Hastelloy Metals and Alloys: A Complete Guide for Manufacturers and Engineers
Hastelloy® metals and alloys are known for their superior ability to withstand high temperatures and corrosion. Haynes International first developed these types of superalloys, following the invention of stainless steel in 1913.
Stainless steel and Hastelloy alloys both offer incredible strength and formability under stress, and good ductility. However, Hastelloy alloys resist corrosive chemicals and acids, such as hydrochloric acid, which distinguishes them from other alloys. Additionally, a metallurgist can engineer a superalloy to withstand oxidizing agents.
What are Hastelloy metals and alloys?
Metals, such as silver or copper, are pure elements, whereas alloys are manmade mixtures of two or more elements. Although stainless steel and Hastelloy alloys may be used in similar applications, there are some key differences between these materials.
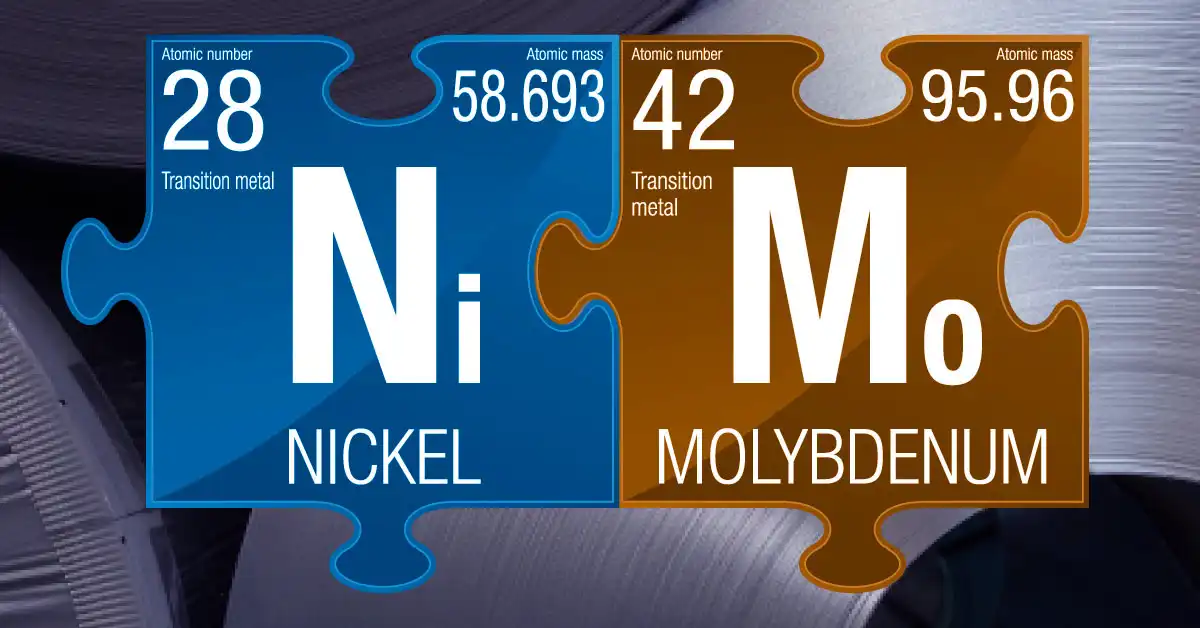
Stainless steel and Hastelloy alloy differences
Nickel and molybdenum are the primary ingredients in any of the Hastelloy alloys. Nickel is a naturally occurring silvery metal with a melting point of 2,651ºF. It is highly resistant to corrosion.
Similarly, molybdenum is a shiny, silvery metal with an incredibly high melting point of 4,752ºF. It’s used to enhance the strength, electrical conductivity, and hardness of certain alloys.
On the other hand, stainless steel is fortified with nickel and chromium. Chromium acts as an agent to prevent rusting. However, the presence of higher percentages of nickel and molybdenum make Hastelloy metals and alloys more resistant to corrosion than stainless steel, especially in elevated temperatures.
Hastelloy alloy optimization
Although all grades of Hastelloy alloys are corrosion resistant, certain grades have been optimized for specific purposes. The mechanical properties of different grades of alloys determines their impact on deep drawing, stamping, and welding processes.
