Grade 9 vs Grade 5 Titanium Comparison: Choosing The Right Titanium Alloy For The Job
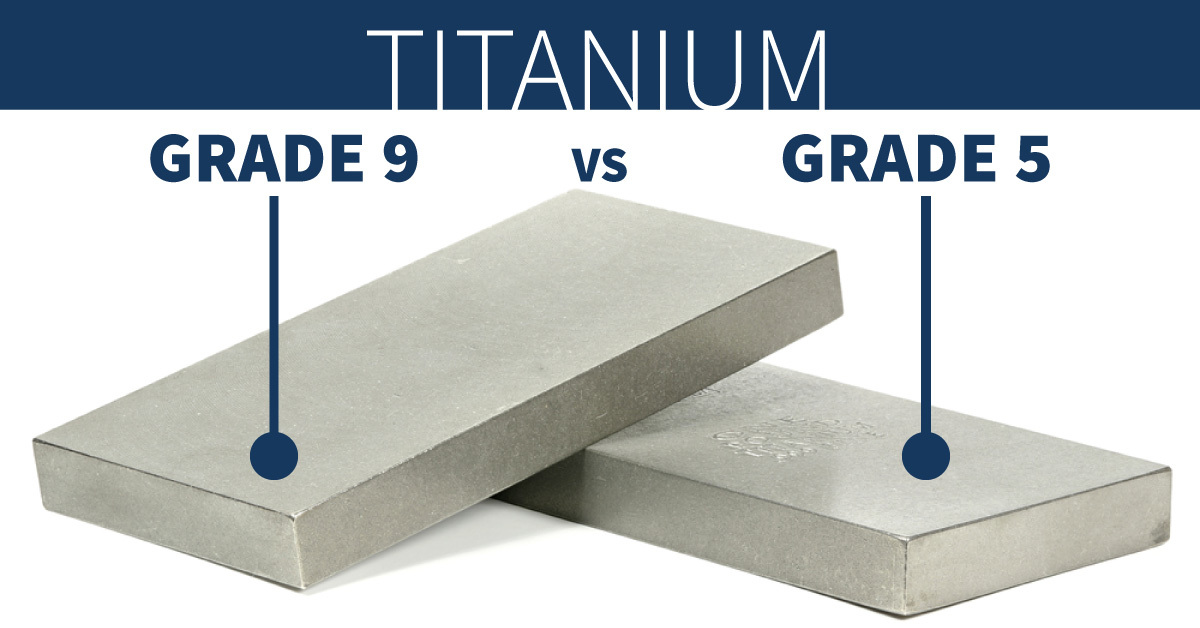
Comparing Grade 9 Titanium vs. Grade 5 Titanium Characteristics
For decades Grade 5, 6-4 titanium has dominated the titanium discussion when it comes to manufacturing applications, mainly due to the extensive use of this workhorse alloy for military and advanced aerospace applications. Grade 5 Titanium documentation abounds and since it has traditionally been the most commercially available titanium alloy it's more well known. What isn't so well known is the fact that while Grade 5 Titanium alloy is twice as strong its low formability makes it twice as hard to work with than Grade 9 Titanium. While both alloys are excellent, Grade 5 Titanium isn't always the best titanium choice for cost-effective, precision production applications in the aerospace, automotive, medical, oil, gas, and power generation industries.
Grade 9 Titanium (3-2.5) is frequently the superior choice for a wide range of applications in industries across the board, perfectly suitable for producing high-tech products ranging from medical pacemakers to aerospace honeycomb.
Titanium Grade 9's mechanical properties offer much more strength than commercially pure titanium. One of the main benefits of this Titanium alloy with 3% Aluminum, 2.5% Vanadium is that it can be cold worked, unlike Ti-6-4,
resulting in good ductility, moderately high strength, and excellent resistance to corrosion.
Both Grade 5 and Grade 9 are alpha-beta titanium alloys with 90% of their alloy composition in common but when production, labor, and manufacturing costs are considered there are distinct differences. Both are superior metals with excellent strength and corrosion-resistant characteristics. Using Ti 6-4 when Ti 3-2.5 alloy can easily meet your component specifications can most definitely have a negative impact on your bottom line. Application is always the determining factor when it comes to making the choice between Grade 5 or Grade 9 titanium.
