Evaluating 301 Stainless Steel Strip for Spring Applications
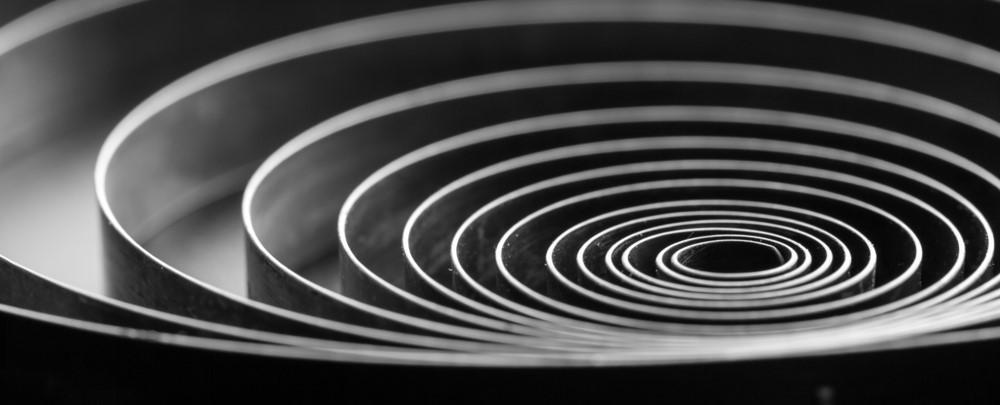
Springs are used in plenty of applications in the present-day world. Even so, only a few people have a nodding acquaintance with the brass tracks of spring manufacturing and the different qualities needed for various functions. While coiling steel into a spiral of desired length and diameter is the primary and center-most stage of spring fabrication, other treatments during and after the procedure determine the quality of the product that reaches the consumer. This article homes in on the manufacture of different grades of spring. We’ll look to give you useful insights into 301 stainless strip & wire and a general idea of how and where it can be used.
Here are some of the items that make use of springs:
- Toys
- Vacuum cleaners
- Door hardware
- Medical instruments
- Office equipment such as staplers and paper punches
- Umbrellas
- Spring scales
How to Choose Type 301 Stainless for Your Spring Application
Type 301 stainless steel strip is particularly well suited for the manufacturing of high strength room temperature springs. When 301 stainless steel strip is tempered to high strength levels it maintains its ductility with or without stress relieving.
301 has been long used for compression spring applications. Full Hard and Extra Full hard tempers being the most common ordering condition for traditional springs.
For those customers whose applications require high ductility at extra hard tempers beyond the traditional 301 capabilities, Ulbrich offers 301si.
301si has more formability at super high tensiles due to the addition of the extra silicon.
Traditional 301 (UNS 30100) stainless is used for most applications while 301Si (UNS 30116), with an increased Silicon content, is used for "super" high strength spring applications, such as Constant Force Springs used in a wide variety of end use parts and products we interact with day-to-day.
Standard 301 has a silicon content of 1.0 max and 301Si increases that content to 1.0 - 1.35. The extra silicon allows for good ductility at higher tensile strength. Both are produced to ASTM A666. The higher silicon results in increasing formability with less cracking. 301si improves the material's ductility because yield strength is not as limited as with traditional 301
What is the Bend Severity When Creating the Stainless Steel Spring?
Bend severity is basically the amount of coiling or bending that is applied on a 301 or 301Si stainless strip while creating a spring. As you would expect, the greater the bend, the more unstable the strip would be on the atomic level. The decision on whether further treatment of the material is needed is based partly on bend severity and partly on the intended use of the finished spring.
Does the 301 Stainless Spring Need Stress Relieving?
Stress-relieving is the process of easing the stress in a freshly coiled spring and creating a new equilibrium at the atomic level. It is usually applied on steel that was initially heated before being coiled into the spring. The stress is not a product of the heating. Instead, it is caused by the cooling that follows. Stress relieving is done by reheating the spring and letting it cool slowly.
Although most stress relieving is done on finished parts, Ulbrich may be able to stress relieve your 301 strip in our continuous furnaces. Stress relieving increases yield strength and hardness while reducing elongation.
