Common Metal Conversions and Units
It goes without saying that accurate measurements and unit conversions are critical to the world of precision metals. Challenging applications demand tight tolerances and the slightest unintended variation in the thickness of strip coil, or the gauge of a wire product, can render the material useless.
To ensure that delivered products meet our customer’s specification requires a multitude of common metal unit conversions — by us and them. In this “101” article, we break down some of the most common metal units and conversions.
Tired of using slide rules and charts for your conversions?
Check out our all-in-one metals calculator and conversion app.
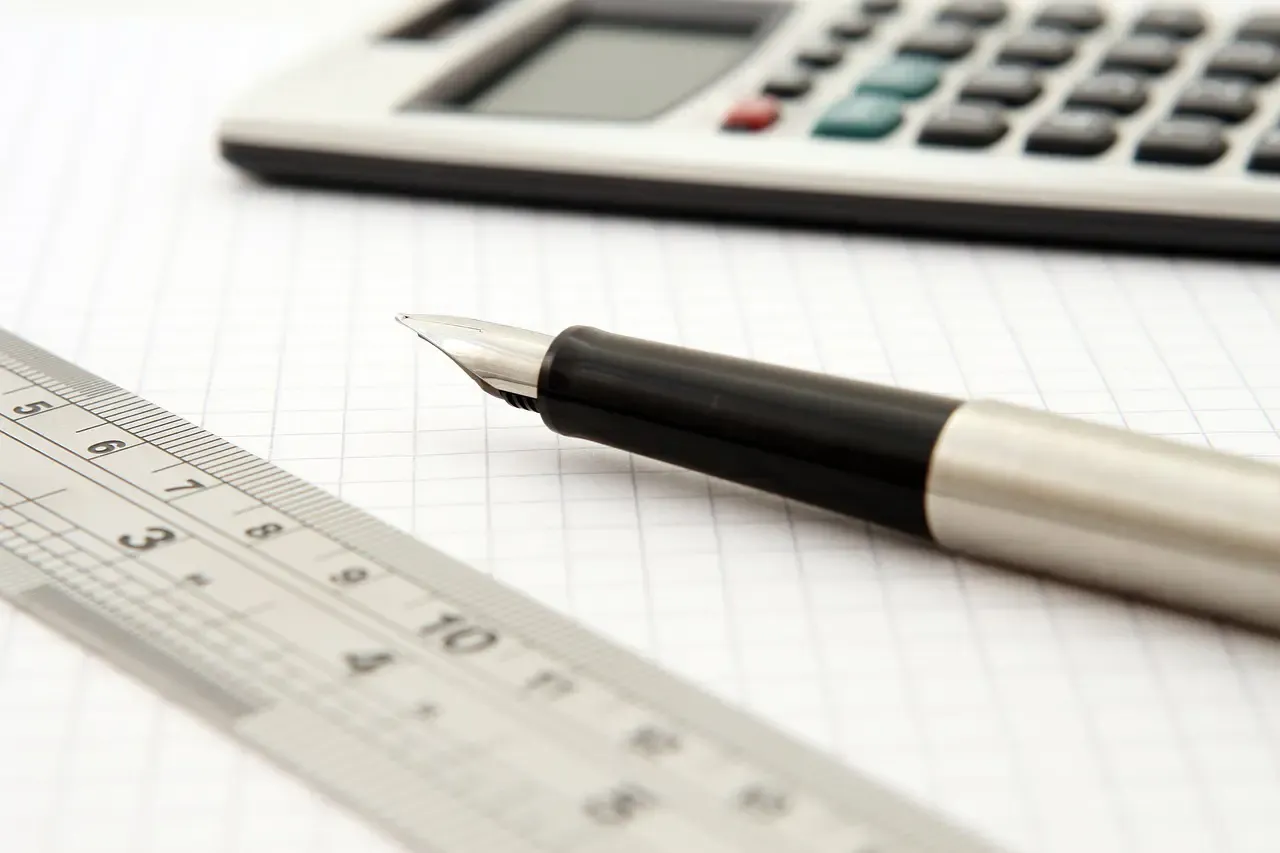
Most Common Metal Measurements
Products like sheet metal, strip/slit coil, and wire are measured in a variety of different ways. Length and mass are the most commonly used when trying to optimize material usage during any manufacturing process. This can help reduce scrap during processing, reduce wear and tear on tooling, in addition to numerous other benefits.