Welding titanium in either grade can be a difficult process, requiring a specific atmosphere and advanced techniques such as MIG, TIG, plasma arc, and electron beam. NASA has a 217-page document Welding Procedures For Titanium and Titanium Alloys which details the current state of the art which includes pre-weld cleaning, post-weld cleaning and operations, and joint design. The inherent manufacturing costs and technical precision required for working with titanium makes it imperative that the most cost-effective grade is used whenever the application permits and for many applications that grade is Titanium 3-2.5.
Elevated Costs With Grade 5 Titanium 6Al-4V
While Grade 5 Titanium is moderately superior to Grade 9 Titanium in some material characteristics such as shear and tensile strength there are serious challenges to using it for manufacturing applications where working with precision rolled coil is optimal.
For demanding applications such as biomedical implants where a material is needed that can emulate bone and high-temperature structural applications in the aerospace industry Grade 5 Titanium (Ti-6Al-4V) is a common choice.
Vanadium is an important alloying element for both Grade 5 and Grade 9 Titanium. When alloyed with Ti, the resulting titanium alloy is significantly stronger than commercially pure titanium while retaining comparable stiffness and thermal characteristics. As mentioned, Grade 5 has properties similar to human bones which makes it the popular choice for orthopedic medical devices. Other more common applications include tension set rings, bicycle parts, and nuts and bolts used in harsh conditions.
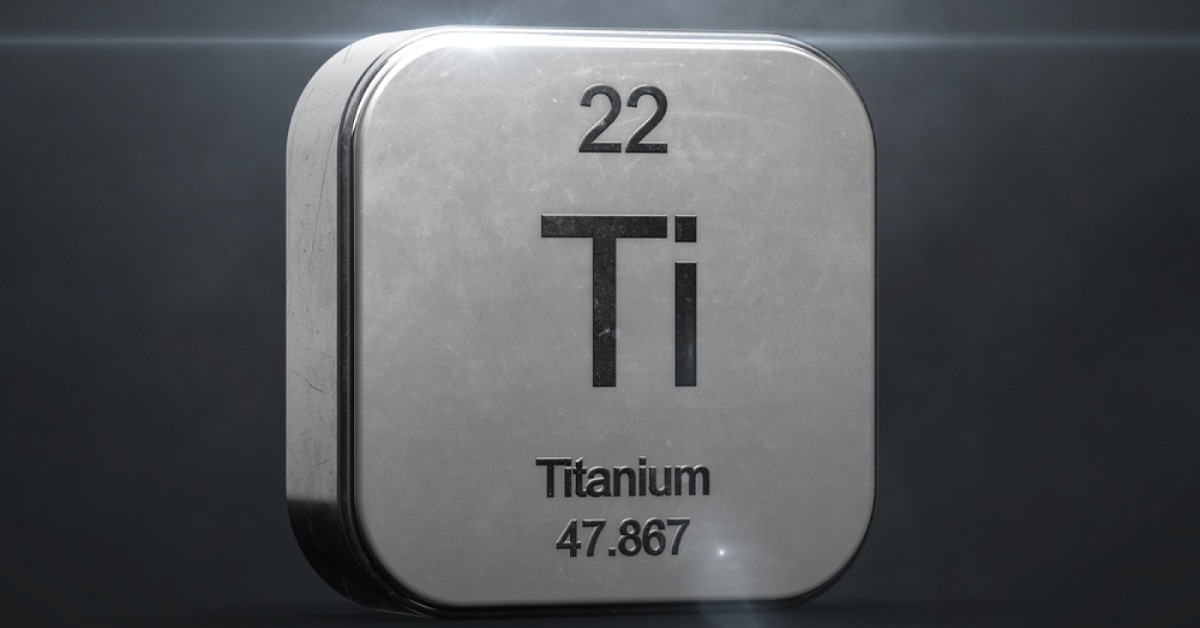
Typically Titanium Grade 5, also known on production floors as "6-4", is used for applications which involve machining. The titanium alloy is most commonly available only in plates and sheets, not coil. Because Grade 5 is not cold-formable, it can't be as efficiently stamped or drawn as Titanium Grade 9 can. It is most often used when no forming is needed because there are better options in formable Titanium Alloys. Grade 5 can be hot formed with contact heating but requires special equipment and considerations that are not as streamlined as the process of batch production when unspooling from a coil.