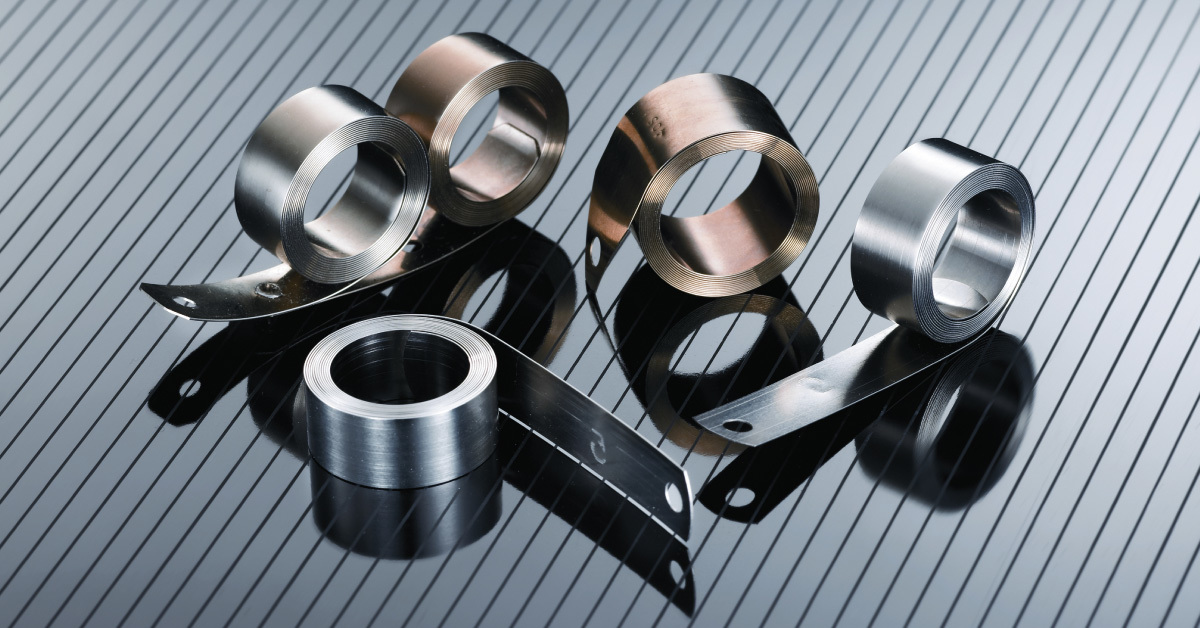
Is Fatigue Resistance Crucial to Performance of Your Application?
When discussing fatigue resistance, it is important to understand these two terms first:
- Elastic deflection, which can be defined as the displacement and returning into shape of a spring after a load is placed on it and removed.
- Plastic deflection, which is the degree to which the spring is permanently deformed after a load is placed on it.
When the elasticity limit of a metal is surpassed, it gets deformed. High strength spring materials generally have a higher elasticity limit and can hold more weight without losing shape.
Fatigue is a combination of these two phenomena. It explains the little plastic deformation that metals undergo when subjected to stress. Plausibly, materials with high fatigue resistance make longer-lasting springs and may come in handy when creating springs meant to come up against greater weight.
Corrosion and fatigue can also take a toll on the lifespan of a spring if much of the structure is eaten away. A 301Si stainless steel spring can perform better where there is a higher risk of corrosion and abrasion and in high-temperature environments.
Yield Strength:
When choosing the chemical composition (301 vs 301Si) of the material selected for your order and the amount of cold rolling, a wide range of tempers can be provided for your application. Stainless Steel 301 can be produced from 1/8 hard to Extra Full Hard with yield strengths ranging from 60 ksi to 280 ksi.
Ductility:
When 301 stainless is rolled to the highest strength levels (extra full hard) there are chemistry options (as noted above) that we can select to improve the material's ductility. Because the limiting factor in increasing yield strength is the loss of adequate ductility, our processing engineers can select from 301 or 301Si chemistry options and processing flexibility to create the best properties for your application.
What Material Should You Choose Based on the Spring's Operating Environment?
Overloading a spring can incredibly shorten its lifespan. However, performance and lifespan are also down to the conditions of the spring's operating environment. In high temperatures, the spring undergoes a similar process to as when it was being coiled. Its elasticity increases while its fatigue resistance falls.
Is Edging (Edge Condition) Needed on the Strip?
Edge rolling and deburring does away with sharp and imperfect ends, enhancing the spring's uniformity and reducing the risk of accidents. Edging produces better results when it is done before the spring is rolled.
Edges:
Ulbrich can provide your 301 stainless steel strip with deburred or skived edges. These coils can also be traverse wound to increase coil size and productivity.
How Would You Like the Steel Strip to be Packaged?
Oscillate wound coils offer such advantages as more footage on individual oscillating coils, fewer changeovers, longer tool life, functions welds, less scrap, fewer start-up problems, and reduced tool fatigue. An important thing to consider for packaging is the coil weight min/max of each packaging type your stainless steel strip mill offers.
Ribbon wound steel strapping, on the other hand, is easier to unroll and may come in handy where the 301 stainless strip is flat and has a reasonably large surface area. Type of packaging may also depend on the length of spring steel you have ordered.