Length and Distance Measurements
Size dimensions like length and distance can be shown as customary units like inches, feet or a metric unit like a millimeter or centimeter.
Sheet metal thickness is typically measured in millimeters, inches, or fractions! Wire, on the other hand, has another option: AWG (American wire gauge), usually referred to as gauge. Gauge is described numerically: the higher the number, the thinner the metal.
Mass, Density, and Weight Measurements for Metal
Mass, density, and weight are related concepts in physics but refer to different properties of sheet metal, strip/slit coil, and wire.
Mass is a measure of the amount of matter in an object. It's an intrinsic property and doesn't change regardless of an object's location. The SI unit for mass is the kilogram (kg). Mass is often confused with weight, but they are different. For instance, an object with a mass of 10 kg will have the same mass whether it's on Earth, the moon, or in space.
Density is the amount of mass in a given volume of a substance. It's a measure of how tightly packed the matter in an object is. Mathematically, density is calculated by dividing the mass of an object by its volume. For example, a material with a high density has more mass packed into a smaller volume compared to a material with a lower density. The unit for density is typically kilograms per cubic meter (kg/m³).
Weight is the force exerted on an object due to gravity. It's directly proportional to the mass of an object and the acceleration due to gravity. Weight can change based on the gravitational pull acting on an object. For instance, an object on Earth will have a different weight than the same object on the moon because the gravitational pull is different. Weight is measured in newtons (N) or pounds (lbs).
In short, mass is the amount of matter in an object, density is the mass per unit volume of a substance, and weight is the force exerted on an object due to gravity.
Measurements for Wire
Wire products have different shapes and properties than sheet metal and require different measurements like diameter and circumference.
When working with wire solutions, it’s important to be accurate and ensure that units are converted when reading blueprints to ensure the shape is exactly as described.
Since metal wire products are used the world over, their measurements must often be converted between the imperial and metric systems.