Grade 5 titanium is a fantastic material that is highly desirable for extremely demanding applications. As a result of higher production costs from vacuum melting and process costs rise and the higher value increases warehousing risk and storage expenses for manufacturers. To achieve the desired thickness Grade 5 must be meticulously cut or ground down, and its use in small gauge applications is severely limited. As a consequence of those cutting and grinding operations, the scrap Grade 5 Titanium material can't be re-melted after it has been mixed with the grinding media which increases the yield loss.
This is why 21st Century manufacturers in all tiers are looking to Titanium 3-2.5 as the solution when strip, foil, or wire gauges are needed for their manufacturing application.
Manufacturing Solutions With Grade 9 Titanium 3Al-2.5V
At Ulbrich, we offer grade 9 titanium as a cold-rolled, more workable alternative to it's 6% Aluminum, 4% Vanadium cousin. Ti 3Al-2.5V is the best option for applications where precision is paramount, and helps to reduce our customers' expenses and enhance the JIT (Just in Time) supply chain which is so prevalent in today's competitive tiered manufacturing environment. Versatile grade 9 titanium 3Al-2.5V is available in wire, foil, and strip coils for ordering on-demand with short lead times to reduce the need to stockpile in costly storage facilities.
Grade 9, or TI 3-2.5 titanium for short, can be rolled down to much smaller gauges making it much more versatile for a wider range of parts and components than grade 5. Grade 9 titanium has excellent corrosion resistance and can be used at higher temperatures than the Commercially Pure Grades 1 through 4. Because it can be cold-rolled and formed, Titanium 3-2.5 is ideal for precision applications in the medical, aerospace, marine, and automotive industries with easier workability and excellent corrosion resistance. Unlike titanium 6-4, grade 9 can be drawn, stamped, and formed, and we can roll it down to extremely thin gauges of .001" or .025mm. Grade 9 is heat treatable with good weldability and is much less difficult to form than Titanium Grade 5 and it can be hardened by cold work and aging. Some common applications include:
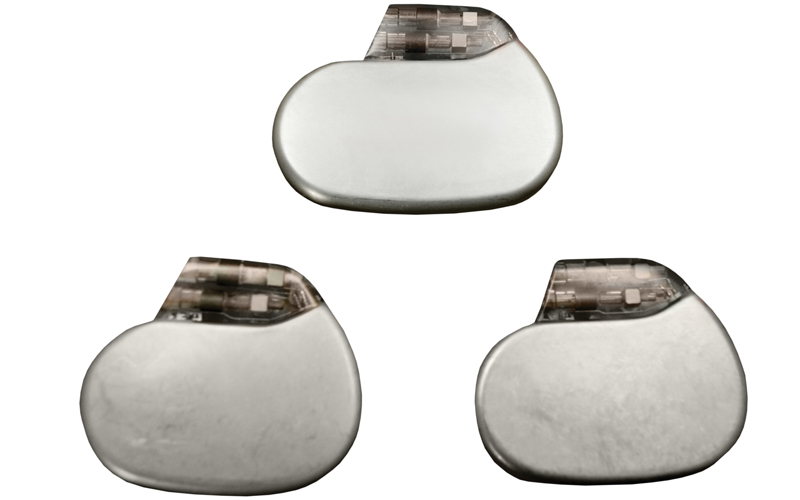
- medical pacemakers
- tennis racquets
- hydraulic tubing
- honeycomb
- golf club shafts
- bellows
Grade 9 titanium is the optimal material solution for many engineers and manufacturers who are seeking a way to bridge the gap of difficulty and expenses that come from working with the commercially pure grades of titanium and the grade 5 titanium alloy.
At Ulbrich Stainless Steel & Special Metals, we offer Grade 9 titanium in a variety of gauge ranges and product forms, ensuring flexibility for your project’s specific requirements. Whether you need quantities for small-scale prototypes or large production runs, we can meet your needs. For those interested in exploring how Grade 9 titanium performs in their applications, we offer trial opportunities to help refine your decision-making process.
If you're considering Grade 9 titanium or another alloy for your next project, don’t hesitate to reach out to one of our Ulbrich specialists for a consultation. Ready to get started? Click below to get a quote on Titanium and explore how Ulbrich can deliver tailored solutions for your metal needs.