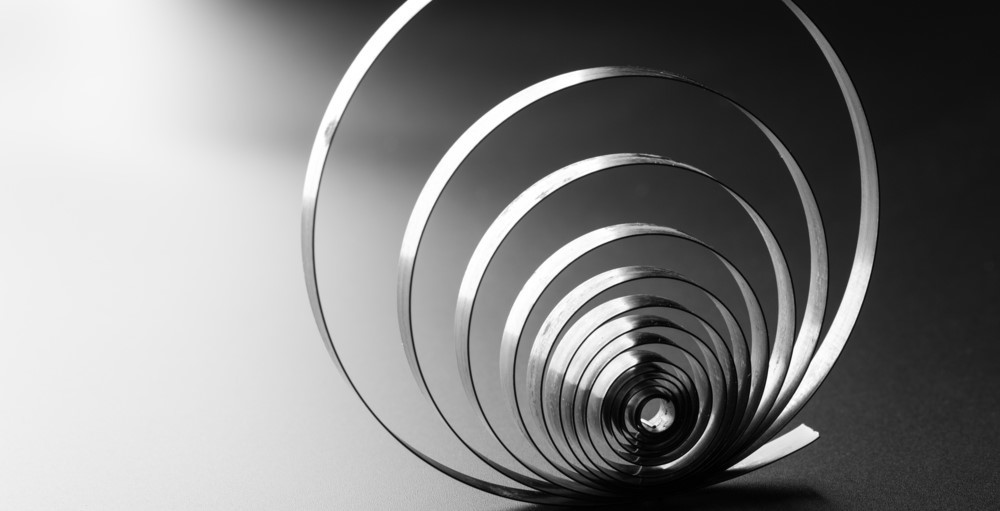
Which Alloy Properties Have the Most Importance to Your Fabrication?
Properties of a good spring material include high elasticity limits, low plasticity, high fatigue resistance, and resistance to corrosion. You may also have to consider the conditions of the environment where the spring is going to be installed as well as the stress it will handle. Some alloys such as medium- and high-carbon steels are considered spring metals as they naturally possess the properties required for a longer lifespan under constant stress. They have a relatively high combination of tensile strength and yield strength, which are two of the most essential properties of a spring material. Yield strength is the amount of stretch that needs to be applied on a metal to cause permanent deformation or plastic deflection.
Gauge Tolerance:
Gauge variation is limited by the use of Sendzimir mills or four-high mills with exacting automatic gauge controls. We can provide extremely tight gauge tolerances on our mills due to our state of art gauge controlling systems. Your requirements will be reviewed closely with our product specialists to engineer the best rolling process for your spring requirements.’
Flatness:
Rolling and leveling controls the 301 stainless steel strip's flatness. On material below .025 and within the tensile limitations of the equipment, stretchbend leveling can achieve critical flatness requirements. For material over .025" it is accomplished through precision rolling techniques.
Springback:
When stamping your 301 strip, controlling springback can be critical to your manufacturing process. By selecting very tight chemistry and a small range of acceptable yield this issue can be readily addressed.
What Finish Do You Need on Your 301 Strip?
Finish can be for cosmetic enhancement or rust prevention or both. You can apply passivation to your cold rolled spring steel after annealing it. Passivation does away with iron on the surface of the strip. An acid solution that targets iron and its compounds but doesn't corrode the surface of the steel is used. The iron deposits on the surface of the strip are formed during machining of the wire or spring.
Mechanical finishes, which are applied with abrasive pads or media, are also available.
Shot peening is another popular type of finish applied on spring steel to increase its lifespan. It involves impacting the surface of the metal with ceramic, glass, or metallic particles with enough force to cause plastic deflection. It is believed to increase the alloy's lifespan up to 10 times.
There is no doubt more than just a few factors come into play when choosing a suitable material to create a spring with. You have to find a metal that will produce the closest blend of properties to what you are looking for. If you are stuck or torn between options, 301 stainless steel is always a good place to start considering the numerous useful features it offers. Being a cold-rolled alloy, the metal has superior directional properties and has better tensile strength compared to other metals of its elasticity class. It is also corrosion-resistant and saves you the need for painting, plating, and other forms of surface treatment. Whether you are creating a spring for indoor or outdoor purposes, you are sure to find a number of these properties useful and cost-effective.
If you are looking to fabricate springs for whichever function, be sure to contact a specialist or call us for expert advice on selecting metals for spring applications.
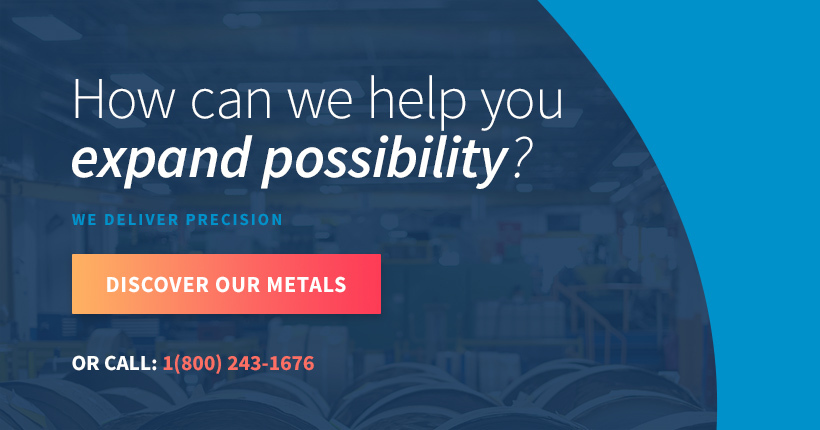