Hastelloy alloy grades
Along with containing nickel and molybdenum, the different grades of Hastelloy alloys may contain percentages of iron, aluminum, tungsten, carbon, titanium, chromium, and other elements. The most widely used and versatile Hastelloy alloys are the C-types.
Formulated in 1952, the Hastelloy X alloy is a more recent grade of superalloy compared to others. It contains higher percentages of iron to improve oxidation resistance, formability, and high temperature strength. It can also be cold rolled to meet desired temper properties; however, it cannot be hardened by heat treatments.
B-type alloys
B-type alloys are known for their high percentages of nickel and molybdenum. Like nickel, molybdenum offers high resistance to corrosion. It is notable for its ductility and has one of the highest melting points of all the naturally occurring elements. These alloys are formulated to withstand extreme reducing conditions, such as environments with hydrochloric, hydrobromic, and sulfuric acids.
B-2 alloy
This grade of alloy typically contains 65 percent nickel, 30 percent of molybdenum, and small percentages of iron, carbon, cobalt, chromium, manganese, silicon, phosphorus, and sulfur. It offers superior corrosion resistance to hydrochloric acids at any concentration or temperature. However, it is not resistant to oxidizing agents.
B-3 alloy
The B-3 alloy has an average composition of 65 percent nickel, 30 percent molybdenum, with trace amounts of manganese, cobalt, and chromium. It provides excellent resistance to pitting and corrosion, along with superior thermal stability compared to the B-2 alloy. Like the B-2 alloy, it is likely to prematurely deteriorate if exposed to oxidizing agents.
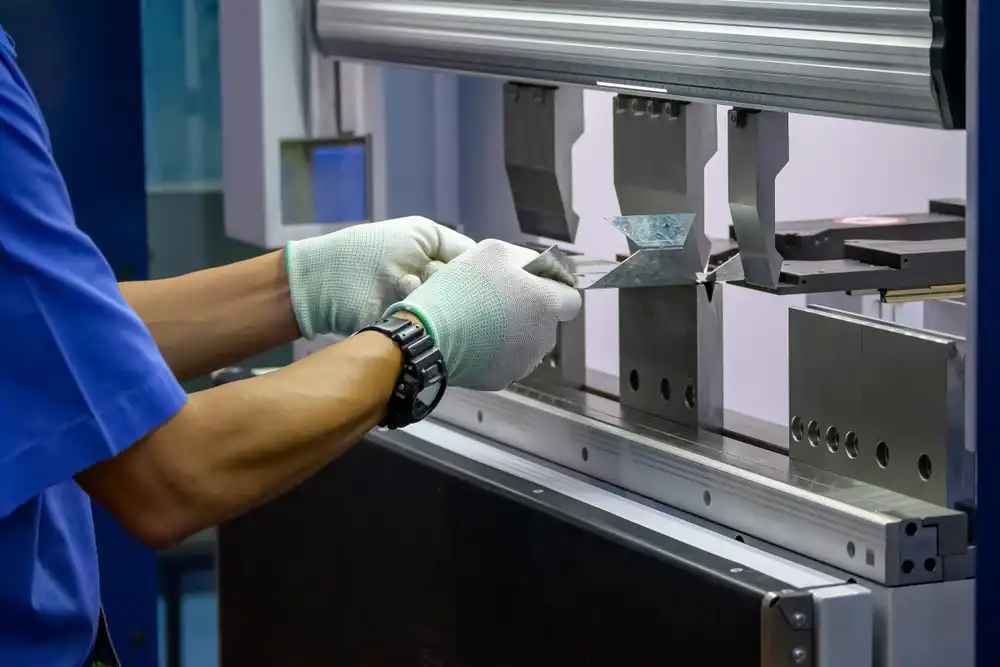
C-type alloys
Alloys that fall within the C-family have high percentages of nickel, molybdenum, and chromium. The addition of chromium increases the formability of these types of alloys, allowing them to withstand elevated temperatures and reducing atmospheres. Most C-type alloys can be formed using different cold and hot working methods, such as deep drawing, press forming, and punching.
C-4 alloy
The C-4 alloy consists of about 60 percent nickel, 18 percent chromium, 16 percent molybdenum, 3 percent iron, and 2 percent cobalt. The remainder comprises silicon, sulfur, carbon, titanium, and other elements. Along with corrosion resistance, it has a high ductility, which makes it suitable for deep drawing.