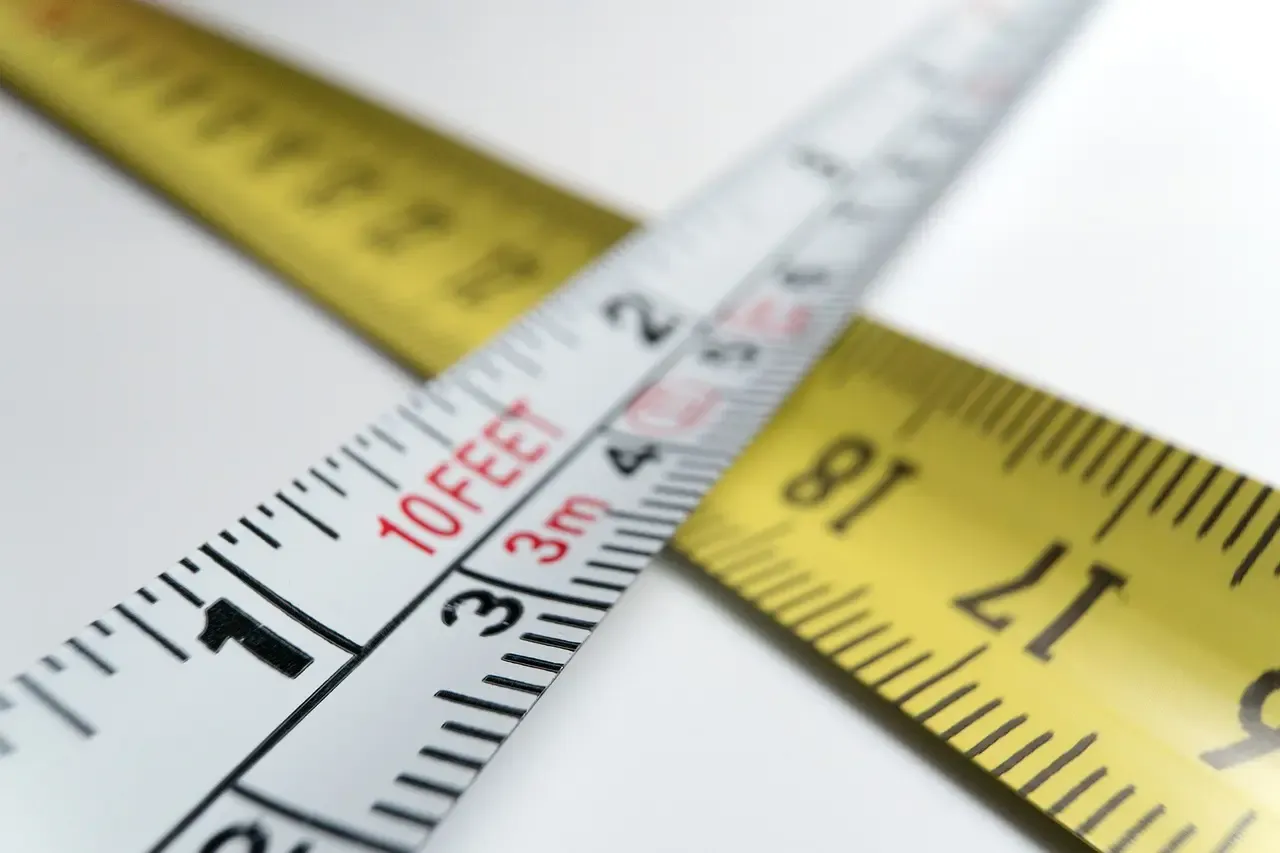
Imperial Versus Metric Metal Units
It’s important to recognize that there are major differences between the US imperial system and the metric system. When doing business internationally, like when there is a language barrier, it can take some time to translate.
Differences Between Metric and Imperial Measurements
The metric system is the most popular system internationally. It’s relatively simple to understand thanks to the base unit (or SI unit) such as a meter or gram. Conversely, the US’s imperial system has its own measurement set called “customary units” like the inch, foot, ounce, and pound.
History of Measurement Systems
The imperial system originated in the United Kingdom and was brought to the US via colonization. However, most of Europe ultimately adopted France’s metric system to simplify international trade.
Despite occasional interest in going metric, the US has kept imperial measurements due to large time and money requirements. Over time, the imperial system has evolved to create a unique difference between US and British measurements.
Difference between the U.S. and British Imperial Systems
Despite different unit names, the main difference between the metric and customary system is volume. While Americans use ounces and pounds to describe weight, metric system users describe mass using the gram. Volume is an important measurement and must be applied in both systems.
Application of Metric and Imperial Measurements
As international trade increased throughout history, industries needed to communicate accurate measurements to potential customers worldwide. This led to many metal fabrication companies including both imperial and metric units for the most common measurements.
Most Common Measurements for Metal Products
The most common measurements that metal fabrication companies use are length, thickness/gauge, hardness, and density.
When it comes to deciding which measurement system is best, there’s certainly room for debate. Ultimately, what matters most is that the measurements and any conversions are accurate.
Challenges in Measuring Metal
One challenge is converting one system’s units to the other. Conversion formulas exist, but since a metal product must be an exact size, weight, and density, any error in the formula can cause issues. Nowadays, machinery can be calibrated to convert the metal units between systems.
