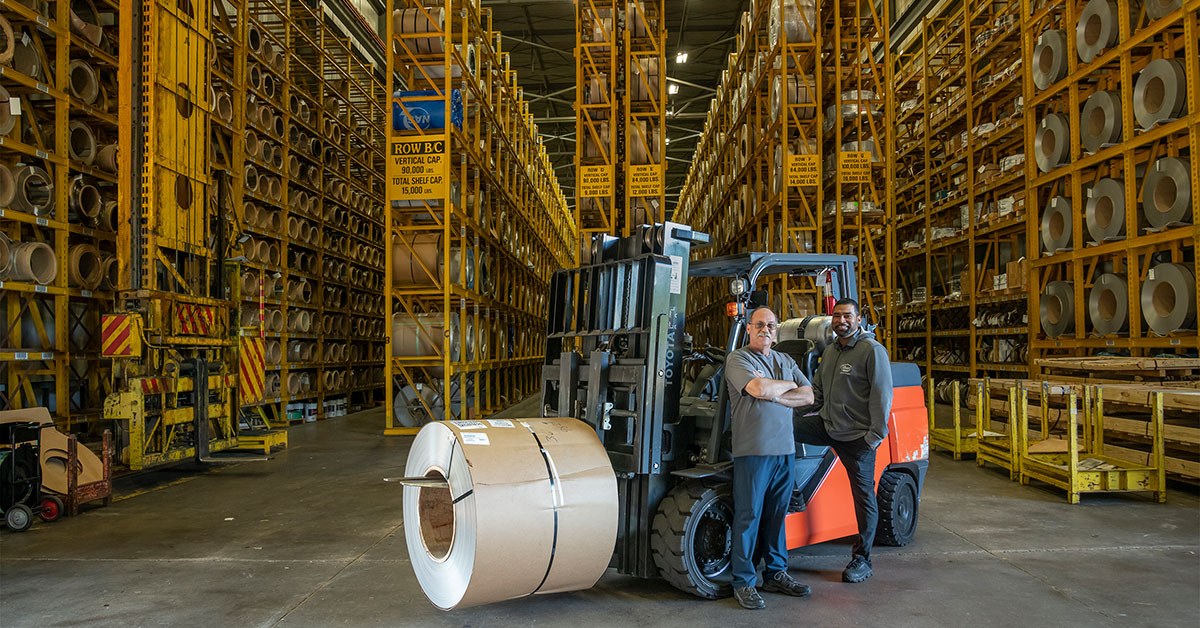
Partner with an Experienced Supplier
Navigating the economic considerations of material selection for precision metal stamping requires a comprehensive approach. By analyzing costs, addressing supply chain challenges, and adopting best practices, manufacturers can ensure that their material choices support both cost-effectiveness and performance.
Partnering with experienced suppliers, like Ulbrich Stainless Steels & Special Metals, ensures access to high-quality materials and expert guidance, helping manufacturers achieve success in high-volume and specialty production runs.
For more information on how Ulbrich can support your material needs, contact us today!