C-22 alloy
The C-22 alloy is one of the most used alloys for flue gas desulfurization systems and pharmaceutical reaction vessels. Usually, it contains about 58 percent nickel, 20 percent chromium, 13 percent molybdenum, 3.5 percent iron, 3 percent tungsten, and 2.5 percent cobalt, along with other trace elements. It is widely used for its weldability; however, it should not be used in environments exceeding 1,250ºF.
C-276 alloy
This type of alloy is the standard for petrochemical processing applications. Most of its composition is nickel. However, it contains an average of 16 percent molybdenum, 15 percent chromium, 5.5 percent iron, 4 percent tungsten, and minute percentages of other elements. It provides excellent resistance to pitting, intergranular corrosion, and oxidizing agents. However, it does not perform well in environments with hot concentrated nitric acid.
G-type alloys
G-type alloys typically contain tungsten, which has the highest melting point of all metals. This family of alloys can be welded using certain techniques, such as gas tungsten arc welding, submerged arc welding, and shielded metal arc welding.
G-3 alloy
This alloy has high percentages of tungsten and molybdenum, which makes it resistant to corrosion. On average, it consists of 22 percent chromium, 20 percent iron, 7 percent molybdenum, and a maximum of 5 percent cobalt. It contains trace amounts of other elements, with nickel being the dominant trace ingredient.
G-30 alloy
The G-30 grade is about 40 percent nickel, 30 percent chromium, 15 percent iron, and 5 percent cobalt, with traces of other elements. It is especially resistance to wet process phosphoric acid.
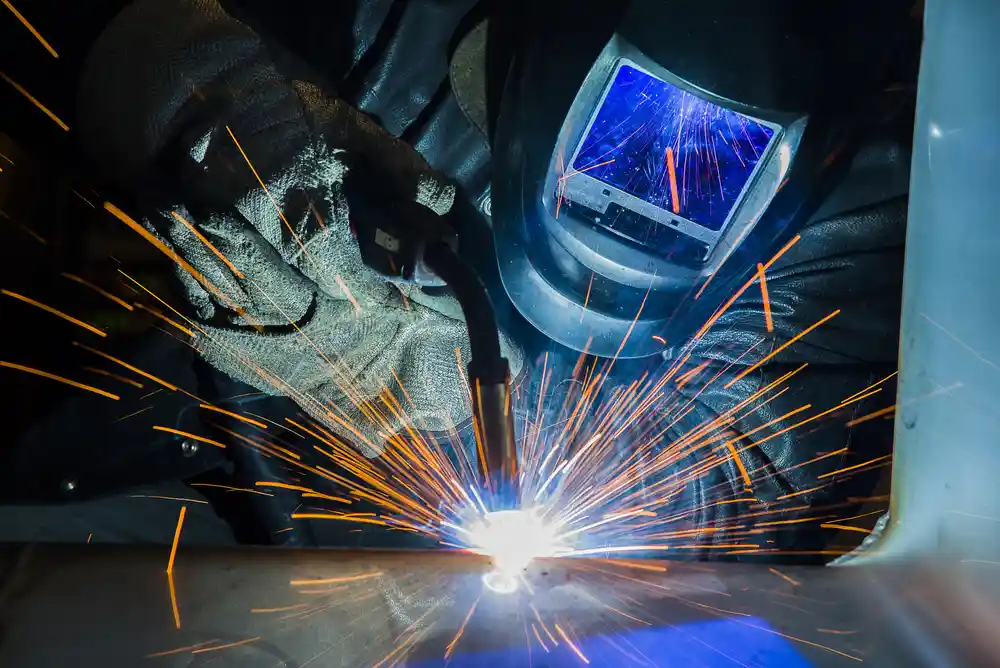
Benefits of Hastelloy alloys
Because of their durability, excellent corrosion resistance, and temperature resistance, manufacturers across multiple industries benefit from using Hastelloy metals and alloys. Although other materials may get the job done, these superalloys are easy to source and use in a variety of manufacturing processes.
Sourcing
Nickel is a highly available raw resource as it is the fifth most common element found on earth. It is also one of the most popular elements to mix with other metals for alloying. For this reason, Hastelloy alloys are relatively affordable to make and source.