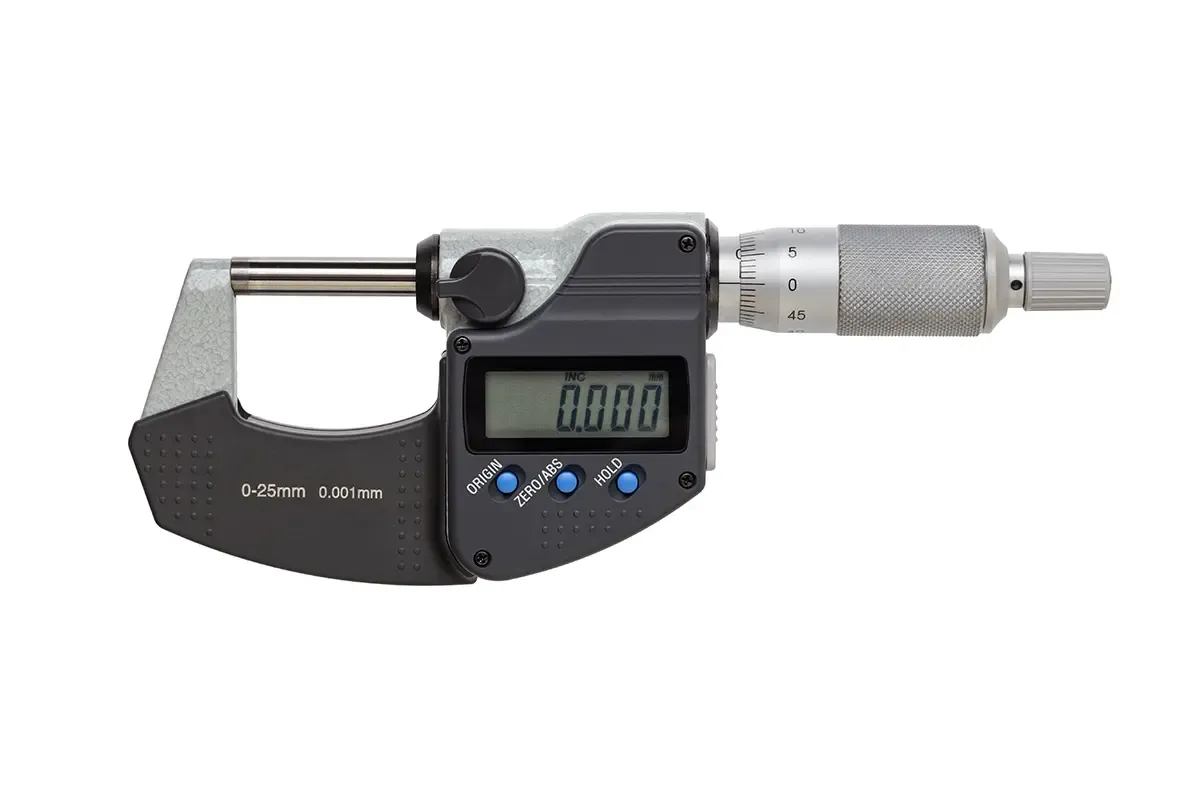
Metal Unit Conversions
To provide customers with understandable specifications, metal fabrication companies can employ unit conversion processes between the imperial and metric systems.
Unit Conversion Process
Without machinery that can provide both metric and imperial measurements, companies can use a unit conversion calculator to perform dimensional analysis. Just be sure to use the correct conversion factor to ensure accurate calculations.
Conversion Factors
Careful attention must be paid to conversion factors when converting measurements between customary units and metric units. Here are a few conversion factors that metal fabrication companies might use:
- 1 inch = 25.4 milimeters or 0.0254 meters
- 1 pound = 453.6 grams or 0.4536 kilograms
- Degrees Celsius = Degrees Farenheit minus 32, multiplied by 5/9
Different products will have different specs and conversion factors, so additional measurements may be required.
Metal Identity
Since gauge is correlated with the weight of the actual material, it’s classified differently depending on the actual metal being used—and can help identify the material itself. This is because different metals have different densities, which also affects their weight.
For instance, a cubic centimeter of steel weighs more than a cubic centimeter of aluminum. So, 18 gauge steel will be thicker than the same gauge aluminum or nickel alloys.
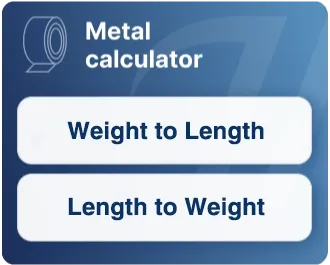
Work More Efficiently with Ulbrich’s Metals Calculator
We searched far and wide for a single app that contained all the unit converters and metal calculators that our team uses on a daily basis. When we couldn’t find one, we built one from scratch that contains all the tools needed to make a maker’s life easier.
Learn more about our calculator that puts essential tools at your fingertips or contact an Ulbrich specialist to learn more about our capabilities.