Manufacturing
In general, Hastelloy metals and alloys can be welded with commonplace welding techniques. These techniques include gas metal arc welding, shielded metal arc welding, gas tungsten arc welding, and more. However, it is especially important to adhere to welding guidelines when using nickel-based alloys.
Using Hastelloy alloys, manufacturers can increase the longevity and reliability of their equipment and products. Costly mistakes, such as production bottlenecks, fixed asset losses, and worker injuries, are more likely to occur when parts break.
Applications for Hastelloy alloys
Hastelloy metals and alloys are widely used across multiple industries because of their enhanced mechanical properties. Because they can withstand moderate to severe corrosion, Hastelloy alloys are used in many welding, aerospace engineering, and chemical processing applications.
Aerospace
Because of their creep resistance and low expansion at elevated temperatures, many Hastelloy alloys are ideal for aerospace applications. Common applications of Hastelloy alloys within the aerospace industry include structural honeycombs, fasteners, connectors, engine components, and more.
Chemical Processing
Chemical processing is one of the largest manufacturing industries in the United States. From prescription drugs to cosmetics, it produces a vast range of commonplace products. In 2019, the chemical processing industry spent $10.1 billion on research and development. As technology and products evolve, so does the demand for better, stronger materials.
Hastelloy alloys can be used to build equipment parts in reactors, such as columns, piping systems, pressure vessels, heat exchangers, and more. Because of their excellent corrosion resistance, they can withstand many of the daily chemical reactions that take place in these facilities.
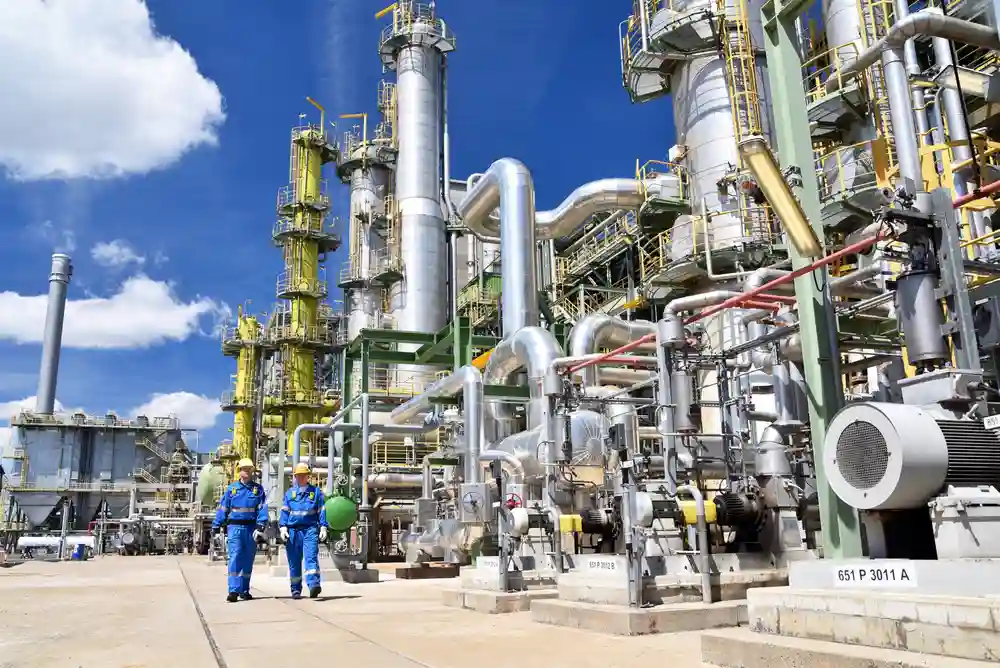
Where to source Hastelloy metals and alloys?
It’s important for manufacturers to know the chemical compositions of Hastelloy metals and alloys when sourcing materials for their projects. Knowing their chemical makeup can ensure that manufacturers invest in high quality, durable materials.
Ulbrich Stainless Steel is a trusted global leader in the production of precision metals and offers a wide selection of nickel-based alloys. They provide their customers with support from their metallurgists, as well as an extensive alloy and material database.
Whether you’re looking for strip or wire, Ulbrich will ensure you find the right Hastelloy alloy for any of your manufacturing needs. For more information, contact Ulbrich Stainless Steel here.